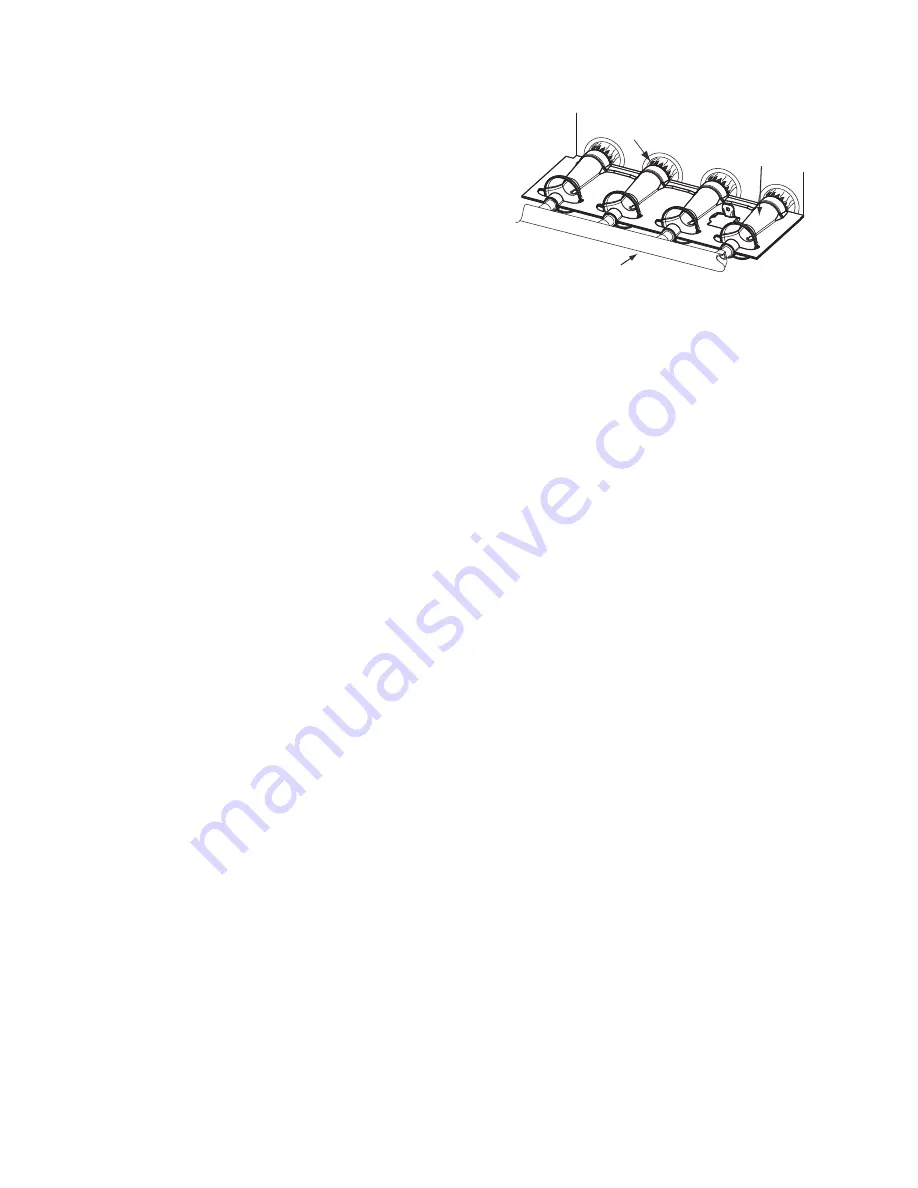
21
Determine natural gas orifice size and manifold pressures for
correct input at installed altitude by using Table 5.
1. Obtain yearly heat--value average (at installed altitude) for
local gas supply.
2. Obtain yearly specific--gravity average for local gas sup-
ply.
3. Find installation altitude in Table 5.
NOTE
: For Canada altitudes of 2000 to 4500 ft. (610 to 1372
M), use U.S.A. Altitudes of 2001 to 3000 ft. (610 to 914 M) in
Table 5.
Furnace gas input rate on rating plate is for installations at
altitudes up to 2000 ft. (610 M).
In the U.S.A., the input rating for altitudes above 2000 ft. (610M)
must be reduced by 2 percent for each 1000 ft. (305 M) above sea
level.
In Canada, the input rating must be derated by 5 percent for
altitudes of 2000 ft. (610 M) to 4500 ft. (1372 M) above sea
level.
The Conversion Kit Rating Plate accounts for high altitude
derate.
SET GAS INPUT RATE
1. Make sure the gas supply is turned off to the furnace and
at the electric switch on the gas valve.
2. Remove the 1/8 inch NPT plug from the outlet pressure
tap on the gas valve.
3. Connect a manometer to the outlet pressure tap on gas
valve.
4. Turn on furnace power supply.
5. Turn gas supply manual shutoff valve to ON position.
6. Turn furnace gas valve switch to ON position.
7. Verify SW1-2 on furnace control is turned “ON”.
8. Jumper R and W/W1 thermostat connections to call for
heat.
9. Check manifold orifices for gas leaks when main burners
ignite.
10. Adjust gas manifold pressure. Refer to Table 5.
11. Remove caps that conceal the adjustment screws for gas
valve regulators. See Fig. 25.
12. Adjust low--heat manifold pressure for natural gas. See
Fig. 25.
13. Turn low--heat adjusting screw counterclockwise (out) to
decrease input rate or clockwise (in) to increase input rate.
NOTE
: When correct input is obtained, main burner flame
should be clear blue, almost transparent (see Fig. 29).
14. Jumper R, W/W1 and W2 on control center thermostat
connections. This keeps furnace locked in high--heat oper-
ation.
15. Adjust high--heat manifold pressure for natural gas.
16. Turn high--heat adjusting screw counterclockwise (out) to
decrease input rate or clockwise (in) to increase input rate.
17. Replace caps that conceal the gas valve regulator adjust-
ment screws.
NOTE
: When correct input is obtained, main burner flame
should be clear blue, almost transparent (see Fig. 29).
Burner Flame
Burner
Manifold
A11461
Fig. 29 -- Burner Flame
18. Remove jumper across R, W1, and W2 after high--heat ad-
justment to terminate call for heat.
19. Turn setup switch SW1-2 on furnace control to OFF posi-
tion.
20. Turn furnace gas valve switch to OFF position.
21. Turn off furnace power supply.
22. Remove manometer and re-install manifold pressure tap
plug.
23. Turn furnace gas valve switch to ON position.
24. Turn on furnace power supply.
25. Set room thermostat to call for heat.
26. Check pressure tap plug for gas leaks when main burners
ignite.
27. Check for correct burner flame.
28. After making the required manifold pressure adjustments,
check and adjust the furnace temperature rise per the fur-
nace installation instructions.
LABEL APPLICATION
1. Fill in Conversion Responsibility Label 340071--205 and
apply to Blower Access Door of furnace as shown. (See
Fig. 30.) Date, name, and address of organization making
this conversion are required.
2. Attach Conversion Rating Plate Label 340071--206, see
Fig. 31, to Outer Door of furnace.
3. Attach Gas Control Conversion label 340071--202 to gas
valve. DO NOT use 340071--203, which is similar.
CHECKOUT
1. Observe unit operation through 2 complete heating cycles.
2. See Sequence of Operation operation in furnace Installa-
tion, Start--Up, and Operating Instructions.
3. Set room thermostat to desired temperature.