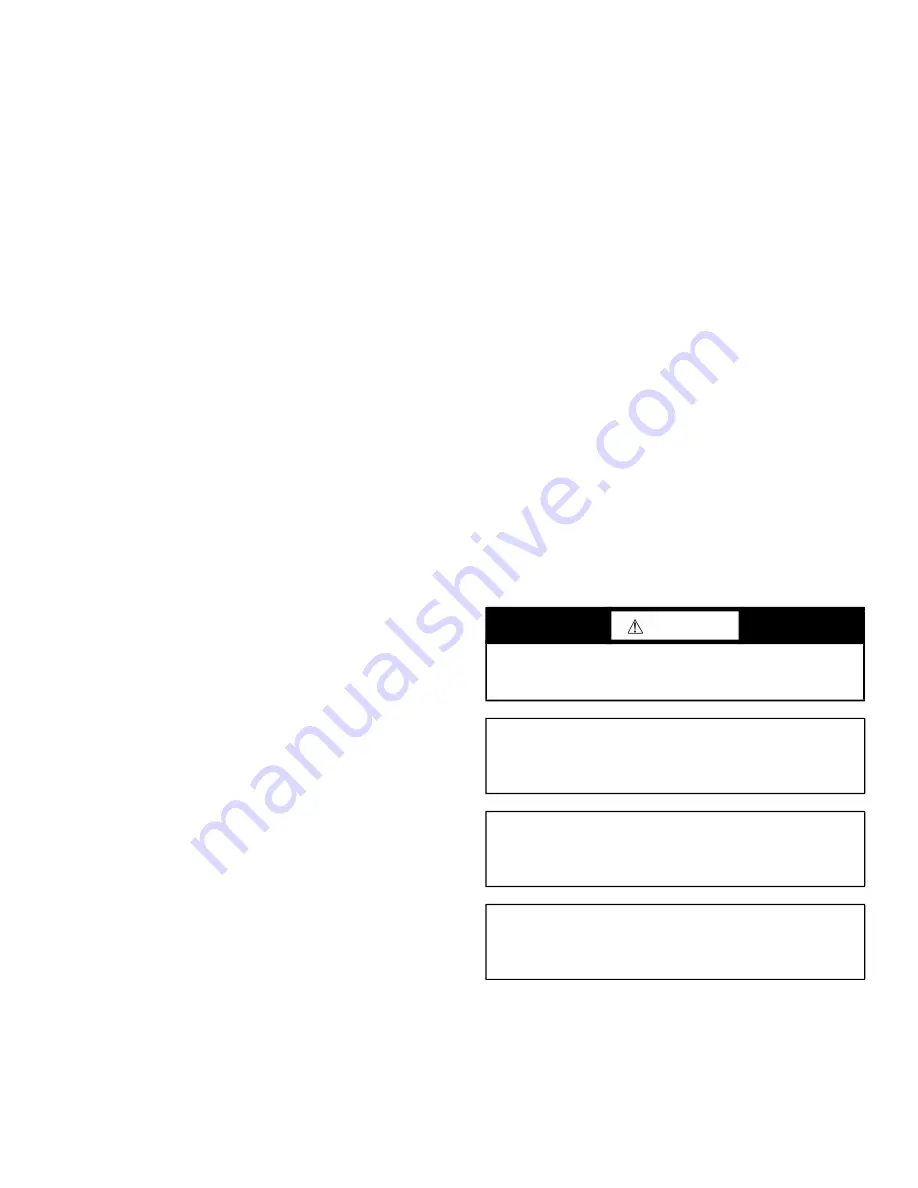
53
CONDENSER WATER TEMPERATURE MONITORING /
CONTROL / ALARM
The control has 4 configurable alarm limits for condenser water
temperature. The control will verify that the water temperature is
within operating range (between high and low limits) for the spe
-
cific operating mode (heating or cooling) before energizing the
compressor. Once the compressor is started, the condenser water
temperature is further monitored to verify that it is within limits to
insure sufficient water is flowing through the coil. Should the
leaving water temperature rise above or fall below the appropriate
limits, and alarm is generated and the compressors will be shut
down if the condition occurs for more than 15 seconds.
HIGH CONDENSATE / OVERFLOW ALARM
The control will monitor a discrete input to determine the state of
a condensate level switch. The input can be configured to alarm
on either an open or closed switch condition. Should this input
be in an alarm state, the control will start a timer and after the
timer exceeds a configurable 'Condensate Overflow Alarm De
-
lay' limit (10 seconds default), the control will generate an alarm
and the unit will disable the compressor, dehumidification and
fan outputs.
FILTER STATUS ALARM
The control provides the ability to generate a dirty filter alarm af
-
ter the number of fan run hours exceeds a configurable filter alarm
timer limit. The control monitors the fan output and if the fan is
operating at any speed, it accumulates run time. Should the fan run
time hours exceed the configurable limit, an alarm is generated. To
reset the alarm timer after the alarm has been generated, a 'Reset
Filter Alarm' input is provided. The filter alarm can be disabled by
setting the 'Filter Alarm Timer Delay' to zero (factory default).
COMPRESSOR FAULT/LOCKOUT ALARM
The control will monitor a discrete input to determine the com
-
pressor state. Should the input state not match the desired com
-
pressor operating state for greater than 6 minutes, the control as
-
sumes the compressor has been locked-out and will generate an
alarm. Also, when this fault occurs and if the unit is equipped with
an auxiliary heating coil or a water economizer and the water tem
-
perature is suitable for heating, should heating be required, the
control will utilize the auxiliary heating source as the primary
heating source until the fault condition is corrected.
INSUFFICIENT VENTILATION ALARM
The control provides the ability to generate a high CO
2
level alarm
during occupied periods whenever the CO
2
sensor value exceeds
the user adjustable limit. Whenever an occupancy transition from
unoccupied to occupied occurs, or the occupied alarm limit is
changed to a value that causes an alarm condition to occur, the
control will automatically calculate an alarm delay based on the
error from set point (15 minutes minimum). This prevents nui
-
sance alarms from occurring when occupancy changes. The IAQ
alarm can be disabled by setting 'Occupied High IAQ Alarm Lim
-
it' to zero.
RELATIVE HUMIDITY ALARM
The control provides the ability to generate an alarm whenever the
space relative humidity exceeds the alarm set point. A separate oc
-
cupied and unoccupied alarm set point is provided. The control
provides a 5 minute alarm delay during unoccupied periods.
During occupied periods, the controller uses the occupied high RH
alarm limit Whenever an occupancy transition from unoccupied to
occupied occurs or the occupied high alarm limit is lowered caus
-
ing an alarm condition to occur, the control will automatically cal
-
culate an alarm delay (equivalent to the configured delay time in
minutes / % RH times the humidity error condition that occurred).
This will prevent nuisance alarms whenever an occupancy change
occurs and allows time for the unit to correct an alarming humidity
condition.
TIME SCHEDULES
The control has an onboard time clock and configurable time
schedules to provide occupancy scheduling.
HOLIDAY SCHEDULES
The control has holiday schedules that can be programmed to
override the normal occupancy operation and cause the unit to go
unoccupied for the duration of the schedule. Each schedule con
-
sists of a start date and time and an end date and time so each
schedule can span more than a single day duration.
OVERRIDE SCHEDULES
The control has override schedules that can be programmed to
override the normal occupancy and holiday operation and cause
the unit to go occupied for the duration of the schedule. Each
schedule consists of a start date and time and an end date and time
so each schedule can span more than a single day duration.
SERVICE
Perform the procedures outlined below periodically, as indicated.
An annual “checkup” is recommended by a licensed refrigeration
mechanic. Recording the performance measurements of volts,
amps, and water temperature differences (both heating and cool
-
ing) is recommended. This data should be compared to the infor
-
mation on the unit’s data plate and the data taken at the original
startup of the equipment.
Periodic lockouts almost always are caused by air or water flow
problems. The lockout (shutdown) of the unit is a normal protec
-
tive measure in the design of the equipment. If continual lock
-
outs occur, call a mechanic immediately and have them check
for: water flow problems, water temperature problems, air flow
problems or air temperature problems. Use of the pressure and
temperature charts for the unit may be required to properly deter
-
mine the cause.
Filters
Filter changes or cleanings are required at regular intervals. The
time period between filter changes will depend upon the type of
environment the equipment is used in. In a single family home that
is not under construction, changing or cleaning the filter every 60
days may be sufficient. In other applications such as motels, where
daily vacuuming produces a large amount of lint, filter changes
may need to be as frequent as biweekly. See Fig. 1 and 2 for re
-
placement filter sizes.
WARNING
To prevent injury or death due to electrical shock or contact
with moving parts, open unit disconnect switch before
servicing unit.
IMPORTANT: When a compressor is removed from this unit,
system refrigerant circuit oil will remain in the compressor. To
avoid leakage of compressor oil, the refrigerant lines of the
compressor must be sealed after it is removed.
IMPORTANT: All refrigerant discharged from this unit must be
recovered without exception. Technicians must follow industry
accepted guidelines and all local, state and federal statutes for the
recovery and disposal of refrigerants.
IMPORTANT: To avoid the release of refrigerant into the
atmosphere, the refrigerant circuit of this unit must only be
serviced by technicians who meet local, state and federal
proficiency requirements.
Summary of Contents for AQUAZONE 50PSH
Page 17: ...17 Fig 15 PSC Motor Single Phase Single Stage WSHP Open Control ...
Page 20: ...20 Fig 18 Constant Torque Motor Single Phase Single Stage WSHP Open Control ...
Page 23: ...23 Fig 21 Constant Airflow Single Phase WSHP Open ...
Page 26: ...26 Fig 24 PSC Motor Three Phase Single Stage WSHP Open ...
Page 29: ...29 Fig 27 Constant Torque Motor Three Phase Single Stage WSHP Open ...
Page 32: ...32 Fig 30 Constant Airflow Motor Three Phase Single Stage WSHP Open ...