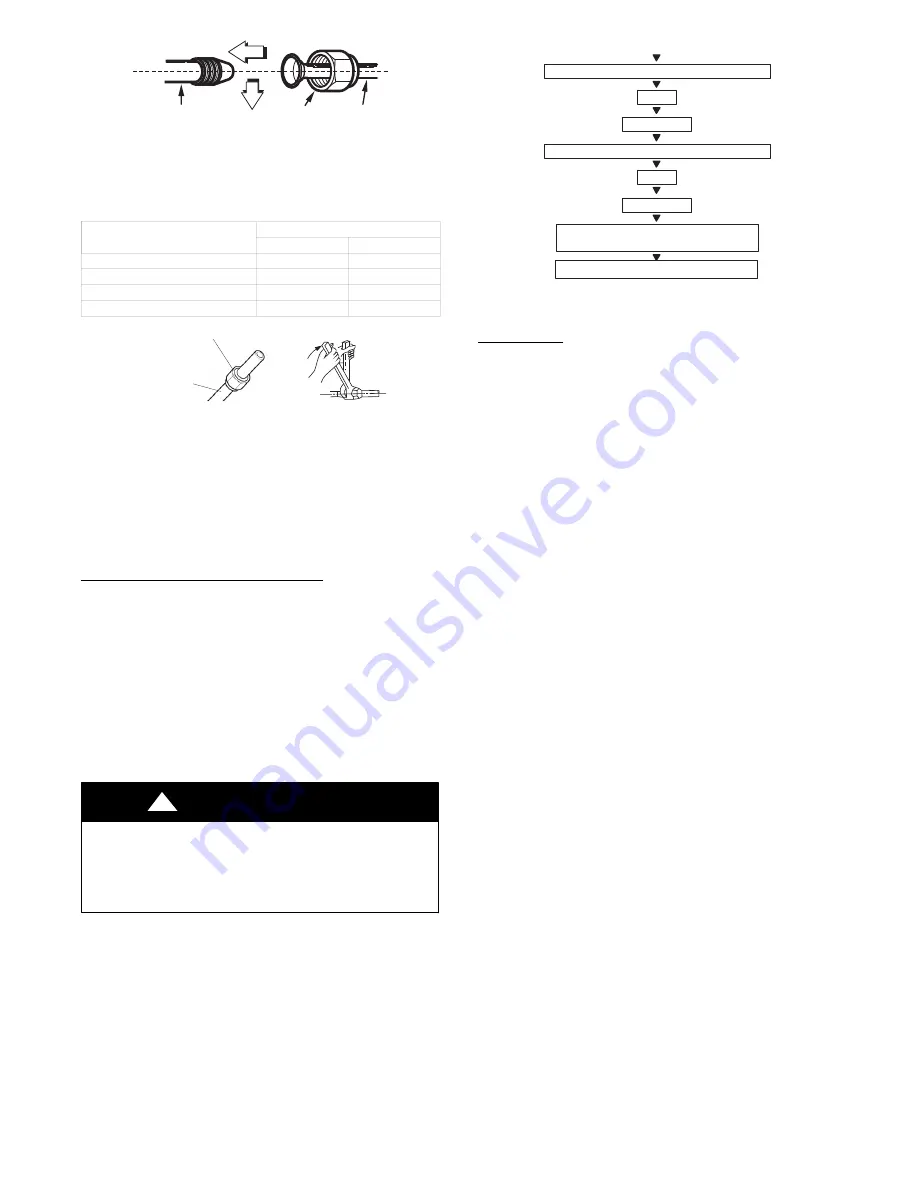
16
Indoor unit tubing
Flare nut
Piping
Fig. 40
-
Align Pipe Center
h. Connect both the liquid and gas piping to the indoor unit.
i. Tighten the flare nut using a torque wrench as specified in
Table 7.
Table 7—Tightening Torque
PIPE DIAMETER INCH (mm)
TIGHTENING TORQUE
Ft-lb
N-m
Ø
1/4
”
(6.35)
10 to 13
13.6 to 17.6
Ø
3/8
”
(9.52)
24 to 31
32.5 to 42.0
Ø
1/2
”
(12.7)
37 to 46
50.1 to 62.3
Ø
5/8
”
(15.88)
50 to 60
67.7 to 81.3
Flare nut
Copper tube
Fig. 41
-
Tighten the Flare Nut
6. Connect the drain line. The drain line must not have a trap
anywhere in its length. The drain line must pitch downwards.
The drain line must be insulated up to the outside wall.
NOTE: For applications where gravity cannot be used for
drainage, a condensate pump accessory is available. Consult the
condensate pump Installation Instructions for more information.
WIRELESS REMOTE CONTROL INSTALLATION
Mounting Bracket (if installed on the wall)
1. Use the two screws supplied with the control to attach the
mounting bracket to the wall in a location selected by the
customer and within operating range.
2. Install the remote control batteries.
3. Place the remote control into the remote control mounting
bracket.
4. For remote control operation, refer to unit owner’s manual.
WIRED REMOTE CONTROLLER
For setup instructions, refer to the wired controller installation
manual. Refer to Fig. 23 for the 4 and 5 Pin connections for the
different wired remote controllers.
UNIT DAMAGE HAZARD
Failure to follow this caution may result in equipment
damage or improper operation.
Never use the system compressor as a vacuum pump.
CAUTION
!
Refrigerant tubes and the indoor coil should be evacuated using the
recommended deep vacuum method (500 microns). The alternate
triple evacuation method may be used if the procedure outlined
below is followed. Always break a vacuum with dry nitrogen.
FINAL TUBING CHECK
IMPORTANT: Ensure certain factory tubing on the indoor unit
has not shifted during shipment. Ensure tubes are not rubbing
against each other or any sheet metal. Pay close attention to the
feeder tubes, making sure the wire ties on the feeder tubes are
secure and tight.
EVACUATE
EVACUATE
CHECK FOR TIGHT, DRY SYSTEM
(IF IT HOLDS DEEP VACUUM)
BREAK VACUUM WITH DRY NITROGEN
WAIT
RELEASE CHARGE INTO SYSTEM
EVACUATE
BREAK VACUUM WITH DRY NITROGEN
WAIT
Fig. 42
-
Triple Evacuation Method
START−UP
Test Operation
Perform a test operation after completing a gas leak and electrical
safety check.
1. Press ON/OFF (on the remote control) to begin testing.
NOTE: A protection feature prevents the air conditioner from
being activated for approximately 3 to 4 minutes.
2. Press MODE and select the COOLING, HEATING, FAN
modes to ensure all the functions work correctly.
3. To run the test using the manual button in the indoor unit:
(1.) Open the indoor unit’s front panel;
(2.) Press manual switch once to energize the unit. Set
conditions of the manual operation are as follows:
· Preset set point: 76
_
F (24
_
C)
· Fan speed: AUTO
· Discharge air direction: Pre−set position based on
operation in COOL or HEAT mode.
4. Be sure to set the manual switch to OFF (by pressing it
twice again) after finishing the test operation.
SYSTEM CHECKS
1. Conceal the tubing where possible.
2. Ensure the drain tube slopes downward along its entire
length.
3. Ensure all tubing and connections are properly insulated.
4. Fasten the tubes to the outside wall, when possible.
5. Seal the hole through which the cables and tubing pass.
INDOOR UNIT
1. Do all the remote control buttons function properly?
2. Do the display panel lights work properly?
3. Does the air deflection louver function properly?
4. Does the drain work?
OUTDOOR UNIT
1. Are there unusual noises or vibrations during operation?
Explain Following Items To Customer
(with the aid of the Owner’s Manual):
1. How to turn the air conditioner on and off; selecting
COOLING, HEATING and other operating modes;
setting a desired temperature; setting the timer to
automatically start and stop the air conditioner operation;
and all other features of the remote control and display
panel.
2. How to remove and clean the air filter.
3. How to set air deflection louver.
4. Explain care and maintenance.
5. Present the owner’s manual and installation instructions to
customer.