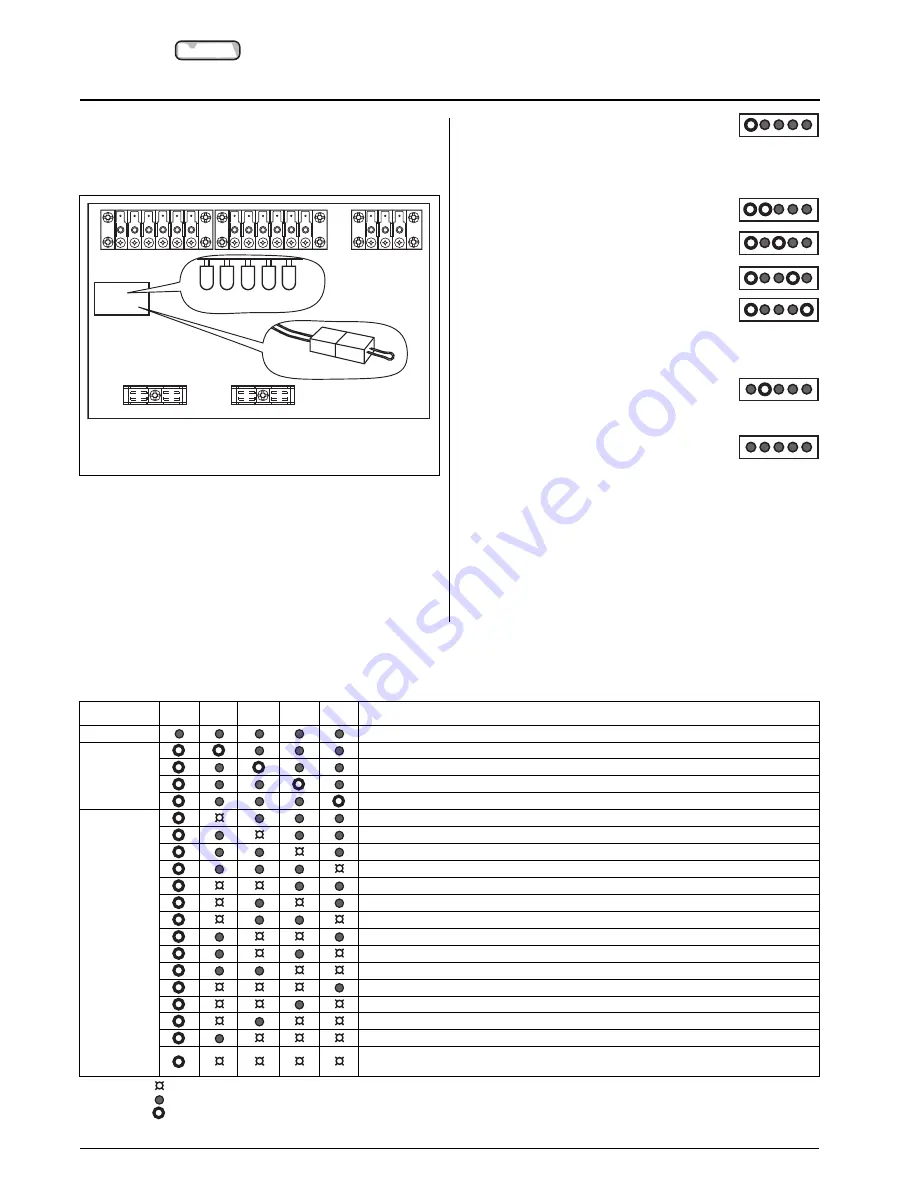
38VYM
R-410A
GB - 12
Incorrect wiring and piping procedure check
This procedure only applies to models 38VYM-28 and 38VYM-32.
The incorrect wiring/piping procedure check can be performed at an
ambient temperature of 5
°
C or more.
Sequence with electrical and refrigerant connections correctly
carried out:
• Position the red connector
outside of terminal block zone.
• Switch the main power supply ON and start all indoor units in
cooling mode.
• Disconnect the red connector
(incorrect wiring/piping test),
with compressor OFF.
• Start the test sequence for incorrect wiring/piping.
• The yellow LED
flashes (D800).
• During the test for incorrect wiring/piping, the
compressor starts operating at a fixed frequency, the outdoor unit
fan operates normally, the indoor unit fans remain OFF.
• The yellow LED
and red LED
flash
(D800 and D801).
• The yellow LED
and red LED
flash
(D800 and D802).
• The yellow LED
and red LED
flash
(D800 and D803).
• The yellow LED
and red LED
flash
(D800 and D804).
• Normally the test procedure for incorrect
wiring/piping lasts from 3 to 15 minutes.
• When the test procedure is completed, the compressor and
outdoor unit fan stop operation, the red LED
(D801) flashes, while the yellow one
(D800) is
OFF.
• If no incorrect wiring/piping has been found, system automatically
restarts and the red LED
(D801) that was
flashing, turns OFF.
• Reconnect the red connector
.
At the end of the test, if there is a fault code, the yellow LED
(D800) flashes and the red LEDs that indicate the defect remain ON
(see table).
The compressor does not start and the indoor unit fans operate in
fan only mode.
After the defect has been corrected, repeat the procedure and carry
out another check.
CHECK LED
LED
LED
D800
D801
D802
D803
D804
Description
Normal operation (no fault)
Checking unit A1
Check
Checking unit A2
Checking unit A3
*
Checking unit A4
Kinking/clogging of pipe unit A1
Kinking/clogging of pipe unit A2
Kinking/clogging of pipe unit A3
*
Kinking/clogging of pipe unit A4
Incorrect wiring/piping or kinking/clogging of pipe unit A1, A2
Incorrect wiring/piping or kinking/clogging of pipe unit A1, A3
*
Incorrect wiring/piping or kinking/clogging of pipe unit A1, A4
Fault
Incorrect wiring/piping or kinking/clogging of pipe unit A2, A3
*
Incorrect wiring/piping or kinking/clogging of pipe unit A2, A4
*
Incorrect wiring/piping or kinking/clogging of pipe unit A3, A4
Incorrect wiring/piping of pipe unit A1, A2, A3
Incorrect wiring/piping of pipe unit A1, A2, A4
Incorrect wiring/piping of pipe unit A1, A3, A4
Incorrect wiring/piping of pipe unit A2, A3, A4
Incorrect wiring/piping of packed valve,
that keeps the circuit closed, unit A1, A2, A3, A4
Table IV: Check for incorrect wiring/piping
Legend:
LED ON
LED OFF
LED flashing
*
Only for 38VYM-32 model
Red LED (D803)
Red LED (D804)
Red connector
Yellow LED (D800)
Red LED (D801)
Red LED (D802)