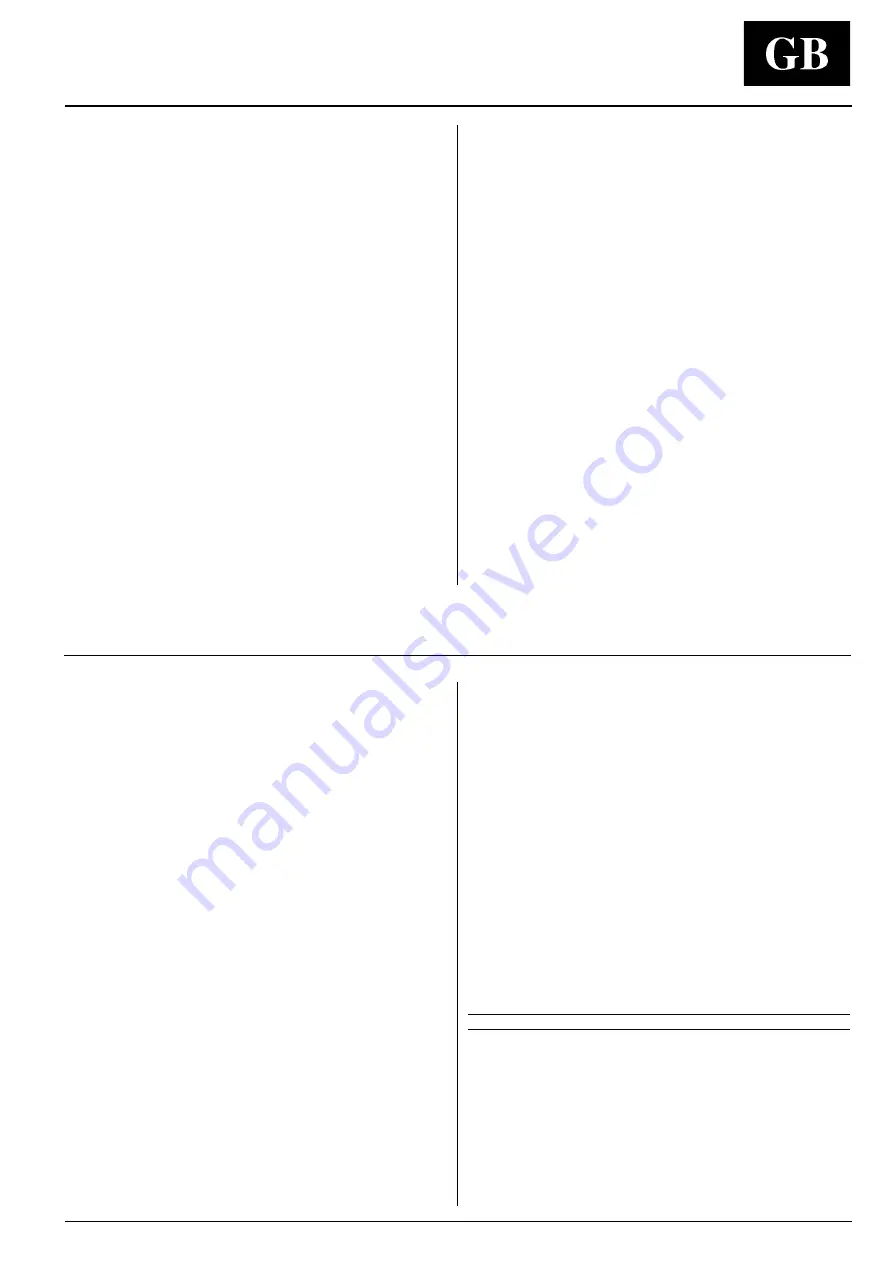
GB - 11
61 AF
E N G L I S H
Electrical connections and refrigerant charge
Electronic control
Operation and control of all units is carried out via the electronic control.
The instructions supplied with the control include comprehensive
descriptions.
After use, check the user interface is properly inserted into its housing
and the cover is closed by means of the screw supplied. This way, the
electronic control and the unit are protected against any impacts and
atmospheric agents.
PRO- electronic control
PRO- is an advanced numeric control system that combines
complex intelligence with great operating simplicity.
PRO- constantly monitors all machine parameters and safety
devices, and precisely manages the operation of compressor and fans
for optimum energy efficiency.
It also controls the operation of the water pump.
A powerful control system
The PID control algorithm with permanent compensation for the
difference between entering and leaving water temperature and
anticipation of load variations regulates compressor operation for
intelligent leaving water temperature control.
To optimise power absorption, the PRO- automatically re-
calibrates the set point of the entering water temperature based on
the outside air temperature to one of the two pre-set values (occupied
building and of an unoccupied building for example).
PRO- control is auto-adaptive for full compressor protection.
The system permanently optimises compressor run times according to
the application characteristics (water loop inertia), preventing excessive
cycling. In most comfort air conditioning applications this feature makes
a buffer tank unnecessary.
Clear and easy-to-use control system
The operator interface is clear and user-friendly: two LEDs and digital
displays allow the immediate control of the device operating data.
The menus offer direct access to all machine controls, including a history
of possible faults, for rapid and complete chiller fault diagnosis.
Extended communications capabilities
PRO-allows remote control and monitoring of the unit
through a wired connection: 7-8 x 0.5 mm² multiple cables. The cable
should be screened of the FROH2R or BELTEN 9842 type.
The screening should be grounded only on the electric unit panel
board. Functions available are start/stop, power demand limit or dual
set-point and customer safety lock.
The system permits remote signalling of any general anomaly for each
refrigerant circuit.
Three independent time schedules permit definition of: chiller start/
stop, operation at the second set-point (e.g. unoccupied mode), and
operation at low fan speed (e.g. during the night).
This option also permits cascade operation of two units and remote
control via communication bus (RS 485 serial port).
Unit start-up is done by the electronic control described above, and
must always be carried out under the supervision of a qualified air
conditioning engineer.
This appliance is not intended for use by persons (including children)
with reduced physical, sensory or mental capabilities, or lack of
experience and knowledge, unless they have been given supervision or
instruction concerning use of the appliance by a person responsible for
their safety.
Children should be supervised to ensure that they do not play with the
appliance.
Necessary checks/precautions before start-up
- Ensure that all electrical connections are properly tightened.
- Ensure that the unit is level and well-supported.
- Check that the hydraulic circuit has sufficient water flow and that the
pipe connections correspond to the installation diagram.
- Ensure that there are no water losses. Check the correct operation of
the valves installed.
- All panels should be fitted and firmly secured with the corresponding
screws.
- Make sure that there is sufficient space for servicing and maintenance
purposes.
- Ensure that there are no refrigerant leaks.
- Confirm that the electrical power source agrees with the unit
nameplate rating, wiring diagram and other documentation for the
unit.
- Ensure that the power supply corresponds to the applicable
standards.
- Make sure that compressors float freely on the mounting springs. ±
Description of unit protection devices
The unit includes the following protection devices.
- Internal compressor protection.
- Fan motor internal thermal protection.
- Main switch. (Only for size 019)
- Anti-short-cycle protection.
- Thermomagnetic control switch
- Fan circuit breaker, heaters and compressor.
- Defrost thermostat.
- Fault detector for the temperature and pressure sensors.
- High pressurestat: this protects the unit against excessive condensing
pressure.
The high pressurestat has factory-fixed non-adjustable settings. The
appliance stops due to the intervention of the high pressure alarm
threshold, before the high pressurestat intervenes.
This function is performed by the electronic control device via a
pressure transducer.
- Low pressurestat: this function is performed by the electronic control
device via a pressure transducer.
Table III: Pressure switch settings
Cut Out [bar] Reset
High Pressure state
31.3 ± 0.7
Manual
WARNING:
Alteration of factory settings other than the design set-
point, without manufacturer's authorisation, may void the warranty.
In case of use other than the manufacturer configuration, Carrier Service
must be asked for permission to change the Pro- system
configuration.
Start-up