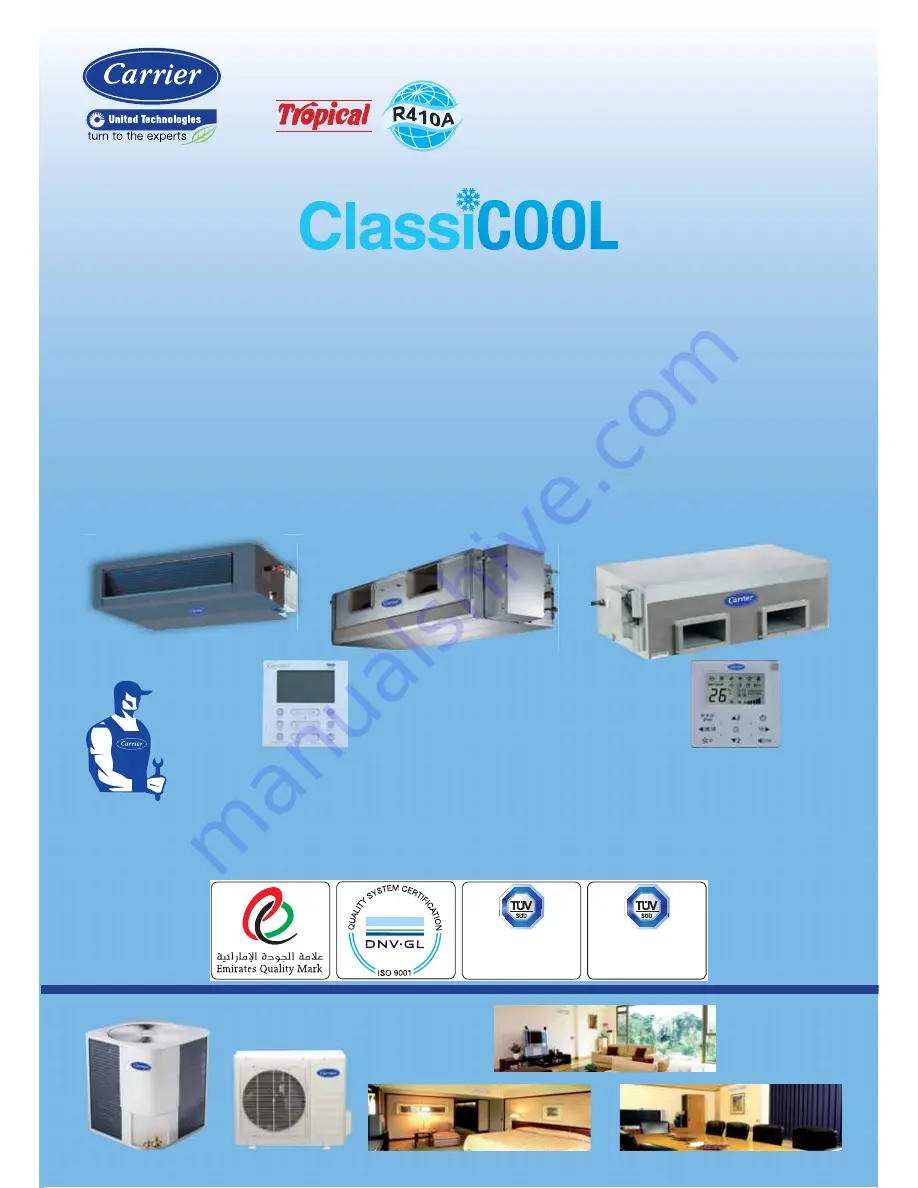
Rev. (0) - 2014
Rev. (0) - 2016
Enviromental
Management System
ISO 14001 : 2004
Certificate No : 12 104 30334 TMS
Safety
Management System
BS OHSAS 18001 : 2007
Certificate No : 12 116 30334 TMS
03504574
INSTALLATION MANUAL
Miraco
Miraco
MISR REFRIGERATION & AIR CONDITIONING MFG. CO.
220-240V ~ 50Hz 1Ph
380-420V ~ 50Hz 3Ph
Carrier is committed for continuous improvement of Carrier products according to national and international standards
to ensure the highest quality and reliability standards, and to meet market regulations and requirements.
All specifications subject to change without prior notice according to Carrier policy of continuous development.
Ceiling Concealed Ducted Split Systems
+
ig
K
(I¿
ciency
*U
een
Cool Only
53KDMT12N-718
53KDMT18N-718
53KDMT24N-718
53KDMT30N-718
53KDMT36N-718T
53KDHT42N-518T
53KDHT48N-518T
53KDHT60N-518T
53KDHT72N-518T
53
36
8
Summary of Contents for ClassiCool 53KDMT12N-718
Page 87: ...83 Notes...
Page 88: ......