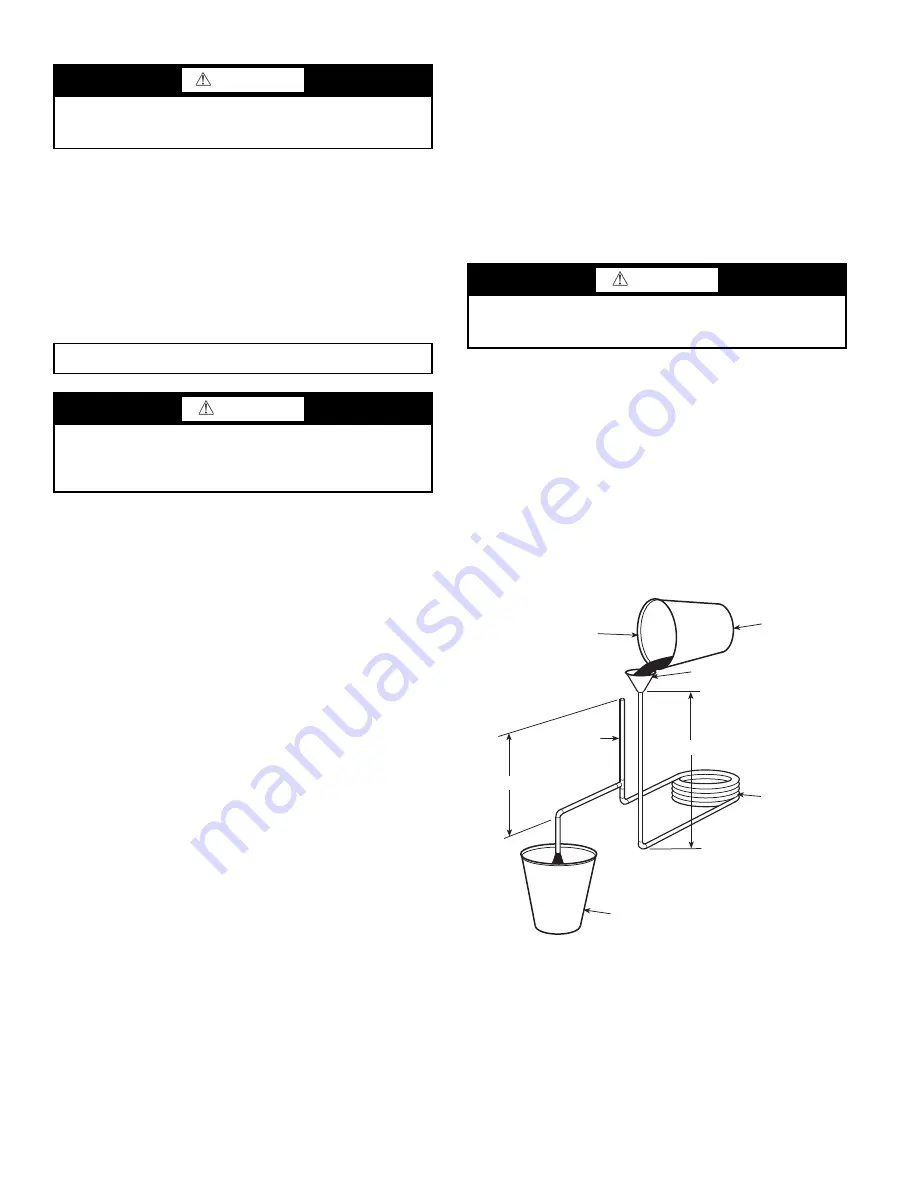
44
Filters
Filter changes or cleanings are required at regular intervals. The
time period between filter changes will depend upon type of envi-
ronment the equipment is used in. In a single family home, that is
not under construction, changing or cleaning the filter every 60
days may be sufficient. In other applications such as motels, where
daily vacuuming produces a large amount of lint, filter changes
may be need to be as frequent as biweekly. See Fig. 1 and 2 for re-
placement filter sizes. Note that horizontal units containing two
filters are taped together at the factory to facilitate removal. This
should be done by end user as new filters are installed.
Condensate Drain Pans
The condensate drain should be checked quarterly by cleaning and
flushing to ensure proper drainage.
Refrigerant System
Verify air and water flow rates are at proper levels before servic-
ing. To maintain sealed circuitry integrity, do not install service
gages unless unit operation appears abnormal. Check to see that
unit is within the superheat and subcooling temperature ranges
shown in Tables 16-28. If the unit is not within these ranges, re-
cover and reweigh in refrigerant charge.
Compressor
Conduct annual amperage checks to ensure that amp draw is no
more than 10% greater than indicated on the serial plate data.
Fan Motors
All units have lubricated fan motors. Fan motors should never be
lubricated unless obvious, dry operation is suspected. Periodic
maintenance oiling is NOT recommended as it will result in dirt
accumulating in the excess oil and cause eventual motor failure.
Conduct annual dry operation check and amperage check to en-
sure amp draw is no more than 10% greater than indicated on se-
rial plate data and to remove any build up on the blower assem-
bly.
Condensate Drain Cleaning
Clean the drain line and unit drain pan at the start of each cooling
season. Check flow by pouring water into drain. Be sure trap is
filled to maintain an air seal.
Air Coil Cleaning
Remove dirt and debris from evaporator coil as required by condi-
tion of the coil. A 10% solution of dishwasher detergent and water
is recommended for cleaning both sides of the coil, followed by a
thorough water rinse. Clean coil with a stiff brush, vacuum clean-
er, or compressed air. Use a fin comb of the correct tooth spacing
when straightening mashed or bent coil fins.
Condenser Cleaning
Water-cooled condensers may require cleaning of scale (water de-
posits) due to improperly maintained closed-loop water systems.
Sludge build-up may need to be cleaned in an open water tower
system due to induced contaminants.
Local water conditions may cause excessive fouling or pitting of
tubes. Condenser tubes should therefore be cleaned at least once a
year, or more often if the water is contaminated.
Proper water treatment can minimize tube fouling and pitting. If
such conditions are anticipated, water treatment analysis is recom-
mended. Refer to the Carrier System Design Manual, Part 5, for
general water conditioning information.
Clean condensers with an inhibited hydrochloric acid solution.
The acid can stain hands and clothing, damage concrete, and,
without inhibitor, damage steel. Cover surroundings to guard
against splashing. Vapors from vent pipe are not harmful, but take
care to prevent liquid from being carried over by the gases.
Warm solution acts faster, but cold solution is just as effective if
applied for a longer period.
GRAVITY FLOW METHOD
Do not add solution faster than vent can exhaust the generated
gases.
When condenser is full, allow solution to remain overnight, then
drain condenser and flush with clean water. Follow acid manufac-
turer’s instructions. See Fig. 26.
Fig. 26 — Gravity Flow Method
FORCED CIRCULATION METHOD
Fully open vent pipe when filling condenser. The vent may be
closed when condenser is full and pump is operating. See Fig. 27.
Regulate flow to condenser with a supply line valve. If pump is a
non-overloading type, the valve may be fully closed while pump
is running.
WARNING
To prevent injury or death due to electrical shock or contact
with moving parts, open unit disconnect switch before servic-
ing unit.
IMPORTANT: Units should never be operated without a filter.
CAUTION
Equipment should never be used during construction or reno-
vation due to possibility of contaminants entering the air coil
of the equipment which permanently affects the performance
and may shorten the life of the equipment.
CAUTION
Follow all safety codes. Wear safety glasses and rubber gloves
when using inhibited hydrochloric acid solution. Observe and
follow acid manufacturer’s instructions.
FILL CONDENSER WITH
CLEANING SOLUTION. DO
NOT ADD SOLUTION
MORE RAPIDLY THAN
VENT CAN EXHAUST
GASES CAUSED BY
CHEMICAL ACTION.
PAIL
FUNNEL
CONDENSER
PAIL
3’ TO 4’
VENT
PIPE
5’ APPROX
1”
PIPE