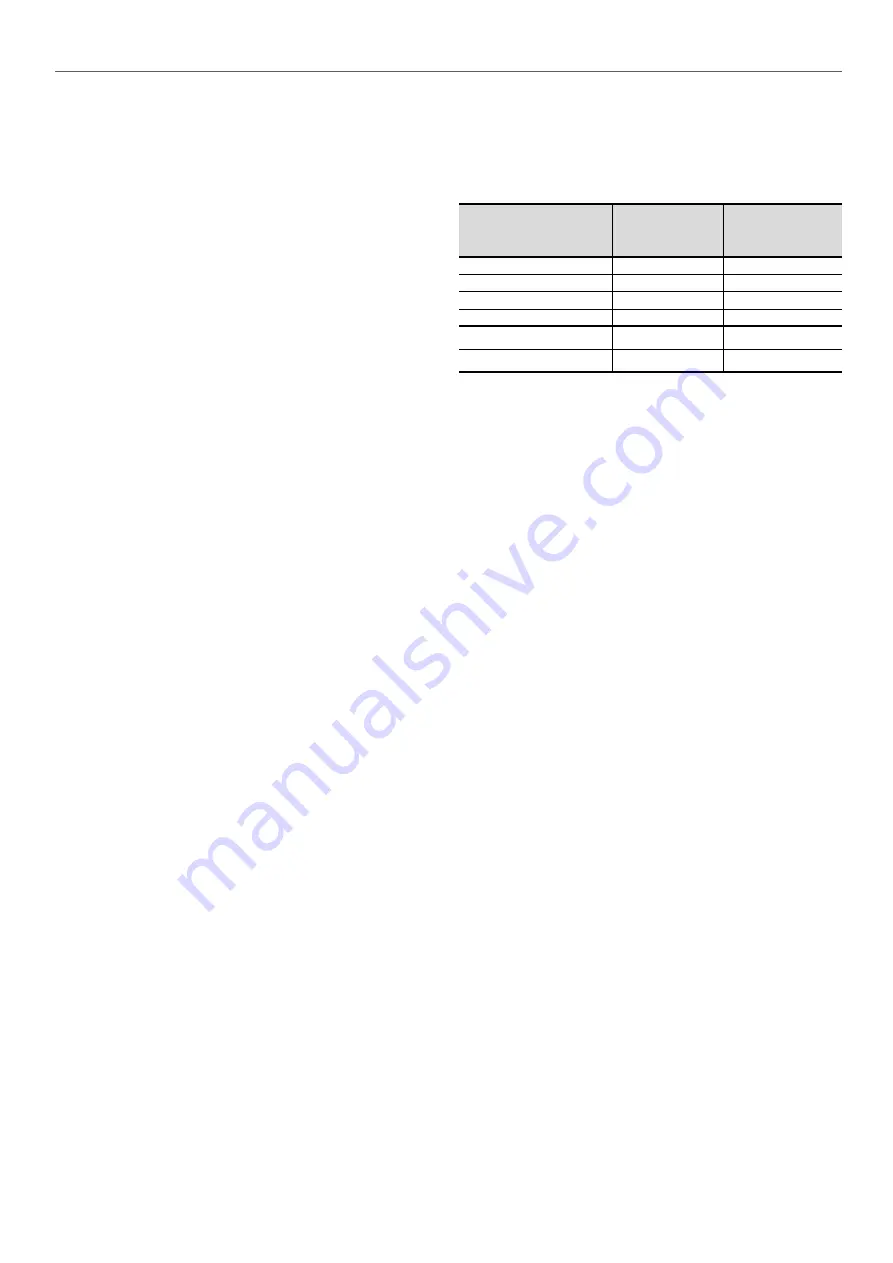
1 - INTRODUCTION
30XW-V/30XWHV units are designed to cool or heat water for the
air conditioning and heating of buildings and industrial procsses.
Prior to the initial start-up of the 30XW-V/30XWHV units, the people
involved in the on-site installation, start-up, operation, and
maintenance of this unit should be thoroughly familiar with these
instructions and the specific project data for the installation site.
30XW-V/30XWHV units are designed for a very high level of safety
during installation, start-up, operation and maintenance.
They are designed for an operating life of 15 years by assuming a
75% utilisation factor; that is approximately 100,000 operating hours.
They will provide safe and long-lasting service when operated within
their application range.
This manual provides the necessary information to fami-liarize
yourself with the control system before performing start-up
procedures. The procedures in this manual are arranged in the
sequence required for machine installation, start-up, operation
and maintenance.
Always ensure that all required safety measures are followed,
including those in this document, such as: wearing protec-tive
clothing (gloves, ear defenders, safety glasses and shoes) using
appropriate tools, employing qualified and skilled technicians
(electricians, refrigeration engineers) and following local
regulations.
To find out, if these products comply with European directives
(machine safety, low voltage, electromagnetic compatibility,
equipment under pressure etc.) check the declarations of
conformity for these products.
1.1 - Installation safety considerations
Access to the unit must be reserved to authorised personnel,
qualified and trained in monitoring and maintenance. The access
limitation device must be installed by the customer (e.g. cut-off,
enclosure).
After the unit has been received and is ready to be installed or
reinstalled and before it is started up, it must be inspected for
damage. Check that the refrigerant circuit(s) is (are) intact,
especially that no components or pipes have shifted (e.g. following
a shock). If in doubt, carry out a leak tightness check and verify with
the manufacturer that the circuit integrity has not been impaired. If
damage is detected upon receipt, immediately file a claim with the
shipping company.
Carrier strongly recommends employing a specialised
company to unload the machine.
It is compulsory to wear personal protection equipment.
Do not remove the skid or the packaging until the unit is in
its final position. These units can be moved with a fork lift
truck, as long as the forks are positioned in the right place
and direction on the unit.
The units can also be lifted with slings, using only the
designated lifting points marked on the unit.
Use slings or lifting beams with the correct capacity, and
always follow the lifting instructions on the certified drawings
supplied with the unit. Do not tilt the unit more than 15°.
Safety is only guaranteed, if these instructions are carefully
followed. If this is not the case, there is a risk of material
deterioration and injuries to personnel.
Never cover any protection devices.
This applies to the relief valves (if used) in the refrigerant or
heat transfer medium circuits, the fuse plugs and the pressure
switches.
Ensure that the valves are correctly installed, before operating
the unit.
Classification and control
In accordance with the Pressure Equipment Directive and
national usage monitoring regulations in the European Union
the protection devices for these machines are classified as
follows:
Classification of safety devices
Safety device
(1)
Device for damage
limitation in
the event of an
external fire
(2)
Refrigerant Side
High pressure safety loop
(3)
X
External relief valve
(4)
X
Rupture disk
X
Heat transfert lfuid side
External relief valve
(5)
(5)
(1) Classified for protection in normal service situations.
(2) Classified for protection in abnormal service situations. These devices are sized
for fires with a thermal flow of 10kW/m². No combustible matter should be placed
within 6.5m of the unit.
(3) High pressure safety loop = SRMCR as described in component section of this
manual and in electrical diagram.
(4) The instantaneous over-pressure limitation of 10% of the operating pressure
does not apply to this abnormal service situation. The setting of the device to a
value above the service pressure is allowed and complies with the applicable
standards. In this case either the design temperature or the high pressure safety
loop ensures that the maximum allowable pressure is not exceeded in normal
service situations.
(5) The selection of these relief valves must be made by the personnel responsible
for completing the hydraulic installation.
If the relief valves are installed on a change-over valve, this is
equipped with a relief valve on each of the two outlets. Only
one of the two relief valves is in operation, the other one is
isolated. Never leave the change-over valve in the intermediate
position, i.e. with both ways open (bring the actuator in
abutment, front or back according to the outlet to isolate). If
a relief valve is removed for checking or replacement please
ensure that there is always an active relief valve on each of
the change-over valves installed in the unit.
All factory-installed relief valves are lead-sealed to prevent any
calibration change.
The external relief valves and the fuses are designed and
installed to ensure damage limitation in case of a fire.
In accordance with the regulations applied for the design, the
European directive on equipment under pressure and in
accordance with the national usage regulations:
• These relief valves and fuses are not safety accessories
but damage limitation accessories in case of a fire,
• The high pressure switches are the safety accessories.
The relief valve must only be removed if the fire risk is fully
controlled and after checking that this is allowed by local
regulations and authorities. This is the responsibility of the
operator.
When the unit is subjected to fire, safety devices prevent
rupture due to over-pressure by releasing the refrigerant. The
fluid may then be decomposed into toxic residues when
subjected to the flame:
-
Stay away from the unit.
-
Set up warnings and recommendations for personnel in
charge to stop the fire.
-
Fire extinguishers appropriate to the system and the
refrigerant type must be easily accessible.
The external relief valves must in principle be connected to
discharge pipes for units installed in a room. Refer to the
installation regulations, for example those of European
standards EN 378 and EN 13136.
5