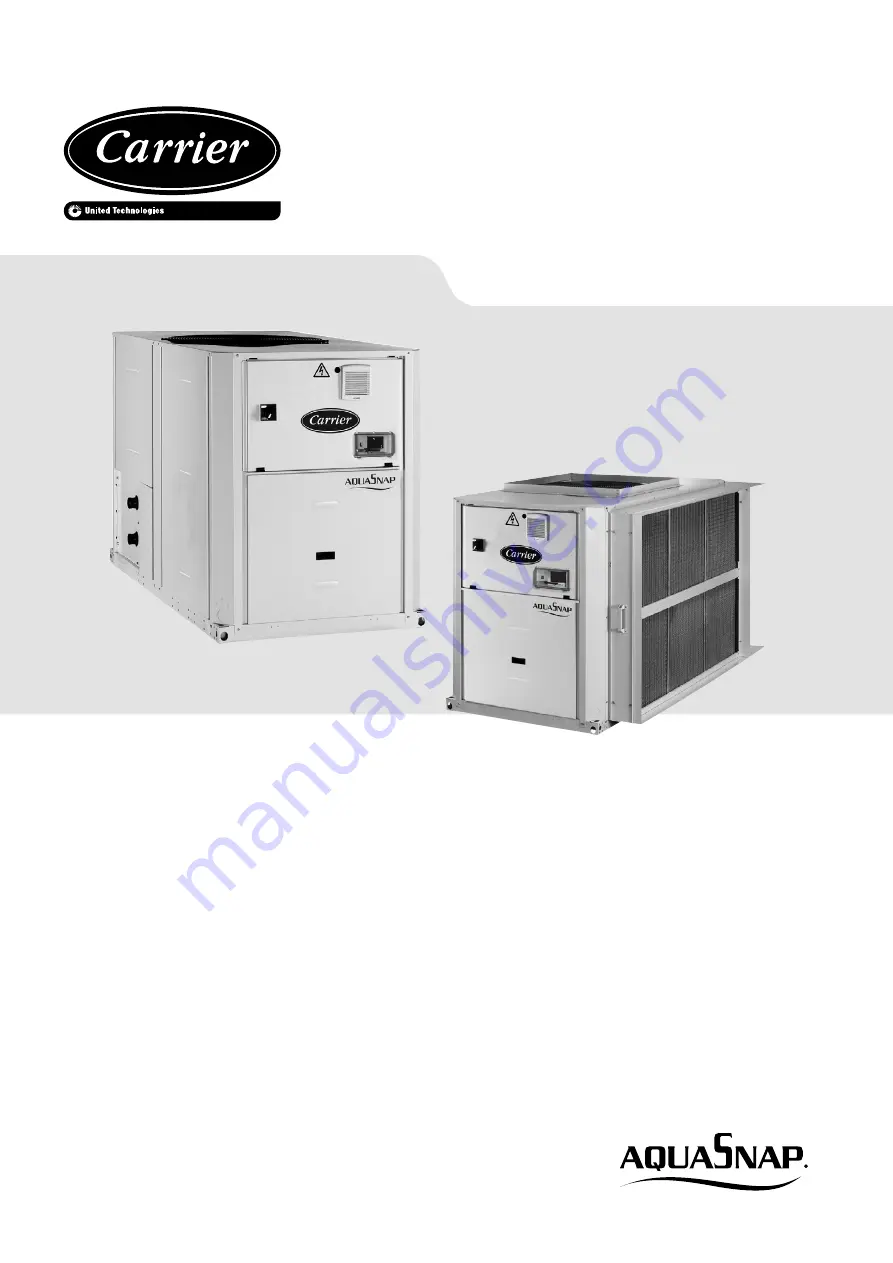
INSTALLATION, OPERATION AND
M A I N T E N A N C E I N S T R U C T I O N S
Original document
Reversible Air-to-Water Heat Pumps
30RQS/30RQSY 039-160 “B”
For the operation of the control please refer to the
Touch Pilot Junior Control manual for the 30RBS/RQS 039-160 series
Nominal cooling capacity 30RQS 38-148 kW - 50 Hz
Nominal heating capacity 30RQS 42-150 kW - 50Hz
Nominal cooling capacity 30RQSY 37-146 kW - 50 Hz
Nominal heating capacity 30RQSY 42-151 kW - 50Hz
30RQS
30RQSY
Touch Pilot Junior