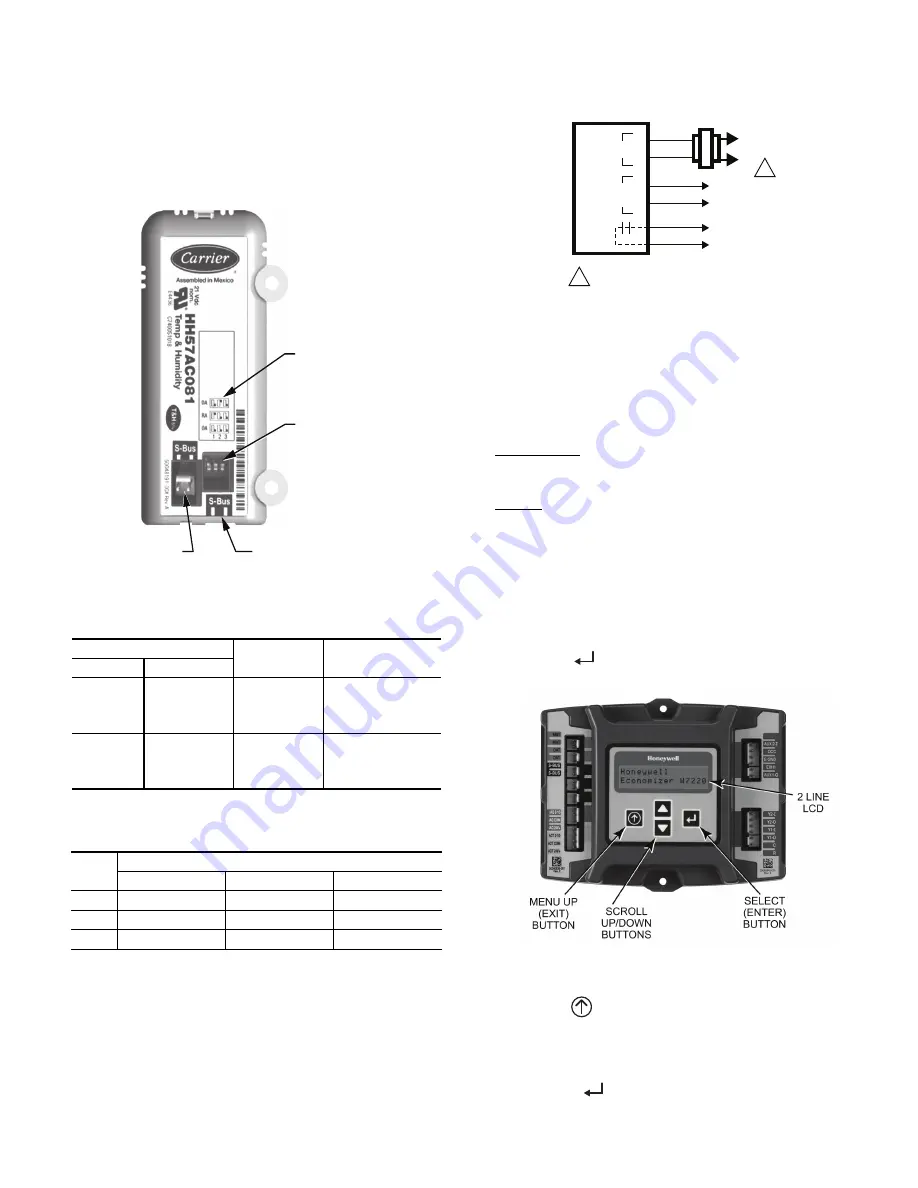
31
S-Bus Sensor Wiring
The labels on the sensors and controller are color coded
for ease of installation. Orange labeled sensors can only be
wired to orange terminals on the controller. Brown labeled
sensors can only be wired to S-bus (brown) terminals. Use
Fig. 50 and Table 9 to locate the wiring terminals for each S-
Bus sensor.
Use Fig. 50 and Table 9 to locate the wiring terminals for
each enthalpy control sensor.
Fig. 50 — S-Bus Sensor DIP Switches
Table 9 — HH57AC081 Sensor Wiring Terminations
Use Fig. 50 and Table 10 to set the DIP switches for the
desired use of the sensor.
Table 10 — HH57AC081 Sensor DIP Switch
NOTE: When an S-Bus sensor is connected to an existing net-
work, it will take 60 minutes for the network to recognize and
auto-configure itself to use the new sensor.
During the 60-minute setup period, no alarms for sensor
failures (except SAT) will be issued and no economizing
function will be available.
CO
2
Sensor Wiring
When using a CO
2
sensor the black and brown common
wires are internally connected and only one is connected to
“IAQ COM” on the W7220. Use the power from the W7220
to power the CO
2
sensor OR make sure the ground for the
power supplies are common. See Fig. 51 for CO
2
sensor wir-
ing.
Fig. 51 — CO
2
Sensor Wiring
Interface Overview
This section describes how to use the EconoMi$er
®
user
interface for:
• Keypad and menu navigation
• Settings and parameter changes
• Menu structure and selection
User Interface
The user interface consists of a 2-line LCD display and a
4-button keypad on the front of the economizer controller.
Keypad
Use the four navigation buttons (see Fig. 52) to scroll
through the menus and menu items, select menu items, and to
change parameter and configuration settings.
To use the keypad when working with menus:
• Press the
▲
(Up arrow) button to move to the previous
menu.
• Press the
▼
(Down arrow) button to move to the next
menu.
• Press the
(Enter) button to display the first item in the
currently displayed menu.
Fig. 52 — W7220 Controller Navigation Buttons
Press the
(Menu Up/Exit) button to exit a menu’s item
and return to the list of menus. To use the keypad when work-
ing with Setpoints, System and Advanced Settings, Checkout
tests and Alarms:
1. Navigate to the desired menu.
2. Press the
(Enter) button to display the first item in
the currently displayed menu.
TERMINAL
TYPE
DESCRIPTION
NUMBER
LABEL
1
S-BUS
S-BUS
S-BUS
Communications
(Enthalpy Control
Sensor Bus)
2
S-BUS
S-BUS
S-BUS
Communications
(Enthalpy Control
Sensor Bus)
USE
DIP SWITCH POSITIONS FOR SWITCHES 1, 2, AND 3
1
2
3
DA
OFF
ON
OFF
RA
ON
OFF
OFF
OA
OFF
OFF
OFF
DIP
SWITCH
LABEL
DIP
SWITCHES
(3)
S-BUS
2 PIN SIDE
CONNECTOR
S-BUS
TERMINALS
(1 AND 2)
CO
2
SENSOR
24V
ANALOG
OUT
L1
(HOT)
L2
RED
BLACK
YELLOW
BROWN
ORANGE
GREEN
+
–
POWER SUPPLY. PROVIDE DISCONNECT
MEANS AND OVERLOAD PROTECTION
AS REQUIRED.
1
1
Summary of Contents for WeatherMaker 48KC Series
Page 4: ...4 Fig 2 Unit Dimensional Drawing ...
Page 5: ...5 Fig 2 Unit Dimensional Drawing cont ...
Page 23: ...23 Fig 41 Typical Humidi MiZer Adaptive Dehumidification System Humidistat Wiring ...
Page 25: ...25 Fig 43 Typical Control Wiring Diagram Electro Mechanical with W7212 ...
Page 26: ...26 Fig 44 Typical 48KC 04 06 Power Wiring Diagram 208 230 3 60 Unit Shown ...