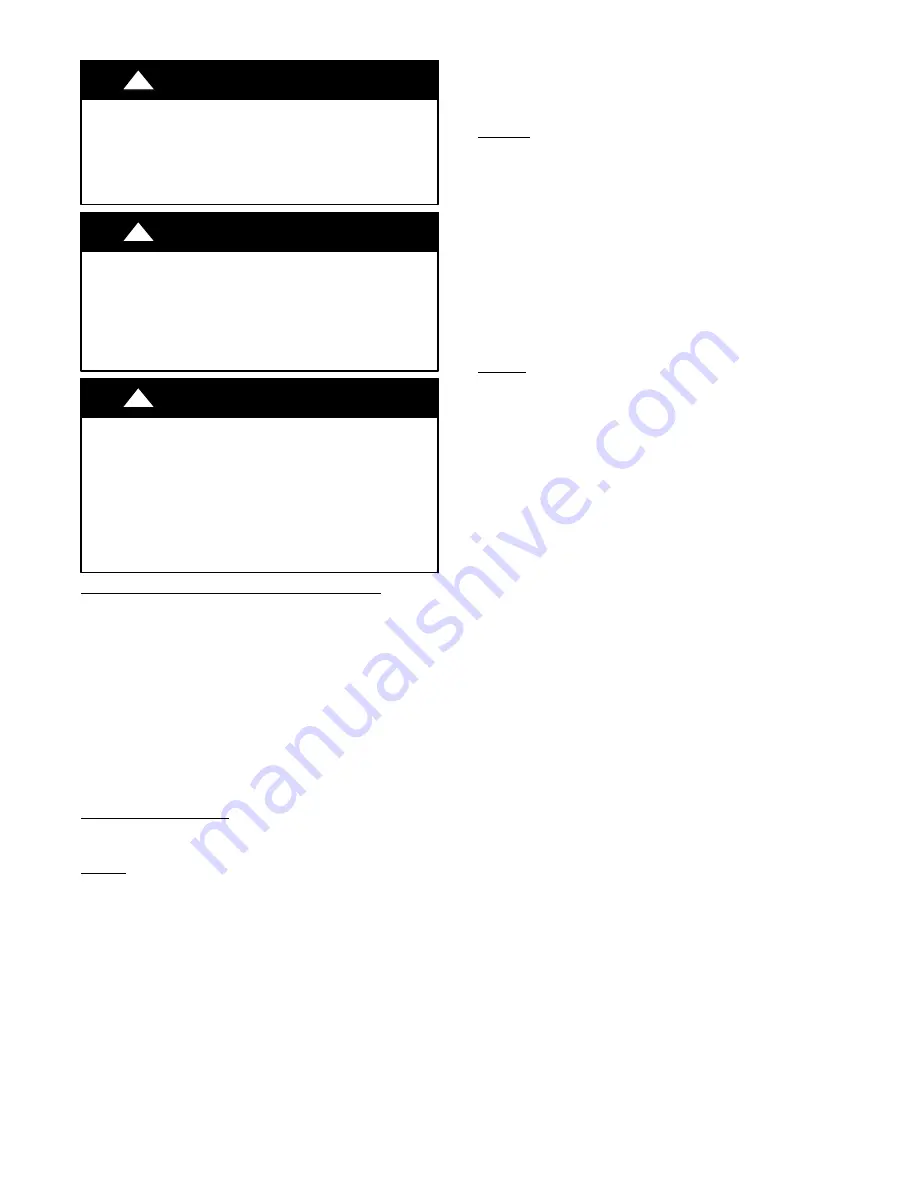
7
Start–Up
CAUTION
!
PERSONAL INJURY HAZARD
Failure to follow this caution may result in personal injury.
Wear safety glasses, protective clothing, and gloves when
handling refrigerant and observe the following:
S
Front seating service valves are equipped with Schrader valves.
CAUTION
!
ENVIRONMENTAL HAZARD
Failure to follow this caution may result in environmental
damage.
Federal regulations require that you do not vent refrigerant to
the atmosphere. Recover during system repair or final unit
disposal.
CAUTION
!
UNIT OPERATION AND SAFETY HAZARD
Failure to follow this caution may result in personal injury,
equipment damage or improper operation.
S
Do not overcharge system with refrigerant.
S
Do not operate unit in a vacuum or at negative pressure.
S
Do not disable low pressure switch in scroll compressor
applications.
S
Compressor dome temperatures may be hot.
Follow these steps to properly start up system:
1. After system is evacuated, fully open liquid and vapor ser-
vice valves.
2. Unit is shipped with valve stem(s) front seated (closed) and
caps installed. Replace stem caps after system is opened to
refrigerant flow (back seated). Replace caps finger–tight and
tighten with wrench an additional 1/12 turn.
3. Close electrical disconnects to energize system.
4. Set room thermostat at desired temperature. Be sure set
point is below indoor ambient temperature.
5. Set room thermostat to HEAT or COOL and fan control to
ON or AUTO mode, as desired. Operate unit for 15
minutes. Check system refrigerant charge.
Sequence of Operation
Turn on power to indoor and outdoor units. Transformer is
energized.
Cooling
On a call for cooling, thermostat makes circuits R–O and R–Y, and
R–G. Circuit R–O energizes reversing valve, switching it to
cooling position. Circuit R–Y energizes contactor, starting outdoor
fan motor and compressor circuit. R–G energizes indoor unit
blower relay, starting indoor blower motor on high speed.
When thermostat is satisfied, its contacts open, de–energizing
contactor and blower relay. Compressor and motors should stop.
NOTE
: If indoor unit is equipped with a time–delay relay circuit,
the indoor blower will run an additional 90 seconds to increase
system efficiency.
Heating
On a call for heating, thermostat makes circuits R–Y and R–G.
Circuit R–Y energizes contactor, starting outdoor fan motor and
compressor. Circuit R–G energizes indoor blower relay, starting
blower motor on high speed.
Should temperature continue to fall, R–W2 is made through
second–stage room thermostat. Circuit R–W2 energizes a relay,
bringing on first bank of supplemental electric heat and providing
electrical potential to second heater relay (if used). If outdoor
temperature falls below setting of outdoor thermostat (field
installed option), contacts close to complete circuit and bring on
second bank of supplemental electric heat.
When thermostat is satisfied, its contacts open, de–energizing
contactor and relay. All heaters and motors should stop.
Defrost
The defrost control is a time/temperature control which includes a
field selectable (quick–connects located at board edge) time period
between defrost cycles (30, 60, or 90 minutes), factory set to either
60 or 90 minutes.
The electronic defrost timer sequence is enabled when the T1 input
on the board is energized. The timer starts only when the defrost
thermostat is closed and the contactor is energized.
Defrost mode is identical to cooling mode except that outdoor fan
motor stops and second–stage heat is turned on to continue
warming conditioned spaces.
To initiate defrost, the defrost thermostat must be closed. This can
be accomplished as follows:
1. Turn off power to outdoor unit.
2. Disconnect outdoor fan motor lead from OF2 on control
board (see Fig. 12). Tape lead to prevent grounding.
3. Restart unit in heating mode, allowing frost to accumulate
on outdoor coil.
4. After a few minutes in heating mode, liquid line temperat-
ure should drop below closing point of defrost thermostat
(approximately 30
°
F/–1.11
°
C).
5. Short between speedup terminals with a flat–blade screw-
driver. This reduces the timing sequence to 1/25th of origin-
al time. (See Table 4.)
6. When you hear reversing valve change position, remove
screwdriver immediately; otherwise, control will terminate
normal 10–minute defrost cycle in approximately 2
seconds.
NOTE
: Length of defrost cycle is dependent upon length of time
it takes to remove screwdriver from test pins after reversing valve
has shifted.
7. Unit will remain in defrost for remainder of defrost cycle
time or until defrost thermostat reopens at approximately
65
°
F (18.33
°
C) coil temperature of liquid line.
8. Turn off power to outdoor unit and reconnect fan motor
lead to OF2 on control board.