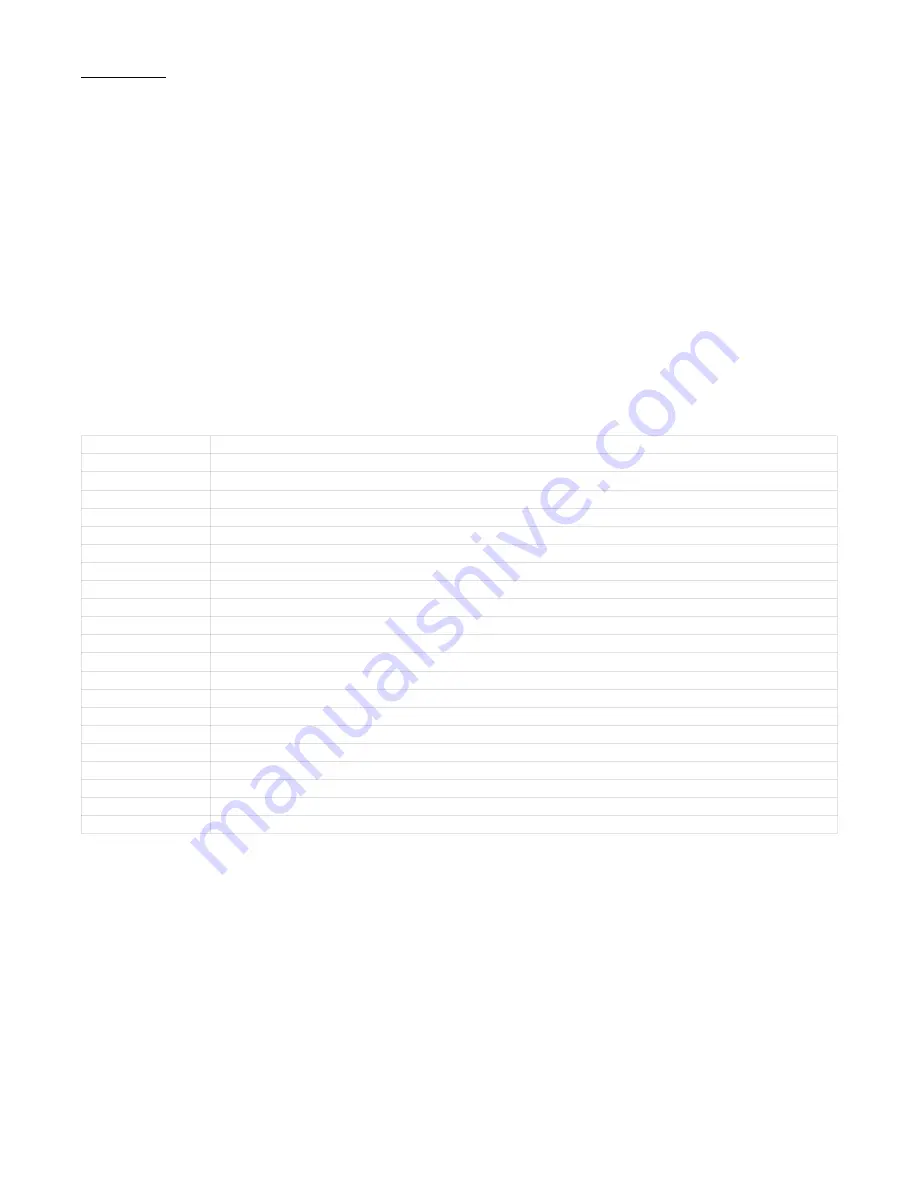
13
START−UP
Test Operation
Perform a test operation after completing a gas leak and electrical
safety check. See the indoor unit installation instructions and
owner’s manual for additional start up information.
SYSTEM CHECKS
1. Conceal the tubing where possible.
2. Make sure that the drain tube slopes downward along its
entire length.
3. Ensure all tubing and connections are properly insulated.
4. Fasten the tubes to the outside wall, when possible.
5. Seal the hole through which the cables and tubing pass.
OUTDOOR UNIT
1. Are there unusual noises or vibrations during operation?
Explain the Following Items to the Customer (with the aid of
the Owner’s Manual):
1. Explain care and maintenance.
2. Present the installation instructions to the customer.
OUTDOOR UNIT DIAGNOSTIC GUIDES
For ease of service, the systems are equipped with a diagnostic code display LEDs on both the indoor and outdoor units. The outdoor
diagnostic is displayed on the outdoor unit microprocessor board.
There may be a few error codes displayed in the indoor unit that might relate to the outdoor unit’s problems. If possible, always check the
diagnostic codes displayed on the indoor unit first.
The diagnostic codes displayed on the outdoor units are listed on Table 10.
Table 10—Unit Diagnostic Guides
DISPLAY
LED STATUS
E1
Communication malfunction between indoor and outdoor units.
F0
Protection of over-current
F1
Open circuit or short circuit of outdoor ambient temperature sensor T4
F2
Open circuit or short circuit of condenser coil temperature sensor T3
F3
Open circuit or short circuit of Compressor discharge temperature sensor T5
F4
Outdoor unit EEPROM error
F5
Outdoor fan speed has been out of control
P0
IPM malfunction
P1
Over voltage or over low voltage protection
P2
High temperature protection of compressor top
P3
Outdoor low temperature protection
P4
Inverter compressor drive error
P7
Outdoor IGBT temperature sensor error
J0
High temperature protection of indoor coil in heating
J1
Outdoor temperature protection of outdoor coil in cooling
J2
Discharge temperature protection
J3
Protection of active PFC module
J4
Communication error between control board and IPM board
J5
High-pressure switch protection
J6
Low-pressure switch protection
J8
AC voltage protection
For additional diagnostic information, refer to the Service Manual.