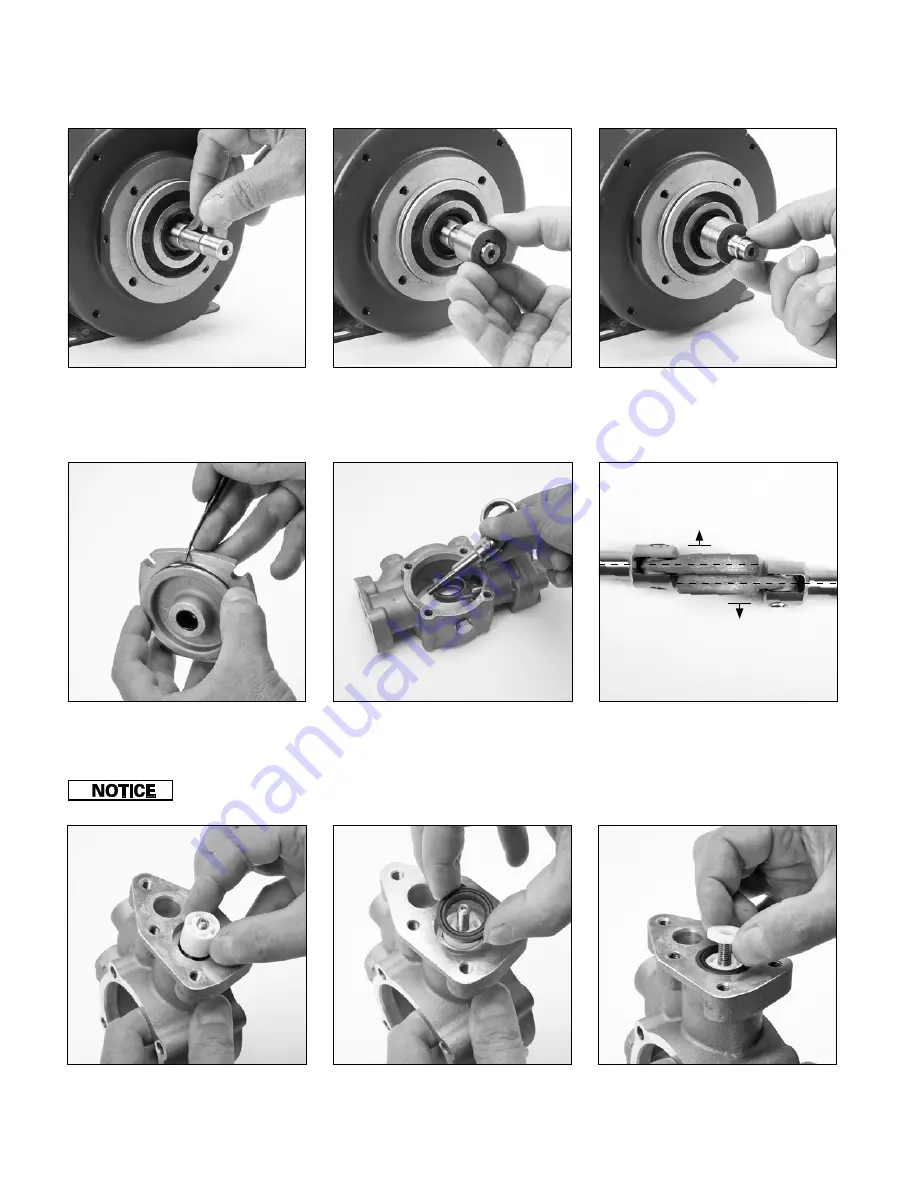
14
6.11 Install plunger rod/connecting rod
assembly through large opening in
crankcase body (1).
Be careful not to damage the bushing ID in the case, as the plunger rod thread passes through the bushing.
6.12 Protruding cast face of connecting
rods should face away from each other
inside crankcase (1).
Out
Eliminates
Interference
Out
6.15 Install inlet valve (20) with flat side
down onto plunger (21).
6.14 Lightly lubricate and install high
pressure seal (22) with v-groove facing
up over ceramic plunger (21).
6.13 Install ceramic plunger (21) with
recessed face away from crankcase.
Pump Reassembly continued
6.10 Lubricate and install o-ring (6) onto
bearing cover (5).
6.9 Install retaining ring (7) into snap
ring groove on motor shaft to secure
cam (8). (Keyed Shaft only).
6.7 Lubricate and install woodruff key (9)
into motor shaft keyway. (Keyed Shaft
only).
6.8 Lubricate and install cam (8) over
motor shaft and key. Position cam (8)
so stamped cam ID number is facing
pump. (Keyed Shaft only).