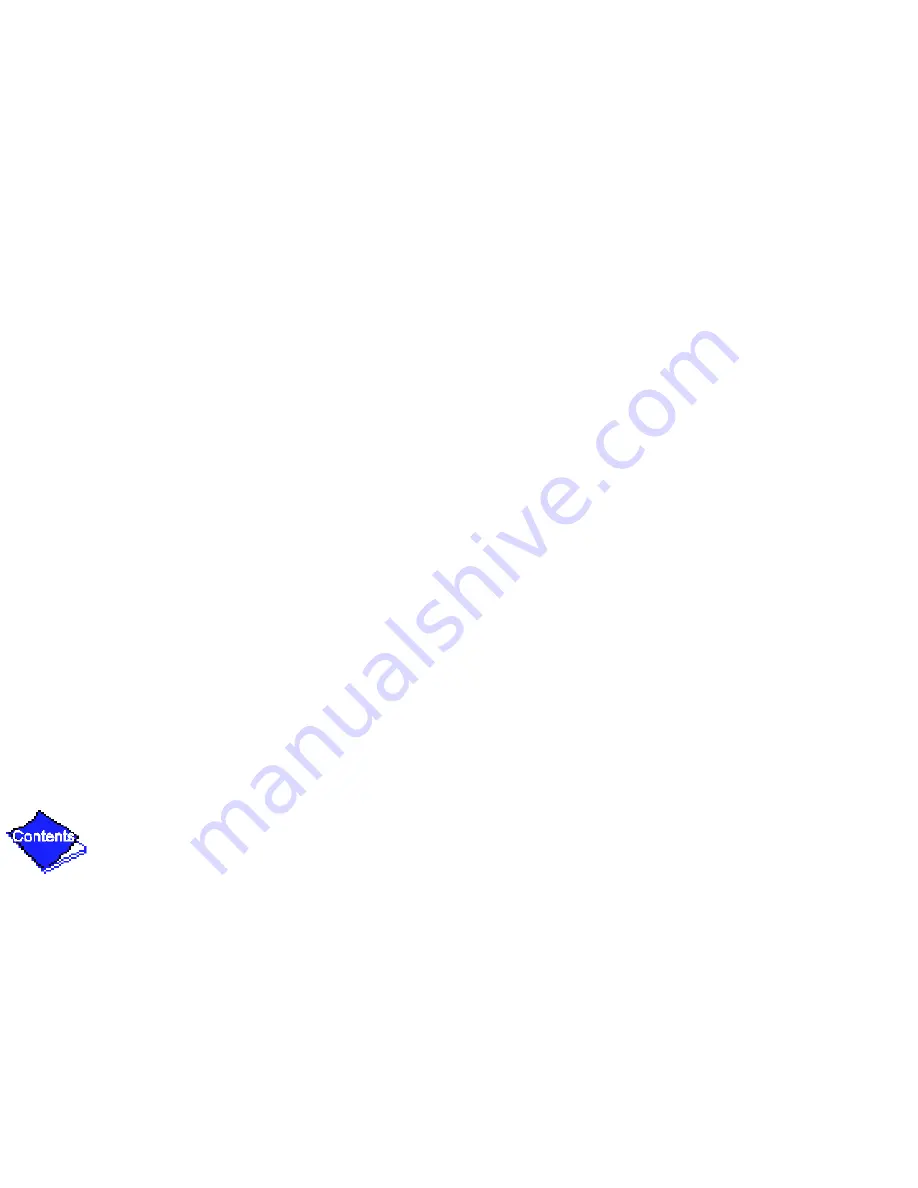
The oil pump suction is fed from the oil reservoir. An oil pressure relief valve maintains 18 to
25 psid (124 to 172 kPad) differential pressure in the system at the pump discharge. This
differential pressure can be read directly from the Local Interface Device (LID) default screen.
The oil pump discharges oil to the oil filter assembly. This filter is capable of being valved closed
to permit removal of the filter without draining the entire oil system (see
Maintenance
sections
for details). The oil is then piped to the oil cooler. This heat exchanger uses refrigerant from the
condenser as the coolant. The refrigerant cools the oil to a temperature between 100 and 120 F
(37 to 49 C).
As the oil leaves the oil cooler, it passes the oil pressure transducer and the thermal bulb for
the refrigerant expansion valve on the oil cooler. The oil is then divided, with a portion flowing to
the thrust bearing, forward pinion bearing, and gear spray. The balance then lubricates the
motor shaft bearings and the rear pinion bearing. The oil temperature is measured as the oil
leaves the thrust and forward journal bearings within the bearing housing. The oil then drains
into the oil reservoir at the base of the compressor. The PIC (Product Integrated Control)
measures the temperature of the oil in the sump and maintains the temperature during
shutdown (see
Oil Sump Temperature Control
section). This temperature is read on the LID
default screen.
During the machine start-up, the PIC will energize the oil pump and provide 15 seconds of
prelubrication to the bearings after pressure is verified before starting the compressor. During
shutdown, the oil pump will run for 60 seconds after the compressor shuts down for the purpose
Summary of Contents for PC211
Page 317: ...Figure 1 19XL Identification ...
Page 318: ...Figure 2A Front View Typical 19XL Components Design I See next page for Rear View ...
Page 319: ...Figure 2A Rear View Typical 19XL Components Design I ...
Page 320: ...Figure 2B Front View Typical 19XL Components Design II See next page for Rear View ...
Page 321: ...Figure 2B Rear View Typical 19XL Components Design II ...
Page 322: ...Figure 3 Refrigerant Motor Cooling and Oil Cooling Cycles ...
Page 323: ...Figure 4 Lubrication System ...
Page 324: ...Figure 5 Cutler Hammer Solid State Starter Internal View ...
Page 325: ...Figure 6 Benshaw Inc Solid State Starter Internal View ...
Page 326: ...Figure 7 Typical Starter Front View Solid State Starter Shown ...
Page 327: ...Figure 8 19XL Controls and Sensor Locations ...
Page 328: ...Figure 9 Control Sensors Temperature ...
Page 329: ...Figure 10 Control Sensors Pressure Transducer Typical ...
Page 330: ...Figure 11 Control Panel Front View with Options Module ...
Page 331: ...Figure 12 Power Panel with Options ...
Page 332: ...Figure 13 LID Default Screen ...
Page 333: ...Figure 14 LID Service Screen ...
Page 334: ...Figure 15 Example of Point Status Screen Status01 ...
Page 335: ...Figure 16 19XL Menu Structure ...
Page 336: ...Figure 17 19XL Service Menu Structure ...
Page 337: ...Figure 18 Example of Time Schedule Operation Screen ...
Page 338: ...Figure 19 Example of Set Point Screen ...
Page 339: ...Figure 20 19XL Hot Gas Bypass Surge Prevention ...
Page 340: ...Figure 21 19XL with Default Metric Settings ...
Page 341: ...Figure 22 Example of Attach to Network Device Screen ...
Page 342: ...Figure 23 Example of Holiday Period Screen ...
Page 344: ...Figure 25 Typical Wet Bulb Type Vacuum Indicator ...
Page 345: ...Figure 26 19XL Leak Test Procedures ...
Page 346: ...Figure 27 Typical Optional Pumpout System Piping Schematic with Storage Tank ...
Page 347: ...Figure 28 Typical Optional Pumpout System Piping Schematic without Storage Tank ...
Page 348: ...Figure 29 Dehydration Cold Trap ...
Page 349: ...Figure 30 Benshaw Inc Solid State Starter Power Stack ...
Page 350: ...Figure 31 Ramp Up and Starting Torque Potentiometers ...
Page 351: ...Figure 32 Typical Potentiometer Adjustment ...
Page 352: ...Figure 33 Typical Cutler Hammer Solid State Starter ...
Page 353: ...Figure 34 Correct Motor Rotation ...
Page 356: ...Figure 37 Optional Pumpout System ...
Page 357: ...Figure 38 Guide Vane Actuator Linkage ...
Page 358: ...Figure 39 19XL Float Valve Designs ...
Page 359: ...Figure 40 Optional Pumpout System Controls ...
Page 360: ...Figure 41 PSIO Module Address Selector Switch Locations and LED Locations ...
Page 361: ...Figure 42 LID Module Rear View and LED Locations ...
Page 362: ...Figure 43 Processor PSIO Module ...
Page 363: ...Figure 44 Starter Management Module SSM ...
Page 364: ...Switch Setting Option Module 1 Option Module 2 S1 S2 6 4 7 2 Figure 45 Options Module ...
Page 365: ...Figure 46 Typical Benshaw Inc Solid State Starter Internal View ...
Page 366: ...Figure 47 Resistance Check ...
Page 367: ...Figure 48 SCR and Power Poles ...
Page 368: ...Figure 49 Typical Cutler Hammer Solid State Starter Internal View ...
Page 369: ...Figure 50 Cutler Hammer Terminal Functions ...
Page 370: ...Figure 51 Solid State Starter General Operation Troubleshooting Guide Typical ...
Page 373: ...Figure 54 Compressor Fits and Clearances Continued ...
Page 374: ...Figure 55 Compressor Fits and Clearances Continued ...