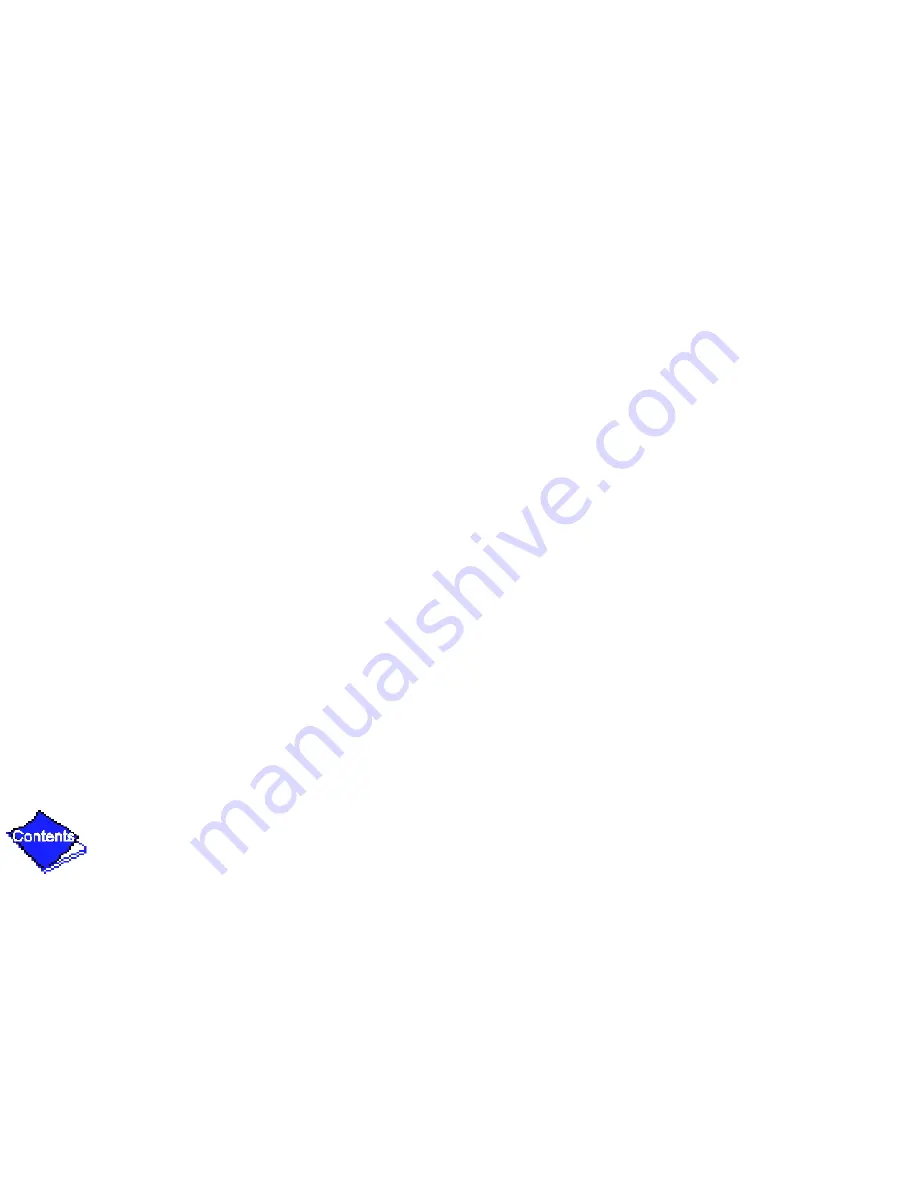
High Discharge Temperature Control
If the discharge temperature increases above 160 F (71.1 C) (PSIO Software Version 09 and
higher) or 180 F (82 C) (PSIO Software Version 08 or lower), the guide vanes are proportionally
opened to increase gas flow through the compressor. If the leaving chilled water temperature is
then brought 5° F (2.8° C) below the control set point temperature, the controls will bring the
machine into the recycle mode.
Oil Sump Temperature Control
The oil sump temperature control is regulated by the PIC which uses the oil heater relay
when the machine is shut down.
As part of the pre-start checks executed by the controls, oil sump temperature is compared
against evaporator refrigerant temperature. If the difference between these 2 temperatures is
50 F (27.8 C) or less, the start-up will be delayed until the oil temperature is 50 F (27.8 C) or
more. Once this temperature is confirmed, the start-up continues.
PSIO Software Version 08 and Lower
The oil heater relay is energized whenever the chiller compressor is off, and the oil sump
temperature is less than 140 F (60 C) or sump temperature is less than the cooler refrigerant
temperature plus 60° F (33.3° C). The heater is then turned off when the oil sump temperature
is: 1) more than 160 F (71.1 C); or 2) the sump temperature is more than 145 F (62.8 C) and
more than the cooler refrigerant temperature plus 65° F (36.1° C). The heater is always off
during start-up or when the compressor is running.
Summary of Contents for PC211
Page 317: ...Figure 1 19XL Identification ...
Page 318: ...Figure 2A Front View Typical 19XL Components Design I See next page for Rear View ...
Page 319: ...Figure 2A Rear View Typical 19XL Components Design I ...
Page 320: ...Figure 2B Front View Typical 19XL Components Design II See next page for Rear View ...
Page 321: ...Figure 2B Rear View Typical 19XL Components Design II ...
Page 322: ...Figure 3 Refrigerant Motor Cooling and Oil Cooling Cycles ...
Page 323: ...Figure 4 Lubrication System ...
Page 324: ...Figure 5 Cutler Hammer Solid State Starter Internal View ...
Page 325: ...Figure 6 Benshaw Inc Solid State Starter Internal View ...
Page 326: ...Figure 7 Typical Starter Front View Solid State Starter Shown ...
Page 327: ...Figure 8 19XL Controls and Sensor Locations ...
Page 328: ...Figure 9 Control Sensors Temperature ...
Page 329: ...Figure 10 Control Sensors Pressure Transducer Typical ...
Page 330: ...Figure 11 Control Panel Front View with Options Module ...
Page 331: ...Figure 12 Power Panel with Options ...
Page 332: ...Figure 13 LID Default Screen ...
Page 333: ...Figure 14 LID Service Screen ...
Page 334: ...Figure 15 Example of Point Status Screen Status01 ...
Page 335: ...Figure 16 19XL Menu Structure ...
Page 336: ...Figure 17 19XL Service Menu Structure ...
Page 337: ...Figure 18 Example of Time Schedule Operation Screen ...
Page 338: ...Figure 19 Example of Set Point Screen ...
Page 339: ...Figure 20 19XL Hot Gas Bypass Surge Prevention ...
Page 340: ...Figure 21 19XL with Default Metric Settings ...
Page 341: ...Figure 22 Example of Attach to Network Device Screen ...
Page 342: ...Figure 23 Example of Holiday Period Screen ...
Page 344: ...Figure 25 Typical Wet Bulb Type Vacuum Indicator ...
Page 345: ...Figure 26 19XL Leak Test Procedures ...
Page 346: ...Figure 27 Typical Optional Pumpout System Piping Schematic with Storage Tank ...
Page 347: ...Figure 28 Typical Optional Pumpout System Piping Schematic without Storage Tank ...
Page 348: ...Figure 29 Dehydration Cold Trap ...
Page 349: ...Figure 30 Benshaw Inc Solid State Starter Power Stack ...
Page 350: ...Figure 31 Ramp Up and Starting Torque Potentiometers ...
Page 351: ...Figure 32 Typical Potentiometer Adjustment ...
Page 352: ...Figure 33 Typical Cutler Hammer Solid State Starter ...
Page 353: ...Figure 34 Correct Motor Rotation ...
Page 356: ...Figure 37 Optional Pumpout System ...
Page 357: ...Figure 38 Guide Vane Actuator Linkage ...
Page 358: ...Figure 39 19XL Float Valve Designs ...
Page 359: ...Figure 40 Optional Pumpout System Controls ...
Page 360: ...Figure 41 PSIO Module Address Selector Switch Locations and LED Locations ...
Page 361: ...Figure 42 LID Module Rear View and LED Locations ...
Page 362: ...Figure 43 Processor PSIO Module ...
Page 363: ...Figure 44 Starter Management Module SSM ...
Page 364: ...Switch Setting Option Module 1 Option Module 2 S1 S2 6 4 7 2 Figure 45 Options Module ...
Page 365: ...Figure 46 Typical Benshaw Inc Solid State Starter Internal View ...
Page 366: ...Figure 47 Resistance Check ...
Page 367: ...Figure 48 SCR and Power Poles ...
Page 368: ...Figure 49 Typical Cutler Hammer Solid State Starter Internal View ...
Page 369: ...Figure 50 Cutler Hammer Terminal Functions ...
Page 370: ...Figure 51 Solid State Starter General Operation Troubleshooting Guide Typical ...
Page 373: ...Figure 54 Compressor Fits and Clearances Continued ...
Page 374: ...Figure 55 Compressor Fits and Clearances Continued ...