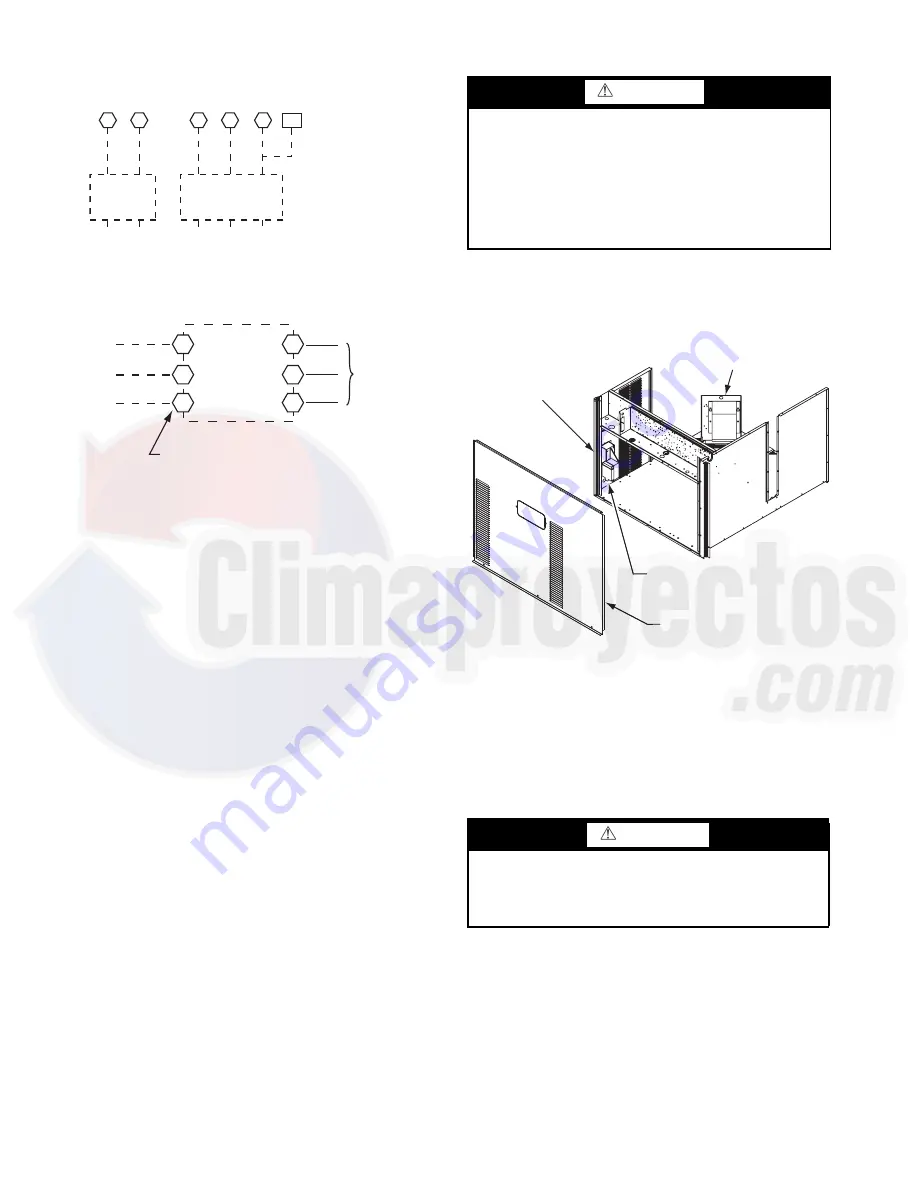
16
Fig. 21 — Power Wiring Connections
ALL UNITS
All field wiring must comply with NEC and all local codes.
Size wire based on MCA (Minimum Circuit Amps) on the unit
informative plate. See Fig. 21 and the unit label diagram for
power wiring connections to the unit power terminal blocks
and equipment ground. Maximum wire size is #2ga AWG
(copper only) per pole.
Provide a ground fault and short circuit over-current protection
device (fuse or breaker) per NEC Article 440 (or local codes).
Refer to unit informative data plate for MOCP (Maximum
Over-Current Protection) device size.
All field wiring must comply with the NEC and local requirements.
All units except 208/230v units are factory wired for the volt-
age shown on the nameplate.
If the 208/230v unit is to be con-
nected to a 208v power supply, the control transformer must be
rewired by removing the black wire with the
1
/
4
-in. female
spade connector from the 230v connection and moving it to the
200v
1
/
4
-in. male terminal on the primary side of the transform-
er. Refer to unit label diagram for additional information.
Field power wires will be connected at line-side pressure lugs
on the power terminal block or at factory-installed option non-
fused disconnect.
NOTE: Check all factory and field electrical connections for
tightness.
Voltage to compressor terminals during operation must be
within voltage range indicated on unit nameplate. On 3-phase
units, voltages between phases must be balanced within 2%
and the current within 10%. Use the formula shown in the ex-
ample below to determine the percent of voltage imbalance.
Operation on improper line voltage or excessive phase imbal-
ance constitutes abuse and may cause damage to electrical
components. Such operation would invalidate any applicable
Carrier warranty.
NOTE: Check all factory and field electrical connections for tight-
ness.
CONVENIENCE OUTLETS
Two types of convenience outlets are offered on 50HCQ mod-
els: non-powered and unit-powered. Both types provide a 125-
volt GFCI (ground-fault circuit interrupter) duplex receptacle
rated at 15A behind a hinged waterproof access cover, located
on the end panel of the unit. See Fig. 22.
Fig. 22 — Convenience Outlet Location
Installing Weatherproof Cover
A weatherproof while-in-use cover for the factory-installed
convenience outlets is now required by UL standards. This
cover cannot be factory-mounted due its depth; it must be in-
stalled at unit installation. For shipment, the convenience outlet
is covered with a blank cover plate.
The weatherproof cover kit is shipped in the unit’s control box.
The kit includes the hinged cover, a backing plate, and gasket.
1. Remove the blank cover plate at the convenience outlet;
discard the blank cover.
2. Loosen the two screws at the GFCI duplex outlet, until
approximately
1/2
in. (13 mm) under screw heads is
exposed. Press the gasket over the screw heads.
3. Slip the backing plate over the screw heads at the keyhole
slots and align with the gasket; tighten the two screws
until snug (do not over-tighten).
4. Mount the weatherproof cover to the backing plate as
shown in Fig. 23.
Units Without Disconnect Option
Units With Disconnect Option
2
4
6
1
3
5
L1
L2
L3
Optional
Disconnect
Switch
Disconnect factory test leads; discard.
Factory
Wiring
11
13
13
L1
L2
L3
TB
C
IFC
(3 Phase
Indoor Motor)
(1 Phase Indoor Motor
and 3 Phase Unit)
208/230-3-60
460-3-60
575-3-60
Disconnect
per
NEC
11
23
C
208/230-1-60
Disconnect
per
NEC
WARNING
ELECTRICAL OPERATION HAZARD
Failure to follow this warning could result in personal
injury or death.
Units with convenience outlet circuits may use multiple
disconnects. Check convenience outlet for power status
before opening unit for service. Locate its disconnect
switch, if appropriate, and open it. Lock-out and tag-out
this switch, if necessary.
WARNING
Failure to follow this warning could result in personal
injury or death.
Disconnect all power to unit and convenience outlet.
Lock-out and tag-out all power.
CONVENIENCE
OUTLET GFCI
PWD-CO FU
S
E
S
WITCH
PWD-CO TRAN
S
FORMER
CONTROL BOX
ACCE
SS
PANEL
Summary of Contents for 50HCQ07
Page 4: ...4 Fig 2 Unit Dimensional Drawing 07 08 Size Units ...
Page 5: ...5 Fig 2 Unit Dimensional Drawing 07 08 Size Units cont ...
Page 6: ...6 Fig 3 Unit Dimensional Drawing 09 Size Units ...
Page 7: ...7 Fig 3 Unit Dimensional Drawing 09 Size Units cont ...
Page 24: ...24 Fig 37 Electro Mechanical Control Wiring 50HCQ A07 D07 208 230v 460v 575v ...
Page 25: ...25 Fig 38 Electro Mechanical Control Wiring 50HCQ D07 Tier 2 1 Compressor 208 230v 460v 575v ...
Page 26: ...26 Fig 39 Electro Mechanical Control Wiring 50HCQ 08 09 208 230v 460v 575v ...
Page 27: ...27 Fig 40 Electro Mechanical Power Wiring 50HCQ A07 D07 208 230v 460v 575v ...
Page 28: ...28 Fig 41 Electro Mechanical Power Wiring 50HCQ D07 Tier 2 1 Compressor 208 230v 460v 575v ...
Page 29: ...29 Fig 42 Electro Mechanical Power Wiring 50HCQ 08 09 208 230v 460v 575v ...
Page 30: ...30 Fig 43 PremierLink Wiring Schematic 50HCQ07 09 208 230v 460v 575v ...
Page 31: ...31 Fig 44 RTU Open System Control Wiring ...
Page 49: ......