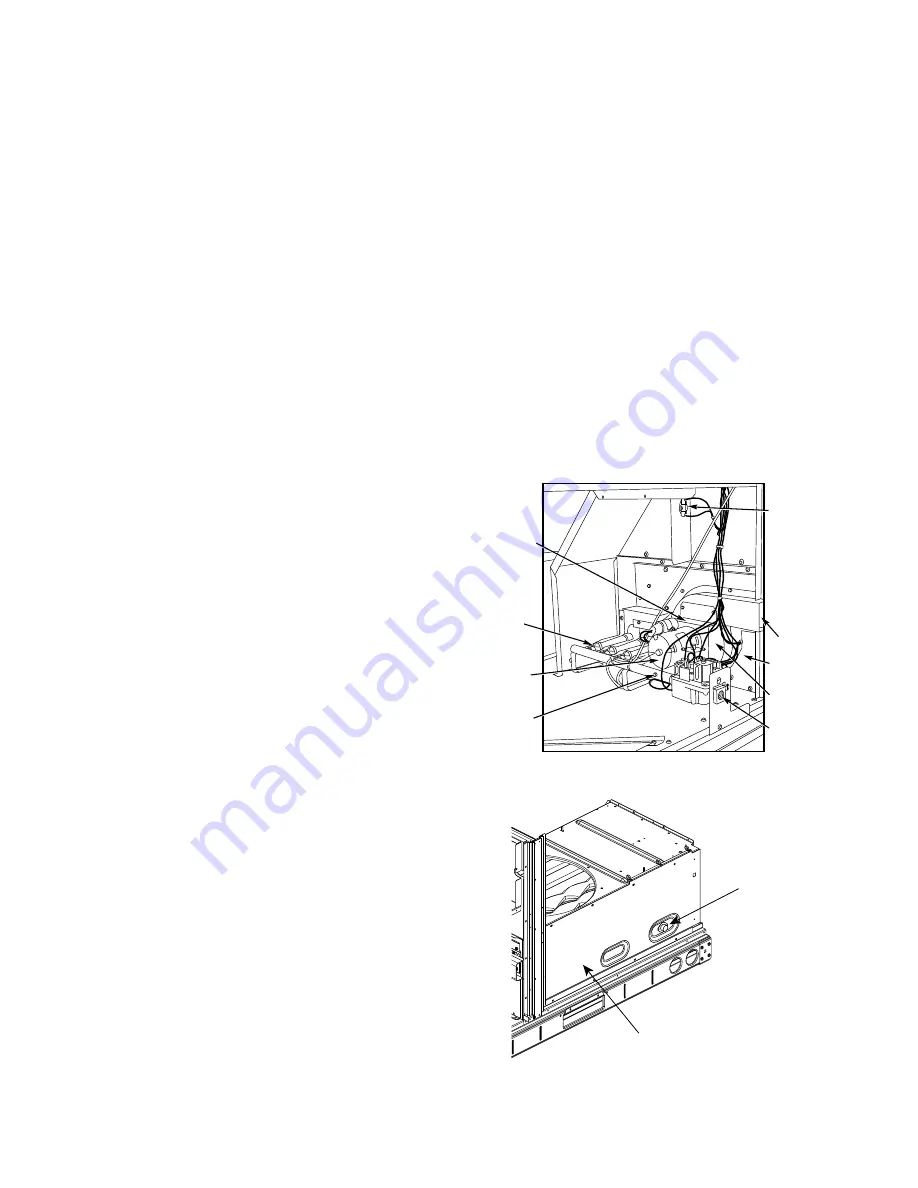
24
2. Check the wiring between the sensor and the controller. If
wiring is loose or missing, repair or replace as required.
CONTROLLER’S POWER LED IS OFF
1. Make sure the circuit supplying power to the controller is
operational. If not, make sure JP2 and JP3 are set correctly
on the controller before applying power.
2. Verify that power is applied to the controller’s supply
input terminals. If power is not present, replace or repair
wiring as required.
REMOTE TEST/RESET STATION’S TROUBLE LED DOES
NOT FLASH WHEN PERFORMING A DIRTY TEST, BUT
THE CONTROLLER’S TROUBLE LED DOES
1. Verify that the remote test/station is wired as shown in
Fig. 38. Repair or replace loose or missing wiring.
2. Configure the sensor dirty test to activate the controller’s
supervision relay. See “Dirty Sensor Test” on page 21.
SENSOR’S TROUBLE LED IS ON, BUT THE CONTROL
-
LER’S TROUBLE LED IS OFF
Remove JP1 on the controller.
PROTECTIVE DEVICES
Compressor Protection
OVERCURRENT
The compressor has internal line-break motor protection.
OVERTEMPERATURE
The compressor has an internal protector to protect it against
excessively high discharge gas temperatures.
HIGH PRESSURE SWITCH
The system is provided with a high pressure switch mounted on
the discharge line. The switch is stem-mounted and brazed into the
discharge tube. Trip setting is 630 psig ± 10 psig (4344 ± 69 kPa)
when hot. Reset is automatic at 505 psig (3482 kPa).
LOW PRESSURE SWITCH
The system is protected against a loss of charge and low evapo
-
rator coil loading condition by a low pressure switch located on
the suction line near the compressor. The switch is stem-
mounted. Trip setting is 54 psig ± 5 psig (372 ± 34 kPa). Reset
is automatic at 117 ± 5 psig (807 ± 34 kPa).
EVAPORATOR FREEZE PROTECTION
The system is protected against evaporator coil frosting and low
temperature conditions by a temperature switch mounted on the
evaporator coil hairpin. Trip setting is 30°F ± 5°F (–1°C ± 3°C).
Reset is automatic at 45°F (7°C).
SUPPLY (INDOOR) FAN MOTOR PROTECTION
Disconnect and lockout power when servicing fan motor.
The standard supply fan motor is equipped with internal over
-
current and over-temperature protection. Protection devices re
-
set automatically.
The high static option supply fan motor is equipped with a pi
-
lot-circuit Thermix combination over-temperature/over-current
protection device. This device resets automatically. Do not by
-
pass this switch to correct trouble. Determine the cause and
correct it.
CONDENSER FAN MOTOR PROTECTION
The condenser fan motor is internally protected against over-
temperature.
Relief Device
A soft solder joint at the suction service access port provides
pressure relief under abnormal temperature and pressure condi
-
tions (i.e., fire in building). Protect this joint during brazing
operations near this joint.
Control Circuit, 24-V
The control circuit is protected against overcurrent conditions
by a circuit breaker mounted on control transformer TRAN.
Reset is manual.
GAS HEATING SYSTEM
General
The heat exchanger system consists of a gas valve feeding mul
-
tiple in-shot burners off a manifold. The burners fire into
matching primary tubes. The primary tubes discharge into
combustion plenum where gas flow converges into secondary
tubes. The secondary tubes exit into the induced draft fan
wheel inlet. The induced fan wheel discharges into a flue pas
-
sage and flue gases exit out a flue hood on the side of the unit.
The induced draft fan motor includes a flue gas pressure switch
circuit that confirms adequate wheel speed through the Inte
-
grated Gas Controller (IGC) board. Safety switches include a
Rollout Switch (at the top of the burner compartment; see Fig. 41)
and a limit switch (mounted through the heat exchanger cover
panel, over the tubes). (See Fig. 42.)
Fig. 41 —
Burner Section Details
Fig. 42 —
Limit Switch Location
INDUCED-
DRAFT
MOTOR
MOUNTING
PLATE
INDUCED-
DRAFT
MOTOR
MANIFOLD
PRE
SS
URE
TAP
VE
S
TIBULE
PLATE
FLUE
EXHAU
S
T
ROLLOUT
S
WITCH
BLOWER
HOU
S
ING
GA
S
VALVE
BURNER
S
ECTION
HEAT EXCHANGER
COVER PANEL
GAS LIMIT
SWITCH
Summary of Contents for 48JC04-06
Page 15: ...15 Fig 26 Condenser Fan Assembly Screw Pattern Sequence 1 2 3 4 5 NO SCREW Blank Tab...
Page 30: ...30 Fig 52 Integrated Gas Controller IGC Board RED LED STATUS...
Page 64: ...64 APPENDIX D WIRING DIAGRAMS Fig B 48JC 04 06 Control Wiring Diagram...
Page 65: ...65 APPENDIX D WIRING DIAGRAMS Fig C 48JC 04 06 Power Wiring Diagram 208 230 460 3 60...