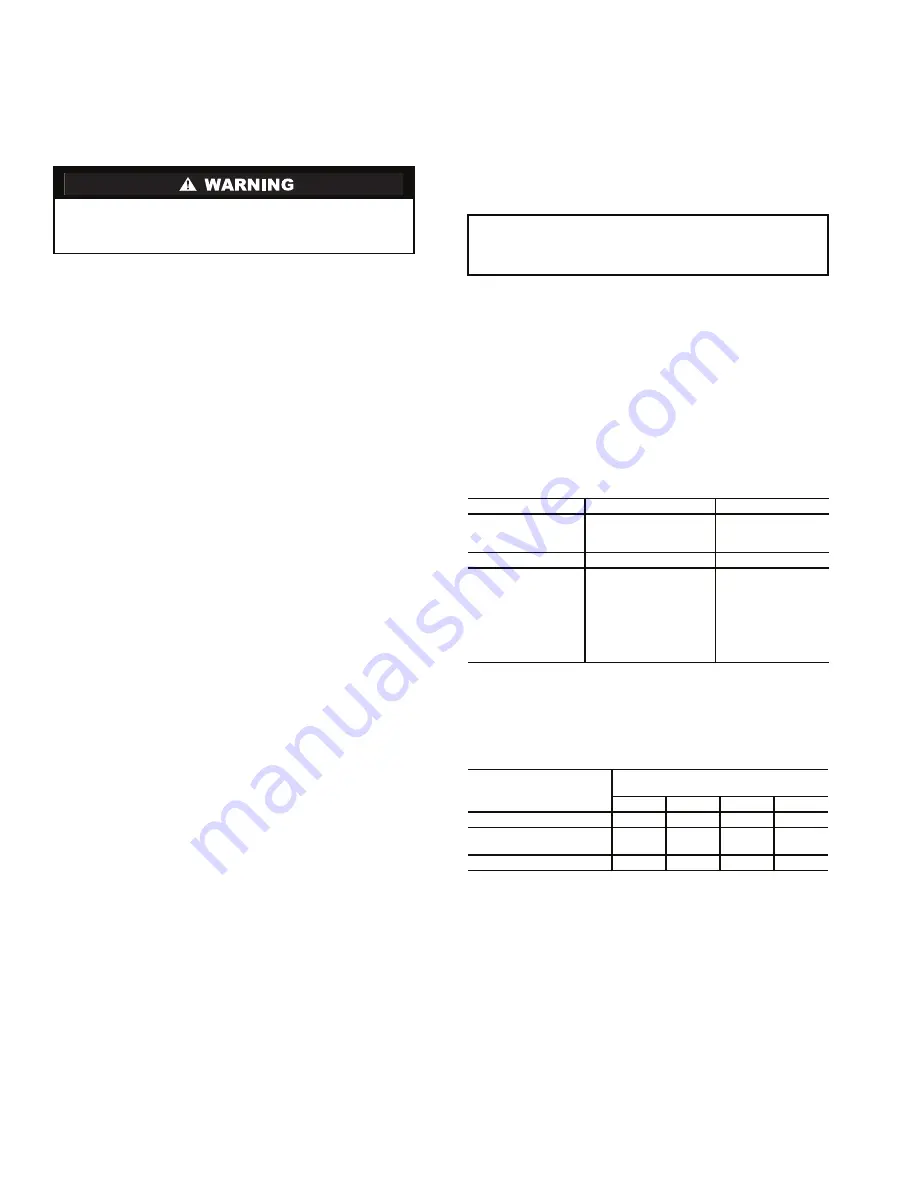
34
An alternative method is to install a flow control device.
These devices are typically an orifice of plastic material de-
signed to allow a specified flow rate that are mounted on the
outlet of the water control valve. Occasionally these valves
produce a velocity noise that can be reduced by applying
some back pressure. To accomplish this, slightly close the
leaving isolation valve of the well water setup.
Flushing —
Once the piping is complete, final purging
and loop charging is needed. A flush cart pump of at least
1.5 hp is needed to achieve adequate flow velocity in the
loop to purge air and dirt particles from the loop. Flush the
loop in both directions with a high volume of water at a high
velocity. Follow the steps below to properly flush the loop:
1. Verify power is off.
2. Fill loop with water from hose through flush cart be-
fore using flush cart pump to ensure an even fill. Do
not allow the water level in the flush cart tank to drop
below the pump inlet line to prevent air from filling
the line.
3. Maintain a fluid level in the tank above the return tee
to avoid air entering back into the fluid.
4. Shutting off the return valve that connects into the
flush cart reservoir will allow 50 psi surges to help
purge air pockets. This maintains the pump at 50 psi.
5. To purge, keep the pump at 50 psi until maximum
pumping pressure is reached.
6. Open the return valve to send a pressure surge through
the loop to purge any air pockets in the piping system.
7. A noticeable drop in fluid level will be seen in the
flush cart tank. This is the only indication of air in the
loop.
NOTE: If air is purged from the system while using a 10 in.
PVC flush tank, only a 1 to 2 in. level drop will be noticed
since liquids are incompressible. If the level drops more
than this, flushing should continue since air is still being
compressed in the loop. If level is less than 1 to 2 in.,
reverse the flow.
8. Repeat this procedure until all air is purged.
9. Restore power.
Antifreeze may be added before, during or after the
flushing process. However, depending on when it is added
in the process, it can be wasted. Refer to the Antifreeze sec-
tion for more detail.
Loop static pressure will fluctuate with the seasons. Pres-
sures will be higher in the winter months than during the
warmer months. This fluctuation is normal and should be
considered when charging the system initially. Run the unit
in either heating or cooling for several minutes to condition
the loop to a homogenous temperature.
When complete, perform a final flush and pressurize the
loop to a static pressure of 40 to 50 psi for winter months or
15 to 20 psi for summer months.
After pressurization, be sure to remove the plug from the
end of the loop pump motor(s) to allow trapped air to be
discharged and to ensure the motor housing has been flood-
ed. Be sure the loop flow center provides adequate flow
through the unit by checking pressure drop across the heat
exchanger.
Antifreeze —
In areas where entering loop temperatures
drop below 40 F or where piping will be routed through ar-
eas subject to freezing, antifreeze is needed.
Alcohols and glycols are commonly used as antifreeze
agents. Freeze protection should be maintained to 15 F
below the lowest expected entering loop temperature. For
example, if the lowest expected entering loop temperature is
30 F, the leaving loop temperature would be 22 to 25 F.
Therefore, the freeze protection should be at 15 F (30 F –
15 F = 15 F).
Calculate the total volume of fluid in the piping system.
See Table 22. Use the percentage by volume in Table 23 to
determine the amount of antifreeze to use. Antifreeze con-
centration should be checked from a well mixed sample us-
ing a hydrometer to measure specific gravity.
FREEZE PROTECTION SELECTIONThe 30 F FP1 fac-
tory setting (water) should be used to avoid freeze damage
to the unit.
Once antifreeze is selected, the JW3 jumper (FP1)
should be clipped on the control to select the low tempera-
ture (antifreeze 13 F) set point to avoid nuisance faults.
Table 22 — Approximate Fluid Volume (gal.)
per 100 Ft of Pipe
LEGEND
NOTE: Volume of heat exchanger is approximately 1.0 gallon.
Table 23 — Antifreeze Percentages by Volume
Cooling Tower/Boiler Systems —
These systems
typically use a common loop maintained at 60 to 90 F. The
use of a closed circuit evaporative cooling tower with a
secondary heat exchanger between the tower and the water
loop is recommended. If an open type cooling tower is
used continuously, chemical treatment and filtering will be
necessary.
Ground Coupled, Closed Loop and Plateframe
Heat Exchanger Well Systems —
These systems
allow water temperatures from 30 to 110 F. The external
loop field is divided up into 2 in. polyethylene supply and re-
turn lines. Each line has valves connected in such a way that
upon system start-up, each line can be isolated for flushing
using only the system pumps. Air separation should be locat-
ed in the piping system prior to the fluid re-entering the loop
field.
To avoid possible injury or death due to electrical shock,
open the power supply disconnect switch and secure it in
an open position before flushing system.
IMPORTANT: All alcohols should be pre-mixed and
pumped from a reservoir outside of the building or intro-
duced under water level to prevent alcohols from fuming.
PIPE
DIAMETER (in.)
VOLUME (gal.)
Copper
1
4.1
1.25
6.4
1.5
9.2
Rubber Hose
1
3.9
Polyethylene
3
/
4
IPS SDR11
2.8
1 IPS SDR11
4.5
1
1
/
4
IPS SDR11
8.0
1
/
2
IPS SDR11
10.9
2 IPS SDR11
18.0
1
1
/
4
IPS SCH40
8.3
1
1
/
2
IPS SCH40
10.9
2 IPS SCH40
17.0
IPS
—
Internal Pipe Size
SCH
—
Schedule
SDR
—
Standard Dimensional Ratio
ANTIFREEZE
MINIMUM TEMPERATURE FOR
FREEZE PROTECTION (F)
10
15
20
25
Methanol (%)
25
21
16
10
100% USP Food Grade
Propylene Glycol (%)
38
30
22
15
Ethanol (%)
29
25
20
14