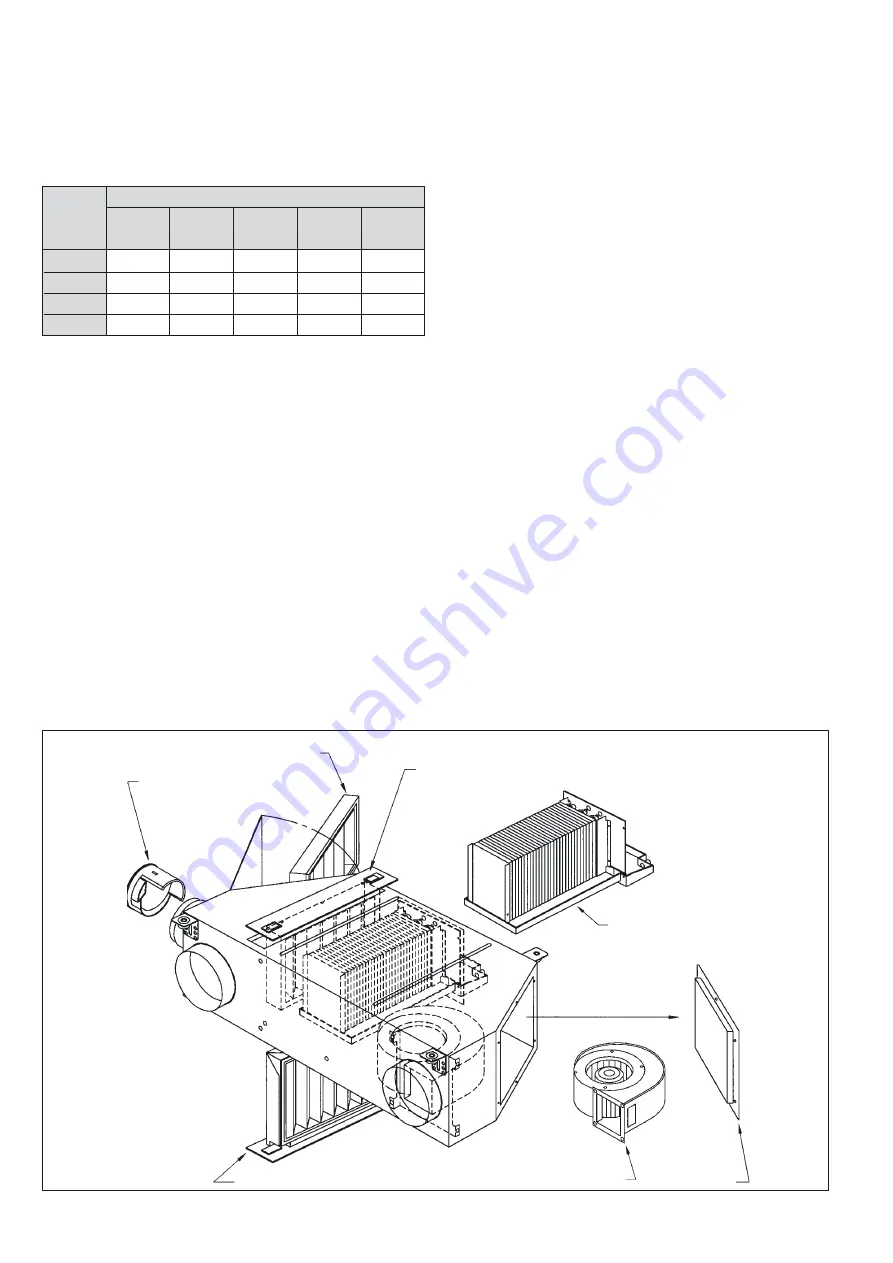
12
Palletised
Size 1
10
1600
1100
1500
320
Size 2
10
1700
1350
1500
450
Size 3
10
1 700
1 350
1 500
430
Size 4
6
1 800
1 350
1 200
410
Units per
pallet
Length
(mm)
Width
(mm)
Height
(mm)
Weight
(kg)
NOTE:
When receiving a shipment of units, check at once that none
of the packages has been damaged. To maintain the protec-
tion of the packaging as long as possible, do not open any
package until just before a unit is to be installed.
2.3 - ULTRA packaging
Packaged on wooden pallets and protected by heat-shrunk or
stretchable plastic film.
NOTE:
If “Export” packaging is needed, please contact your local
Carrier representative.
2.4 - Receiving a shipment - installation methods
When receiving a shipment, check the condition of the goods
and report any damage in transit to the shipping company. Do
not unpack the units until just before they are due to be instal-
led, and make sure they are as close as possible to the installa-
tion site when unpacking them. Do not stack the units and do
not place heavy articles of any sort on them.
WARNING:
When moving the units do not use water pipe connections or
condensate drain stubs, valves or flexible pipes as handles.
The presence of electrical components creates hazards to those
installing and servicing these units. Only properly qualified
electricians may be authorised to install, service and repair
these units. Some routine maintenance such as cleaning of the
coils and filter replacement may be entrusted to non-skilled
personnel. Before carrying out any work, qualified technicians
must familiarise themselves with the contents of this manual
and all informative tags and labels attached to the units. It is
essential to adhere to all applicable safety regulations. Wear
eye protectors, work gloves and non-flammable clothing when
soldering or brazing. Always have a fire extinguisher of the
appropriate type close at hand.
WARNING:
Disconnect the power supply to the unit and to any accesso-
ries before carrying out any work on a unit.
Do not install a unit where flammable gases or products of an
acidic or alkaline character may be present. The copper/alumi-
nium coil or plastic components inside the unit could suffer
irreparable corrosion damage in their presence.
WARNING:
Failure to take proper account of the above advice and
unauthorised modification of the electrical connections will
render the warranty on the product null and void.
FRESH AIR CONTROLLER
LATERAL FILTER ACCESS OPTION
FILTER TOP ACCESS
OPTION
FILTER ACCESS OPTION FROM BELOW
DRAIN PAN AND
COIL ASSEMBLY
FAN MOTOR ASSEMBLY
FAN ACCESS
PANELS