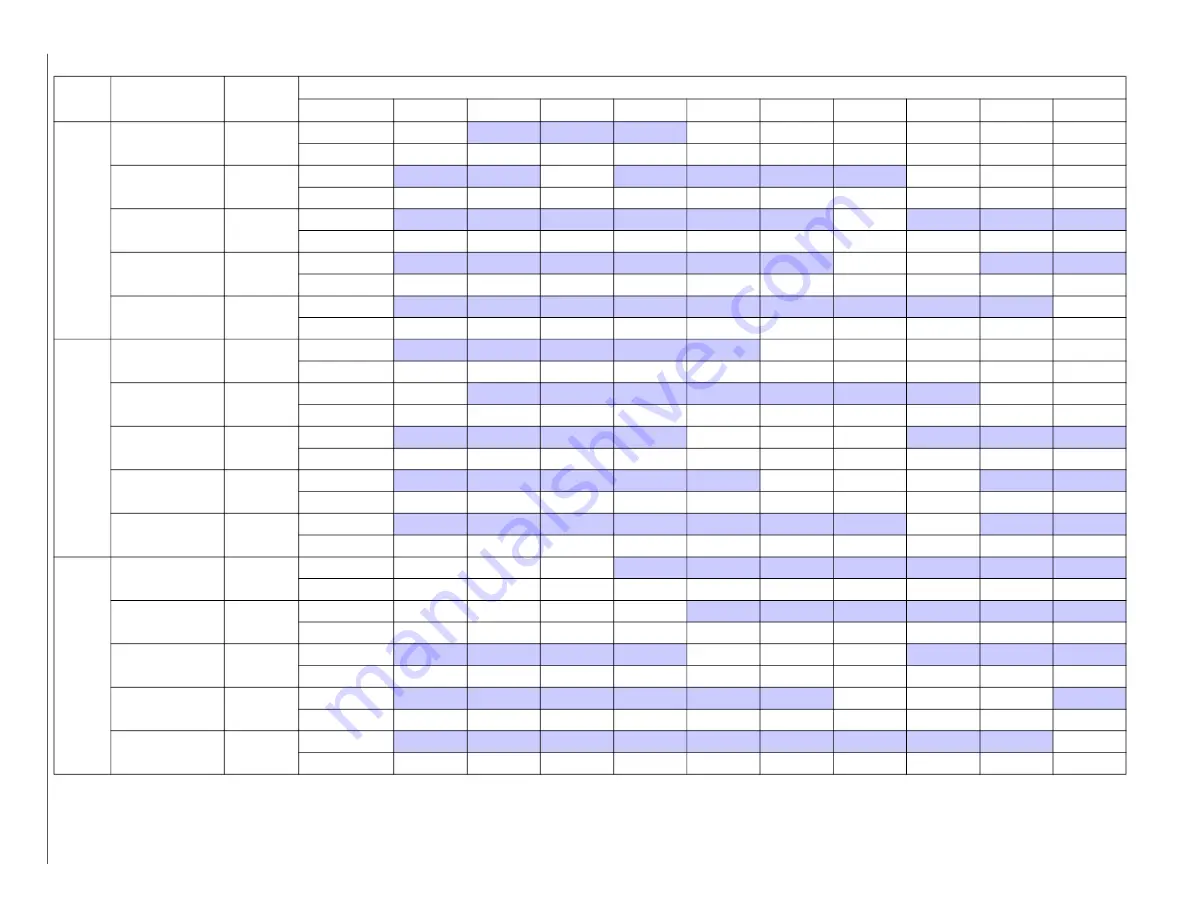
PA
4G
: In
sta
lla
tio
n I
ns
tru
ctio
ns
M
an
ufa
ctu
re
r r
es
erv
es
th
e r
ig
ht
to
ch
an
ge
, a
t a
ny
tim
e, s
pe
cif
ica
tio
ns
an
d d
es
ig
ns
w
ith
ou
t n
oti
ce
an
d w
ith
ou
t o
bli
ga
tio
ns
.
15
Table 4 – Dry Coil Air Delivery* - Horizontal and Downflow Discharge Sizes 24-60
Unit Size
Motor Speed
Tap
ESP (in. W.C.)
0.1
0.2
0.3
0.4
0.5
0.6
0.7
0.8
0.9
1
24
Low
Blue
CFM
640
553
454
310
---
---
---
---
---
---
BHP
0.07
0.08
0.08
0.09
---
---
---
---
---
---
Med-Low
Pink
CFM
830
758
688
607
514
393
254
---
---
---
BHP
0.12
0.13
0.13
0.13
0.14
0.14
0.15
---
---
---
Medium**
Red
CFM
1080
1025
969
910
852
787
718
638
541
457
BHP
0.21
0.22
0.23
0.23
0.24
0.24
0.25
0.25
0.26
0.27
Med-High
Orange
CFM
1101
1046
993
936
878
816
749
676
599
498
BHP
0.22
0.23
0.24
0.24
0.25
0.26
0.26
0.27
0.27
0.28
High
Black
CFM
1222
1173
1123
1072
1021
967
912
853
787
712
BHP
0.29
0.29
0.30
0.31
0.31
0.32
0.33
0.34
0.34
0.34
30
Low
Blue
CFM
643
552
455
348
225
---
---
---
---
---
BHP
0.09
0.10
0.11
0.11
0.11
---
---
---
---
---
Med-Low
Pink
CFM
817
744
673
597
516
431
325
190
---
---
BHP
0.14
0.15
0.15
0.16
0.17
0.17
0.18
0.18
---
---
Medium
Red
CFM
1159
1104
1045
990
937
878
821
759
693
618
BHP
0.31
0.32
0.33
0.33
0.34
0.35
0.36
0.37
0.37
0.38
Med-High**
Orange
CFM
1201
1147
1095
1037
987
934
877
818
755
671
BHP
0.34
0.35
0.36
0.37
0.37
0.38
0.39
0.40
0.41
0.40
High
Black
CFM
1291
1236
1181
1131
1080
1033
978
909
792
661
BHP
0.41
0.42
0.43
0.43
0.44
0.45
0.46
0.45
0.43
0.40
36
Low
Blue
CFM
1096
1044
994
945
892
837
780
717
664
612
BHP
0.14
0.15
0.16
0.18
0.19
0.19
0.20
0.21
0.22
0.23
Med-Low
Pink
CFM
1151
1103
1056
1002
953
897
845
788
729
678
BHP
0.16
0.17
0.18
0.19
0.20
0.21
0.22
0.23
0.24
0.25
Medium
Red
CFM
1299
1252
1204
1155
1106
1059
1007
959
905
844
BHP
0.22
0.23
0.24
0.25
0.26
0.27
0.28
0.29
0.30
0.31
Med-High**
Orange
CFM
1382
1335
1292
1246
1202
1152
1106
1058
1007
957
BHP
0.26
0.27
0.28
0.29
0.30
0.31
0.32
0.33
0.34
0.35
High
Black
CFM
1530
1485
1442
1398
1354
1309
1263
1217
1169
1120
BHP
0.33
0.35
0.36
0.37
0.38
0.39
0.40
0.41
0.42
0.43