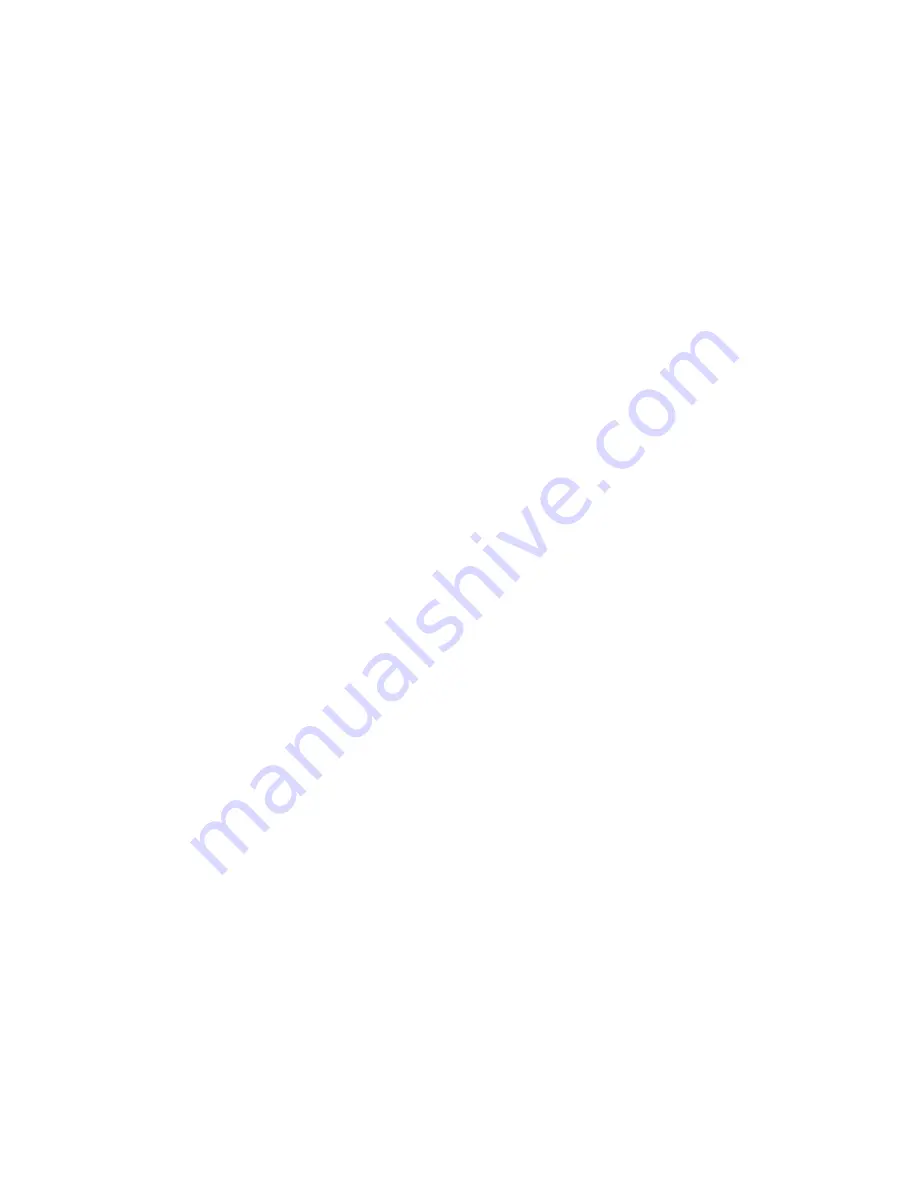
47
Freeze Sensor
The default setting for the freeze limit trip is 30°F (sensor number
1); however this can be changed to 15°F by cutting the R30 resis-
tor located on top of the DIP switch SW1. Since freeze sensor 2 is
dedicated to monitor the evaporator coil it is recommended to
leave the factory default setting on the board. The UPM board will
constantly monitor the refrigerant temperature with the sensor
mounted close to the condensing water coil between the thermal
expansion valve and water coil. If temperature drops below or re-
mains at the freeze limit trip for 30 seconds, the controller will
shut the compressor down and enter into a soft lockout condition.
Both the status LED and the Alarm contact will be active. The
LED will flash three times the code associated with this alarm
condition. If this alarm occurs 2 times (or 4 if DIP switch is set to
4) within an hour the UPM board will enter into a hard lockout
condition. It will constantly monitor the refrigerant temperature
with the sensor mounted close to the evaporator between the ther-
mal expansion valve and evaporator coil as shown in Fig. 29. If
temperature drops below or remains at the freeze limit trip for 30
seconds, the controller will shut the compressor down and enter
into a soft lockout condition. Both the status LED and the Alarm
contact will be active. The LED will flash three times the code as-
sociated with this alarm condition. If this alarm occurs 2 times (or
4 if DIP switch is set to 4) within an hour the controller will enter
into a hard lockout condition.
Intelligent Reset
If a fault condition is initiated, the 5 minute delay on break time
period is initiated and the unit will restart after these delays expire.
During this period the fault LED will indicate the cause of the
fault. If the fault condition still exists or occurs 2 or 4 times (de-
pending on 2 or 4 setting for LOCKOUT DIP switch) before 60
minutes, the unit will go into a hard lockout and requires a manual
lockout reset. A single condensate overflow fault will cause the
unit to go into a hard lockout immediately, and will require a man-
ual lockout reset.
Lockout Reset
A hard lockout can be reset by turning the unit thermostat off and
then back on when the RESET DIP switch is set to "Y" or by shut-
ting off unit power at the circuit breaker when the RESET DIP
switch is set to "R".
Selectable Alarm Mode
The UPM board can be configured to have either a constant or
pulse signal. If constant (CONT) is selected the UPM will provide
a closed contact at the alarm output until the alarm is cleared. If
pulsed (PULSE) is selected the UPM will sequence the alarm con-
tact with the fault LED flashes.
Test Mode (TEST)
In test mode the ASC and Random Start time delays are reduced
(5 seconds and 10 seconds respectively), and serve no function to
the end user equipment. The alarm and display relays also pulse
for both soft and hard lockout conditions, and are both cleared
through a manual reset.
UPM Sequence of Operations
Figure 24 shows the UPM sequence of operations.
Thermistor
A thermistor may be required for single-phase units where starting
the unit is a problem due to low voltage.
Control Sensors
The control system employs 2 nominal 10,000 ohm thermistors
(FP1 and FP2) that are used for freeze protection. Be sure FP1 is
located in the discharge fluid and FP2 is located in the air dis-
charge. See Fig. 31.
Thermostatic Expansion Valves
Thermostatic expansion valves (TXV) are used as a means of me-
tering the refrigerant through the evaporator to achieve a preset su-
perheat at the TXV sensing bulb. Correct superheat of the refriger-
ant is important for the most efficient operation of the unit and for
the life of the compressor.
Packaged heat pumps typically use one bi-flow TXV to meter re-
frigerant in both modes of operation. When diagnosing possible
TXV problems it may be helpful to reverse the refrigerant flow to
assist with the diagnosis.
Geothermal and water source heat pumps are designed to operate
through a wide range of entering-water temperatures that will
have a direct effect on the unit refrigerant operating pressures.
Therefore, diagnosing TXV problems can be difficult.
TXV FAILURE
The most common failure mode of a TXV is when the valve fails
while closed. Typically, a TXV uses spring pressure to close the
valve and an opposing pressure, usually from a diaphragm, to
open the valve. The amount of pressure exerted by the diaphragm
will vary, depending on the pressure inside of the sensing bulb. As
the temperature of and pressure within the bulb decreases, the
valve will modulate closed and restrict the refrigerant flow
through the valve. The result is less refrigerant in the evaporator
and an increase in the superheat. As the temperature at the bulb in-
creases the diaphragm pressure will increase, which opens the
valve and allows more refrigerant flow and a reduction in the su-
perheat.
If the sensing bulb, connecting capillary, or diaphragm assembly
are damaged, pressure is lost and the spring will force the valve to
a closed position. Often, the TXV will not close completely so
some refrigerant flow will remain, even if there is inadequate flow
for the heat pump to operate.
The TXV sensing bulb must be properly located, secured, and in-
sulated as it will attempt to control the temperature of the line to
which it is connected. The sensing bulb must be located on a dedi-
cated suction line close to the compressor. On a packaged heat
pump, the bulb may be located almost any place on the tube run-
ning from the compressor suction inlet to the reversing valve. If
the bulb is located on a horizontal section, it should be placed in
the 10:00 or 2:00 position for optimal performance.