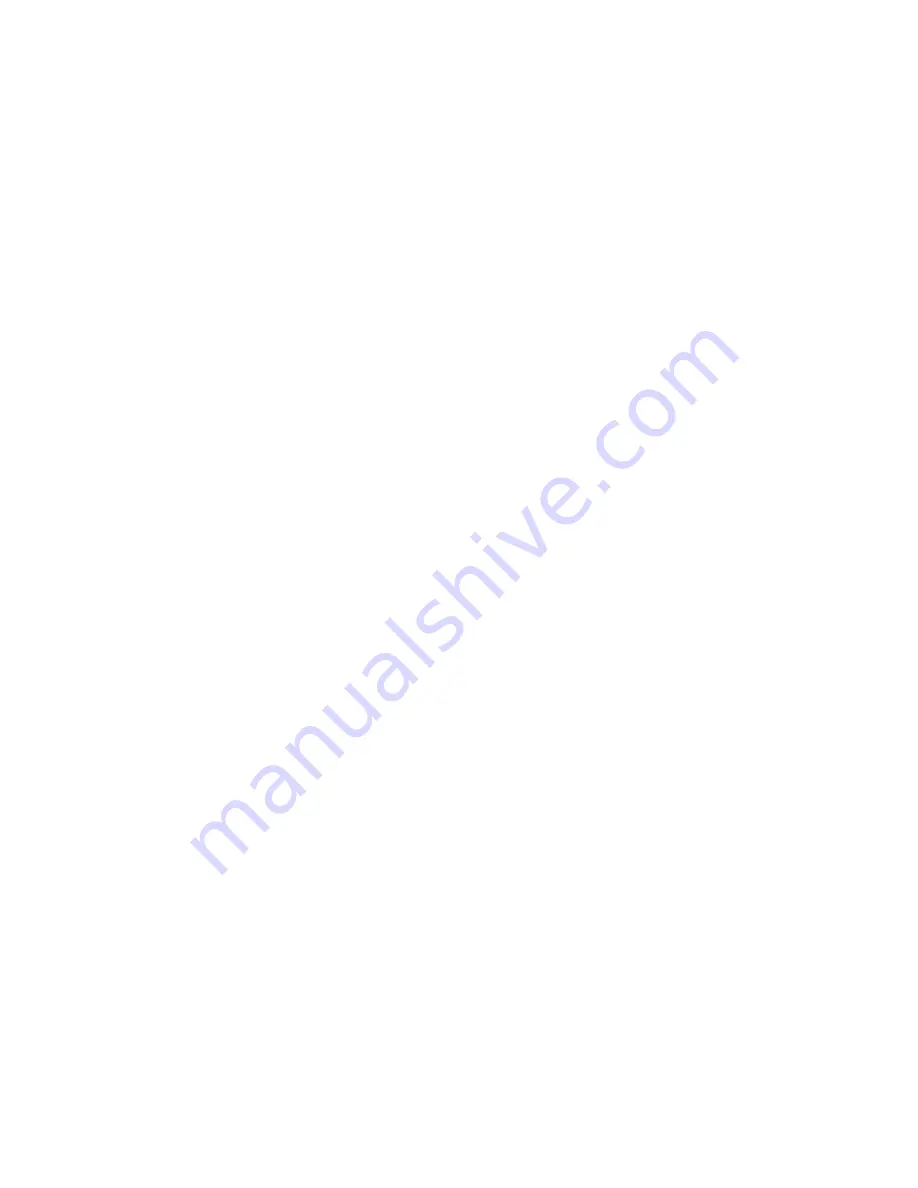
2-11
62-11848
2.8
REFRIGERATION CIRCUIT
2.8.1
Cooling
(See
When cooling, the unit operates as a vapor compression refrigeration system. The main components of the system
are the compressor, air-cooled condenser, thermostatic expansion valve, direct expansion evaporator, and hot gas
solenoid (two-way).
The compressor raises the pressure and temperature of the refrigerant and forces it into the condenser tubes.
The condenser fan circulates surrounding air over the outside of the condenser tubes. Heat transfer is thus established
from the refrigerant gas (inside the tubes) to the air ambient (flowing over the tubes). The condenser tubes have fins
designed to improve the transfer of heat. This removal of heat causes the refrigerant to liquefy; liquid refrigerant flows
from the condenser to the receiver.
The refrigerant then flows through the filter-drier, where an absorbent keeps it dry and clean. The refrigerant then flows
through a sight glass with moisture indication to the check valve and then to the liquid / gas heat exchanger.
The liquid then flows to the thermostatic expansion valve (with external pressure equalizer) which regulates the
flow rate of refrigerant in the evaporator in order to obtain maximum use of the evaporator heat transfer surface.
The evaporator tubes have aluminum fins to increase heat transfer; therefore heat is removed from the air circu-
lated through the evaporator. This cold air is circulated throughout the refrigerated compartment to maintain the
box at the desired temperature.
The transfer of heat from the air to the low temperature liquid refrigerant causes the liquid to vaporize. The vapor at
low temperature and pressure enters the heat exchanger then enters the compressor pressure regulating valve
(CPR) which regulates refrigerant pressure entering the compressor, where the cycle starts over.
The discharge pressure is regulated with HP2.
2.8.2
Heat And Defrost
(See
When refrigerant vapor is compressed to a high pressure and temperature in a compressor, the mechanical energy
necessary to operate the compressor is transferred to the gas as it is being compressed. This energy is referred to
as the “heat of compression” and is used as the source of heat during the heating or defrost cycle.
When the microprocessor activates heating or defrost, the hot gas solenoid valve (HGS1) energizes and the con-
denser pressure control valve (HGS2) energizes, closing the port to the condenser and opening a port which allows
heated refrigerant vapor to flow directly to the evaporator coil.
The main difference between heating and defrosting is that when in heating mode the evaporator fans continue to
run thus circulating the air throughout the compartment to heat the product. When in defrost, the evaporator fans
stop, thus allowing the heated vapor to defrost any ice build-up on the coil.
When the pressure is above the setting of the condenser pressure control switch (HP2), the condenser pressure
control valve (HGS2) is closed to prevent additional pressure rise in the system. When pressure is below the set-
ting of the condenser pressure control switch, the valve is opened to pressurize the receiver and force additional
refrigerant into the system and increase heating capacity.