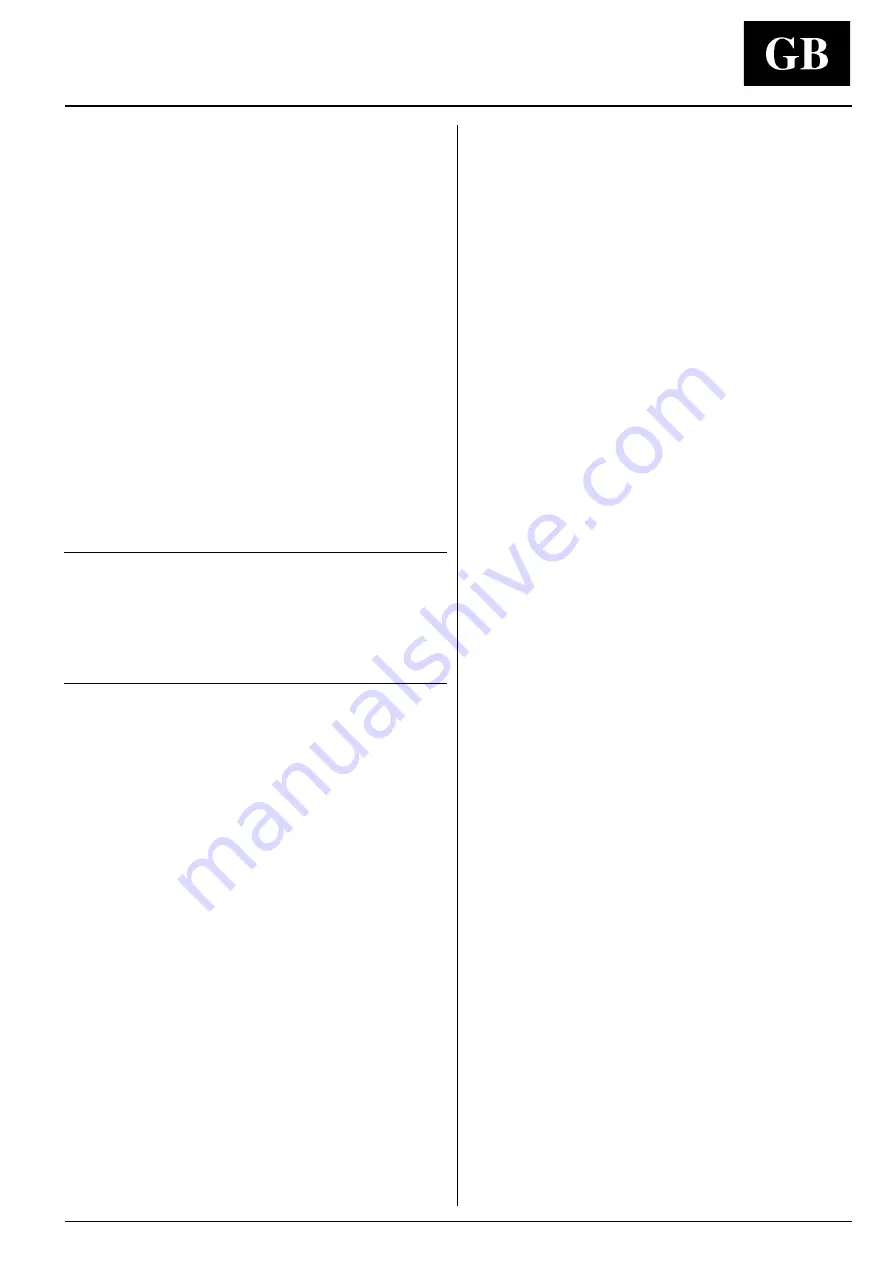
GB - 5
61 AF
E N G L I S H
General information and hydronic module
Unit installation
Read this manual thoroughly before starting machine installation.
The device complies with the low voltage directives, Machinery
Directive and EMC Directive.
•
Check that the impedance of the mains power supply is in
conformance with the unit power input indicated in the electrical
data table II on page 4 (EN 61000-3-11).
• The installation must be carried out by a qualified installer.
• Follow all current national safety code requirements.
In particular ensure that a properly sized and connected ground wire
is in place.
• Check that voltage and frequency of the mains power supply are
those required; the available power must be adequate to operate any
other possible appliances connected to the same line. Also ensure
that national safety code requirements have been followed for the
mains supply circuit.
• After installation thoroughly test the system operation and explain all
system functions to the owner.
• Leave this manual with the owner for consultation during future
periodic maintenance.
• Be sure the unit and its components are checked periodically to look
for loosen, damaged or broken components
In case of persisting defects, the unit may cause personal injury or
property damage.
IMPORTANT:
During the unit installation make first the hydronic connections and
then electrical connections. If unit is uninstalled first disconnect
electrical cables, then the hydronic connections.
WARNING:
Disconnect the mains power supply switch before servicing the
system or handling any internal parts of the unit.
All mains supply circuits must be disconnected.
• The manufacturer declines any liability for damage resulting from
modifications or errors in the electrical or hydronic connections.
• Failure to observe the installation instructions or use of the unit under
conditions other than those indicated in Tables “Operating limits”, will
immediately void the unit warranty.
• Failure to observe electric safety codes may cause a fire hazard in case
of short circuits.
• Inspect equipment for damage due to improper transportation or
handling: file an immediate claim with the shipping company. Do not
install or use damaged units.
• During unit operation, some of the refrigerant circuit elements could
reach a temperature in excess of 70°C so only trained and qualified
personnel should access areas protected by access panels.
• In case of any malfunctioning turn the unit off, disconnect the mains
power supply and contact a qualified service engineer.
•
All of the manufacturing and packaging materials used for your
new appliance are compatible with the environment and can be
recycled.
• Dispose of the packaging material in accordance with local
requirements.
• This equipment contains refrigerant R-407C that must be disposed of
in a proper manner. When disposing of the unit after its operational
life, remove it carefully. The unit must then be delivered to an
appropriate disposal center or to the original equipment dealer.
• Carefully recover refrigerant within this unit before final disposal or
when servicing. Never vent refrigerant to atmosphere.
Choosing the installation site
• This unit should not be installed in an explosive atmosphere.
• The unit can operate in normal radioelectric atmospheres in
residential, commercial and light industrial installations. For other
applications, please consult Carrier.
• In the case of heat pump operation with an outdoor temperature
of less than 0 °C the unit must be installed at least 300 mm above
ground level. This is necessary to prevent ice from accumulating on
the frame and to permit correct operation also in the event of heavy
snowfalls.
• The unit must be levelled on both axes (the tolerance is less than 2
mm per metre).
• In some cases it may be necessary to fit deflectors against strong
winds and to stop snow from hitting the coil directly.
These deflectors must be installed so that the normal air circulation is
not obstructed.
Siting the unit
Check that:
• The location is able to support unit operating weight (Table I).
• There is sufficient space for servicing and air flow around the unit (see
“Clearances” figure).
• The selected site is without dust or foreign material which could
obstruct the coil.
• When installing the unit on the ground, the selected site is not subject
to flooding.
• The installation is in accordance with local rules and standards
governing the installation of air conditioning equipment.
• Vibration absorbers have been provided throughout the installation
to prevent noise from being transmitted.
• To avoid possible damages fix the vibration absorbers under a feet-
supporting frame of the unit.
Transport
1. Use spreader bars to lift the unit to avoid damage to the panels. Avoid
violent movements.
2. Never roll or swing the unit more than 15°.
IMPORTANT:
Ensure that all unit panels are fixed in place before moving the unit.
Raise and set down the unit carefully.
IMPORTANT:
Always ensure that the unit is levelled correctly.