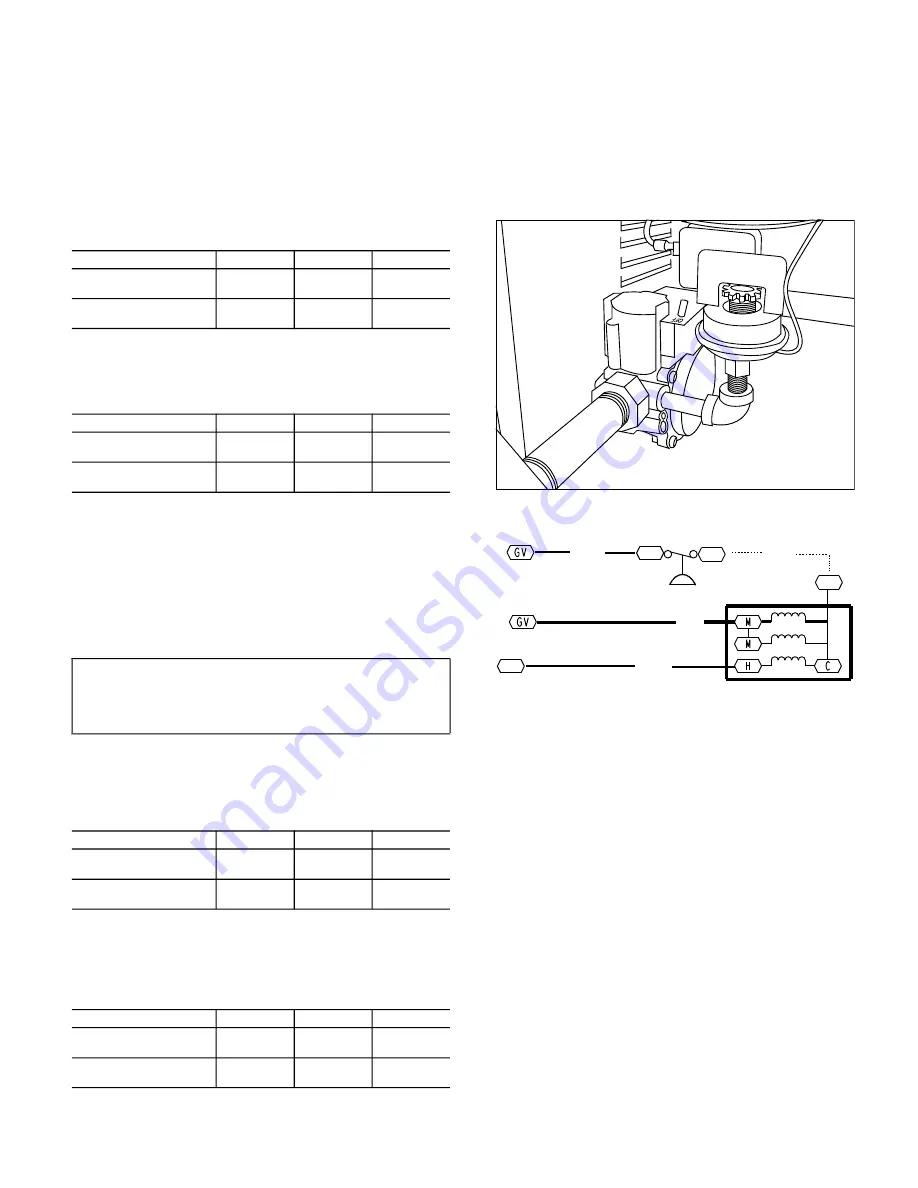
25
Fuel Types and Pressures
NATURAL GAS
The 48JC unit is factory-equipped for use with natural gas
(NG) fuel at elevation under 2000 ft (610 m). See section “Ori
-
fice Replacement” for information in modifying this unit for
installation at elevations above 2000 ft (610 m).
Gas line pressure entering the unit’s main gas valve must be
within specified ranges (see Table 5). Adjust unit gas regulator
valve as required or consult local gas utility.
Manifold pressure is factory-adjusted for NG fuel use. Adjust
as required to obtain best flame characteristic. (See Table 6.)
LIQUID PROPANE
Accessory packages are available for field-installation that will
convert the 48JC unit (except low NOx model) to operate with
liquid propane (LP) fuels. These kits include new orifice spuds,
new springs for gas valves and a supply line low pressure switch.
See High Altitude Gas Conversion Kit Gas Heating/Electric
Cooling 3 to 15 Ton Small Rooftop Units Accessory LP (Liquid
Propane) Installation Instructions for details on orifice size
selections.
Fuel line pressure entering unit gas valve must remain within
specified range. (See Table 7.)
Manifold pressure for LP fuel use must be adjusted to specified
range (see Table 8). Follow instructions in the accessory kit to
make initial readjustment.
SUPPLY PRESSURE SWITCH
The LP conversion kit includes a supply low pressure switch.
The switch contacts (from terminal C to terminal NO) will
open the gas valve power whenever the supply line pressure
drops below the set point. See Fig. 43 and 44. If the low
pressure remains open for 15 minutes during a call for heat, the
IGC circuit will initiate a Ignition Fault (5 flashes) lockout. Re
-
set of the low pressure switch is automatic on rise in supply
line pressure. Reset of the IGC requires a recycle of unit power
after the low pressure switch has closed.
Fig. 43 —
LP Low Pressure Switch (Installed)
Fig. 44 —
LP Supply Line Low Pressure
Switch Wiring
This switch also prevents operation when the propane tank lev
-
el is low, which can result in gas with a high concentration of
impurities, additives, and residues that have settled to the bot
-
tom of the tank. Operation under these conditions can cause
harm to the heat exchanger system. Contact your fuel supplier
if this condition is suspected.
Flue Gas Passageways
To inspect the flue collector box and upper areas of the heat ex
-
changer:
1. Remove the combustion blower wheel and motor assem
-
bly according to directions in Combustion-Air Blower sec
-
tion. See Fig. 45.
2. Remove the flue cover to inspect the heat exchanger.
3. Clean all surfaces as required using a wire brush.
Combustion-Air Blower
Clean periodically to assure proper airflow and heating effi
-
ciency. Inspect blower wheel every fall and periodically during
heating season. For the first heating season, inspect blower
wheel every two months to determine proper cleaning frequency.
To access burner section, slide the burner partition panel out of
the unit.
Table 5 —
Natural Gas Supply Line Pressure Ranges
UNIT MODEL
UNIT SIZE
MIN
MAX
48JCD/E/S/R
04, 05, 06
4.0 in. wg
(996 Pa)
13.0 in. wg
(3240 Pa)
48JCF/T
(High Heat Units Only)
05, 06
5.0 in. wg
(1245 Pa)
13.0 in. wg
(3240 Pa)
Table 6 —
Natural Gas Manifold Pressure Ranges
UNIT MODEL
UNIT SIZE
HIGH FIRE
LOW FIRE
48JCD/E/S/R
04, 05, 06
3.5 in. wg
(872 Pa)
1.7 in. wg
(423 Pa)
48JCF/T
(High Heat Units Only)
05, 06
3.5 in. wg
(872 Pa)
1.7 in. wg
(423 Pa)
IMPORTANT: Low NOx models include specially-sized
orifices and use of different flue flow limits and tube baf
-
fles. Because of these extra features, conversion of these
models to LP is not recommended.
Table 7 —
Liquid Propane Supply Line Pressure
Ranges
UNIT MODEL
UNIT SIZE
MIN
MAX
48JCD/E/S/R
04, 05, 06
11.0 in. wg
(2740 Pa)
13.0 in. wg
(3240 Pa)
48JCF/T
(High Heat Units Only)
05, 06
11.0 in. wg
(2740 Pa)
13.0 in. wg
(3240 Pa)
Table 8 —
Liquid Propane Manifold Pressure Ranges
UNIT MODEL
UNIT SIZE
MIN
MAX
48JCD/E/S/R
04, 05, 06
10 in. wg
(2490 Pa)
5 in. wg
(1245 Pa)
48JCF/T
(High Heat Units Only)
05, 06
10 in. wg
(2490 Pa)
5 in. wg
(1245 Pa)
PNK
W2
TSTAT
GRA
BRN
IGC
J2-12
IGC
J2-11
BRN
C
NO
MGV
C
LP LPS
Summary of Contents for 48JC04-06
Page 15: ...15 Fig 26 Condenser Fan Assembly Screw Pattern Sequence 1 2 3 4 5 NO SCREW Blank Tab...
Page 30: ...30 Fig 52 Integrated Gas Controller IGC Board RED LED STATUS...
Page 64: ...64 APPENDIX D WIRING DIAGRAMS Fig B 48JC 04 06 Control Wiring Diagram...
Page 65: ...65 APPENDIX D WIRING DIAGRAMS Fig C 48JC 04 06 Power Wiring Diagram 208 230 460 3 60...