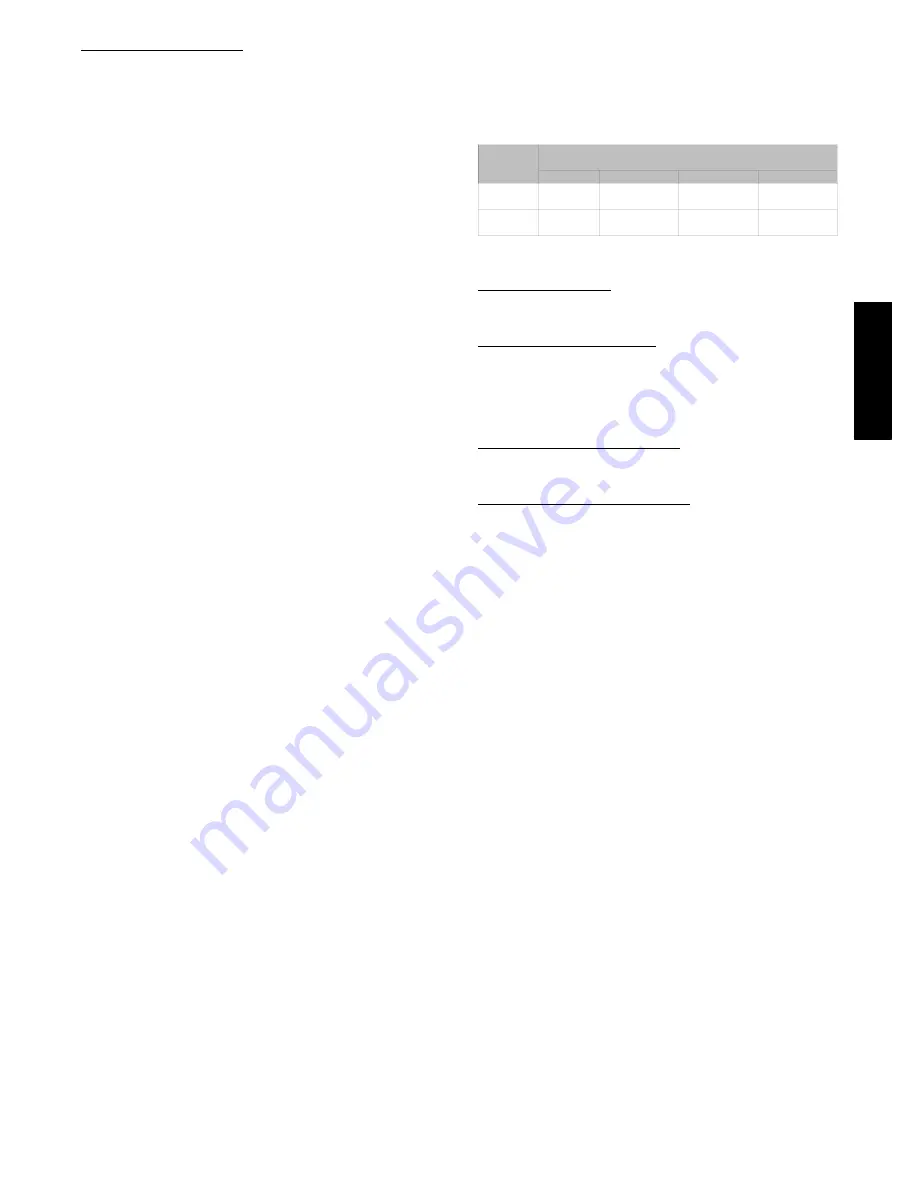
9
Unloader Test Procedure
The unloader is the compressor internal mechanism, controlled by
the DC solenoid, that modulates between high and low stage. If it
is suspected that the unloader is not working, the following
methods may be used to verify operation.
1. Operate the system and measure compressor amperage.
Cycle the unloader on and off at 30 second plus intervals at
the thermostat (from low to high stage and back to low
stage). Wait 5 seconds after staging to high before taking a
reading. The compressor amperage should go up or down
at least 20 percent.
2. If the expected result is not achieved, remove the solenoid
plug from the compressor and with the unit running and the
thermostat calling for high stage, test the voltage output at
the plug with a DC voltmeter. The reading should be 24
volts DC.
3. If the correct DC voltage is at the control circuit molded
plug, measure the compressor unloader coil resistance. The
resistance should be approximately 330 or 1640 ohms de-
pending on unloader coil supplier. If the coil resistance is
infinite or is grounded, the compressor must be replaced.
Final Checks
IMPORTANT
: Before leaving job, be sure to do the following:
1. Ensure that all wiring is routed away from tubing and sheet
metal edges to prevent rub
−
through or wire pinching.
2. Ensure that all wiring and tubing is secure in unit before
adding panels and covers. Securely fasten all panels and
covers.
3. Tighten service valve stem caps to 1/12
−
turn past finger
tight.
4. Leave Owner’s Manual with owner. Explain system opera-
tion and periodic maintenance requirements outlined in
manual.
5. Fill out Dealer Installation Checklist and place in customer
file.
TROUBLESHOOTING
If the compressor fails to operate with a cooling call, the table
below (Resistance table) can be used to verify if there is any
damage to the compressor windings causing system malfunction.
Table 3 – Winding Resistance
Winding
Winding resistance at 70
_
F +/- 20
_
F
(21.11
_
C +/- 11.11
_
C)
024
036
048
060
Start
(S-C)
1.64
1.54
1.86
1.63
Run
(R-C)
1.30
0.88
0.52
0.39
MAJOR COMPONENTS
2
−
Stage Compressor
The 2
−
stage compressor contains motor windings that provide
2
−
pole (3500 RPM) operation.
Compressor Internal Relief
The compressor is protected by an internal pressure relief (IPR)
which relieves discharge gas into compressor shell when
differential between suction and discharge pressures exceeds and
550
−
625 psi. The compressor is also protected by an internal
overload attached to motor windings.
Compressor Control Contactor
The contactor has a 24 volt coil and is controlled by Y input from
the thermostat
High and Low Pressure Switches
High and low pressure switches are provided in line with the Y
signal to the contactor for protection.
CARE AND MAINTENANCE
For continuing high performance and to minimize possible
equipment failure, periodic maintenance must be performed on this
equipment.
Frequency of maintenance may vary depending upon geographic
areas, such as coastal applications. See Users Manual for
information.
25HCB6