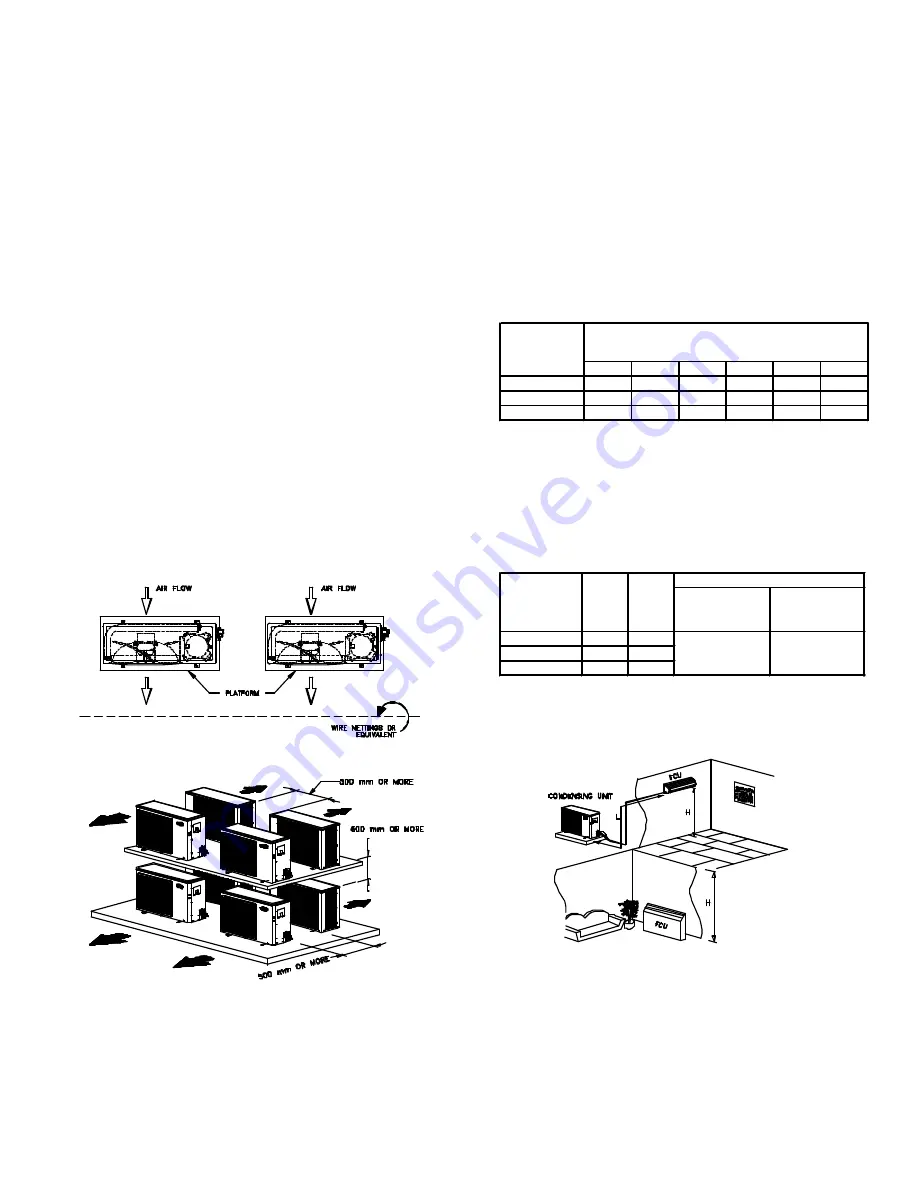
INSTALLATION
SELECTION OF MOUNTING POSITION
1) The unit should be installed outdoors.
2) A place where air will not be stagnant.
3) A place where the exhausted air will not be sucked in for
the second time.
4) Allow sufficient space for airflow clearance, wiring,
refrigerant piping and servicing unit. See Fig. 2.
5) Avoid positioning unit in such a manner that water will
pour directly onto the unit.
6) Do not install the unit near a source of heat, steam or
flammable gas.
7) Ducting of the fan inlet or discharge is not permitted.
UNIT MOUNTING
1)
MOUNTING ON GROUND
– Mount on a solid, level
concrete base. If conditions or local building codes
require unit to be fastened to base, tie down bolts
should be used and fastened through slots provided in
unit’s mounting feet (Fig. 3). Do not install unit directly
on ground.
2)
MOUNTING ON AND AGAINST THE WALL
– the
bracket is to be locally procured (Fig. 4).
3)
MOUNTING ON ROOF
– Mount on a level platform or
frame. When multiple unit are installed, the air outlet
side should be opened as shown in Fig. 5.
When installation base is used, secure the required spacing
as per (Fig. 6). Fabricate the stand so that it will have
sufficient strength.
REFRIGERANT PIPING
Size Refrigerant Lines. Consider length of piping required
between unit and evaporator, amount of liquid lift and
compressor oil return (Table 4).
Run refrigerant tubes as directly as possible, avoiding
unnecessary turns and bends. Condensing unit may be
connected to evaporator sections using field-supplied
tubing of refrigerant grade, correct size and condition.
Suspend refrigerant tubes so they do not transmit
vibration to structure. Also when passing refrigerant
tubes through walls, seal opening so vibration is not
transmitted to structure. Leave some slack in refrigerant
tubes between structure and unit to absorb vibration.
The longer the piping, the lower the cooling capacity of
the unit. See table 3.
TABLE 3 – REDUCTION IN CAPACITY VS
INCREASE IN PIPE LENGTH
MODEL
38ASB /
CCAR
5m
10m
15m
20m
25m
30m
240
0%
1.2%
2.0%
2.8%
3.5%
4.5%
360 / 036
0%
1.6%
2.6%
3.6%
4.6%
5.6%
600 / 060
0%
2.8%
4.8%
6.7%
8.7%
10.2%
PIPING LENGTH (ONE WAY)
As such the following are the operating limits. Refer to
Table 4 and fig. 7.
TABLE 4 – VERTICAL AND HORIZONTAL
SEPARATION BETWEEN INDOOR
AND OUTDOOR UNIT
MODEL
MAX.
MAX.
38ASB /
HEIGHT LENGTH MAX. ALLOWABLE MAX. ALLOWABLE
CCARS024~060
H(m)
L(m)
PRESSURE DROP TEMPERATURE
(kPa)
LOSS (
0
C)
024
(20)15
25
360 / 036
(20)15
25
600 / 060
(25)15
30
LIQUID LINE
151
5
Note:
1) Values shown are for units operating at 7.2
0
C saturated suction
and 35
0
C entering air.
2) Values in ( ) indicate a case when the outdoor unit is located at
a lower height than the indoor unit.
Do not bury section of line set underground. If any section is buried,
refrigerant may migrate to cooled buried section during extended period of
unit shutdown. This causes refrigerant slugging and possible compressor
damage at start-up.
If either refrigerant tubing or indoor coil is exposed to atmospheric
conditions for longer than 5 minutes, it must be evacuated to 1000 microns
to eliminate contamination and moisture in the system.
FIG. 5 ROOF MOUNTING
FIG. 6 MINIMUM SPACING REQUIREMENT
FIG. 7 MAXIMUM ALLOWABLE PIPING LENGTH
AND ELEVATION DIFFERENCE
4