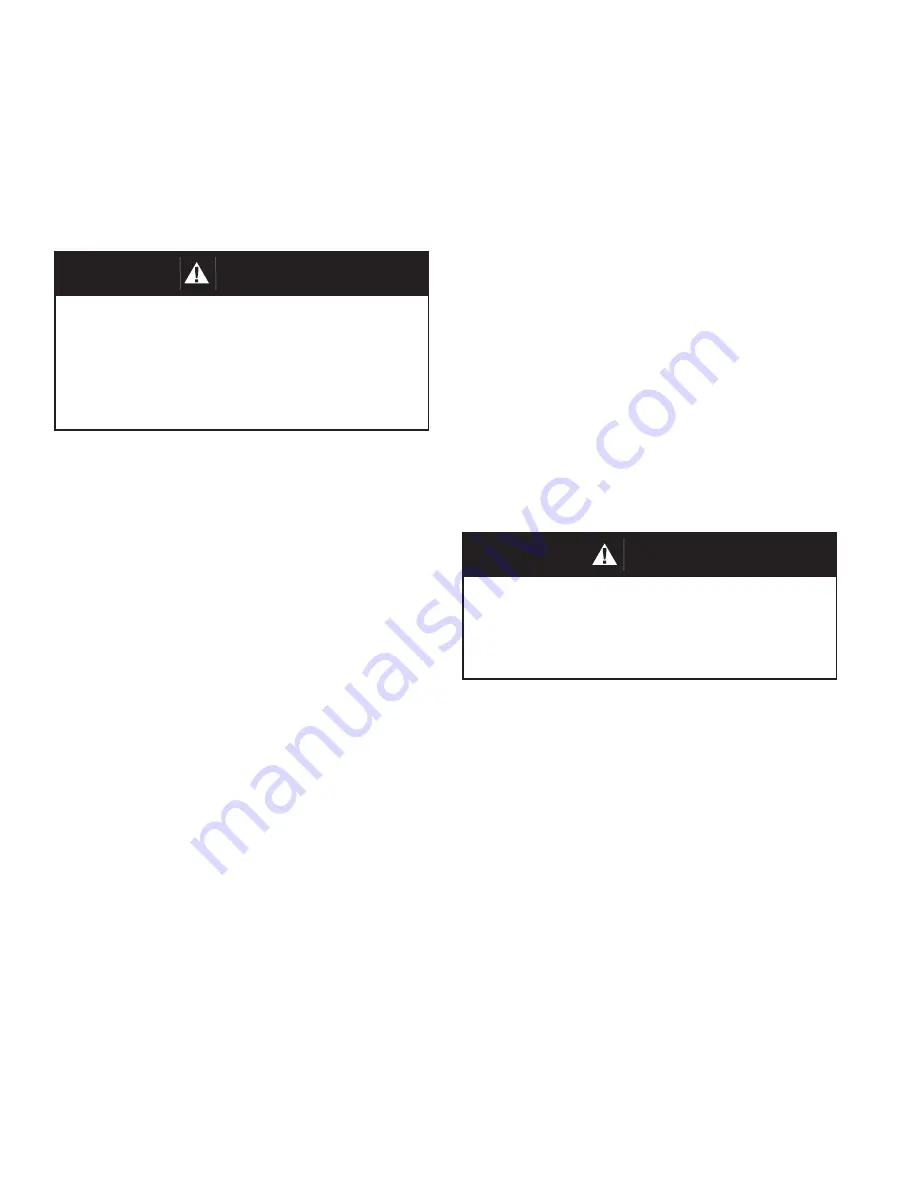
IOM-POSR-1
2
to a point downstream at gauge location; use
1/4" OD metal tubing for dis tanc es 4 ft (1.2 m)
or less, and 3/8" OD metal tubing (requires
1/4" x 3/8" tubing adapter) for distances
greater than 4 ft. (1.2 m). The sensing line
should always be sloped down ward so that
condensation will drain away from the pilot.
If regulator pipe line is ex pand ing to a larger
pipe line, always connect sens ing line to the
larger pipe line.
NOTE:
The POSR-1-20 does
not require a sensing line.
10. For best per for mance Cashco rec om mends
in stall ing regulator in a well drained horizontal
pipe, prop er ly trapped.
11. Recommended installation is with pilot valve
spring chamber vertical upwards. Orient such
that the spring chamber vent hole does not
collect rainwater or debris.
12. Regulators are not to be buried underground.
13. For insulated piping systems, rec om men da tion
is to not insulate regulator.
This increases the loading pres sure on
the main valve’s plug and opens valve.
Partially closing the pilot valve’s plug will
reduce its flow to less than the amount
bleed ing downstream, and allows the loading
pressure on the main valve’s diaphragm to
de cay, allowing partial closing of the main
valve’s plug. This continues until steady-state
is de vel oped.
4. The pilot valve’s diaphragm(s) senses the
down stream (P
2
) pressure and compares the
force generated to the force developed by the
pilot’s range spring.
5. If, during operation, the downstream (P
2
)
pres sure falls below the pilot valve’s setpoint,
the main valve’s diaphragm senses the
reduced pres sure on its underside and instantly
moves down, increasing the flow through the
main valve. At the same time, the pilot valve
5. All installations should include a down stream
re lief device if the inlet pressure could ex ceed
the pressure rating of any downstream
equip ment or the maximum allowable outlet
pres sure rating of the unit.
6. Clean the piping of all foreign material in clud ing
chips, welding scale, oil, grease and dirt
before installing the regulator. Strainers are
recommended.
III. PRIN CI PLE OF OPERATION
A. General:
1. The POSR-1 pilot obtains its operating
medium from the main valve body inlet.
Down stream pressure (P
2
) registers on the
un der side of the main valve’s diaphragm and
the pilot valve’s diaphragm(s).
2. The loading pressure on the top side of the
main valve’s diaphragm is an intermediate
pressure higher than the downstream (P
2
)
pres sure by the sum of the pressures re quired
to overcome the main valve’s plug unbalance
force and the piston spring’s force.
3. The pilot has a bleed orifice that continuously
bleeds part of the loading medium down stream.
In op er a tion, the pilot valve’s plug can flow
more medium than is bleeding down stream.
SECTION III
CAUTION
For welded installations, all internal trim parts, seals and
diaphragm(s) must be removed from reg u la tor body prior
to welding into pipeline. The heat of fusion welding will
dam age non-metallic parts if not re moved. NOTE: This
does not apply to units equipped with extended pipe
nip ples.
CAUTION
DO NOT HYDROSTATIC TEST THROUGH AN IN STALLED
UNIT, INCLUDING PILOT; ISOLATE BOTH PILOT AND MAIN
VALVE FROM TEST. The upper range spring pressure
level listed on the nameplate is the rec om mend ed “upper
op er a tive limit” for the sens ing diaphragm(s) in the pilot.
Higher pres sures could cause internal dam age. In addition,
note on the name plate that the Inlet and Outlet pressure
and tem per a ture rat ings are at different levels.
7. In placing thread sealant on pipe ends prior to
en gage ment, assure that excess material is
removed and not allowed to enter the reg u la tor
upon start-up.
8. Flow Direction. Install so the flow direction
match es the arrow cast on the body.
9. The POSR-1 comes factory piped between the
pilot supply and pilot loading. Install an external
sensing line from the 1/4" NPT con nec tion
opposite the factory piped pilot load ing port