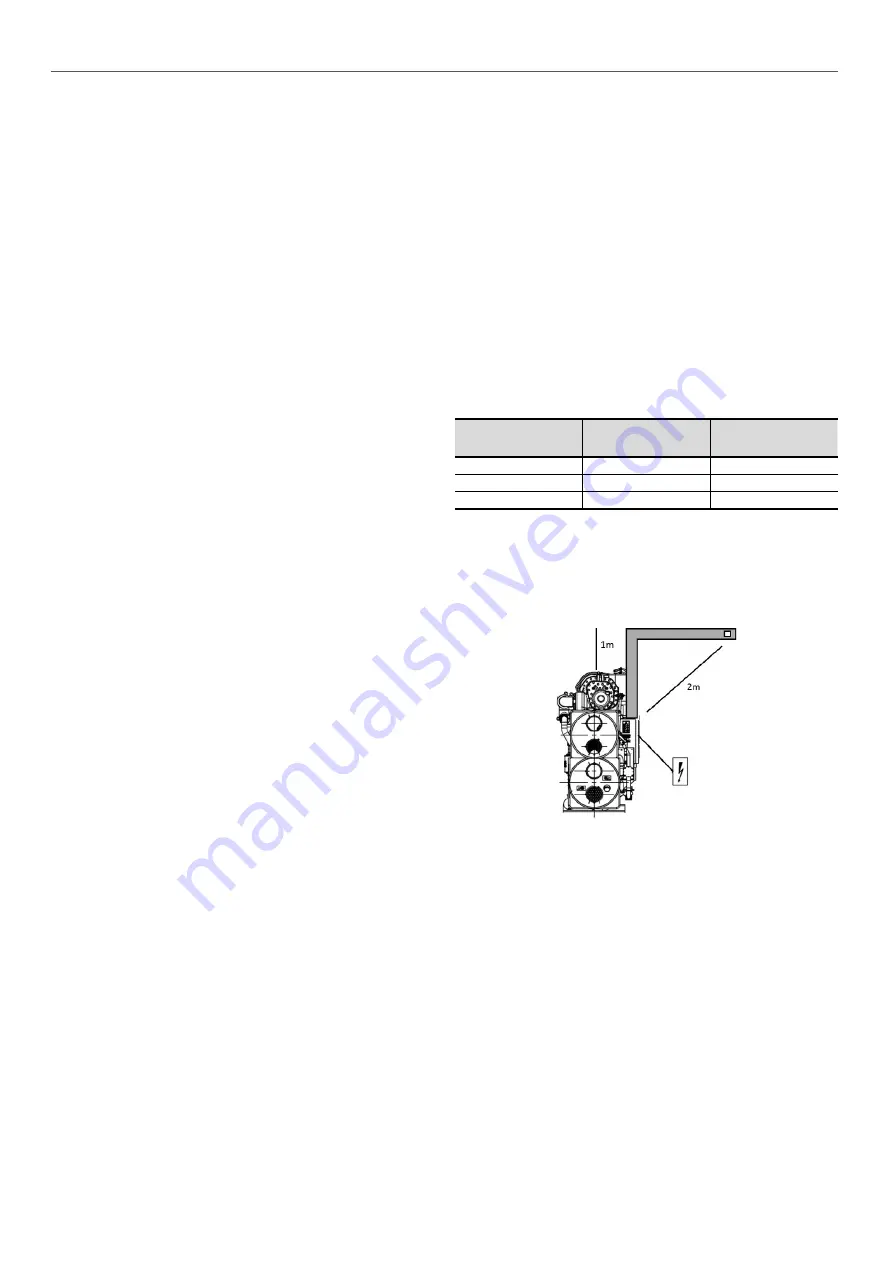
6
All factory-installed relief valves are lead-sealed to prevent cany
calibration change. The external relief valves must always be
vented to outside if the units are installed in a closed space. Refer
to the installation regulations, for example those of European
standard EN 378 and EN 13136. These pipes must be installed
in a way that ensures that people and property are not exposed
to vented refrigerant. As the fluids can be diffused in the air, ensure
that refrigerant is discharged away from building air intakes, relief
valves must be checked periodically. The valves must be checked
periodically.
The safety device shall be tested at least once a year to verify
good operation and cut out value.
An example of test procedure
without removing the pressure
switch
is given in Section 11.9 of this manual
.
If the relief valves are installed on a change-over manifold, this is
equipped with a relief valve on each of the two outlets. Only one
of the two relief valves is in operation, the other one is isolated.
Never leave the change-over valve in the intermediate position,
i.e. with both ways open (locate the control element in the stop
position). If a relief valve is removed for checking or replacement
please ensure that there is always an active relief valve on each
of the change-over valves installed in the unit.
All factory-installed relief valves are lead-sealed to prevent any
calibration change.
The external relief valves are designed and installed to ensure
damage limitation in case of a fire.
In accordance with the regulations applied for the design, the
European directive on equipment under pressure and in
accordance with the national usage regulations:
• These relief valves (and rupture disk if used) are not safety
accessories but damage limitation accessories in case of
a fire.
• The high pressure switches are the safety accessories.
The relief valve must only be removed if the fire risk is fully
controlled and after checking that this is allowed by local
regulations and authorities. This is the responsibility of the
operator.
When the unit is subjected to fire, safety devices prevent rupture
due to over-pressure by releasing refrigerant. The fluid may then be
decomposed into toxic residues when subjected to the flame:
• Stay away from the unit
• Set up warnings and recommendations for personnel in
charge to stop the fire.
• Fire extinguishers appropriate to the system and the
refrigerant type must be easily accessible.
The external relief valves must be connected to discharge pipes for
units installed in a room. Refer to the installation regulations, for example
those of European standards EN-378.
These standards include a sizing method and examples for
configuration and calculation. Under certain conditions they permit
connection of several valves to the same discharge pipe.
Carrier recommends using flexible hose to connect the relief valves
to discharge pipe. Special care shall be taken so that coupling to
discharge pipe is not creating mechanical stress on relief valve
connection.
These pipes must be installed in a way that ensures that people and
property are not exposed to refrigerant leaks. These fluids may be
diffused in the air, but far away from any building air intake, or they
must be discharged in a quantity that is appropriate for a suitably
absorbing environment (Note that the R1234ze(E) refrigerant is
heavier than air).
It is recommended to install an indicating device to show if part of
the refrigerant has leaked from the valve. The presence of oil at the
outlet orifice is a useful indicator that refrigerant has leaked. Keep
this orifice clean to ensure that any leaks are obvious.
The calibration of a valve that has leaked is generally lower than
its original calibration. The new calibration may affect the operating
range. To avoid a nuisance tripping or leaks, replace or re-calibrate
the valve.
Periodic check of the relief valves: See paragraph 1.3 “Maintenance
safety considerations”.
The electrical box must be supplied with fresh air source.
This must be done by connecting the interface on the top of the
electrical box with an air duct. The fresh air should be sucked from
outside the machinery room in an open air area. If this is not
possible, it is acceptable to suck fresh air inside the machinery
room but the following criteria must be respected regarding the
ventilation duct inlet:
• located at least one meter higher than the highest point of
the unit
• located at least 2 meters away from the unit
• The inlet air duct must be sized according to table below
(Maximum air duct pressure drop for a given air flow)
In addition, the following constraints must be fulfilled:
•
The junction between the air duct and the electrical box
interface must be tight
• The inlet air duct must be sized to guarantee below
maximum pressure drop in any operating condition
(including fooling)
61XWH model
Air flow (m
3
/h)
Air duct maximum
pressure drop (Pa)
3
40
10
5 / 7
60
20
10 / 14 / 15 / 17
120
40
•
The electrical box fan filter if any has to be serviceable in
order to be checked, cleaned and replaced if necessary.
•
The inlet of the duct should be equipped with a dust filter.
It’s filtering classification shall depend on dust occurrence.
G3 class per EN 779 is recommended.
Provide a drain in the discharge circuit, close to each relief valve,
to avoid an accumulation of condensate or rain water.
1 - INTRODUCTION