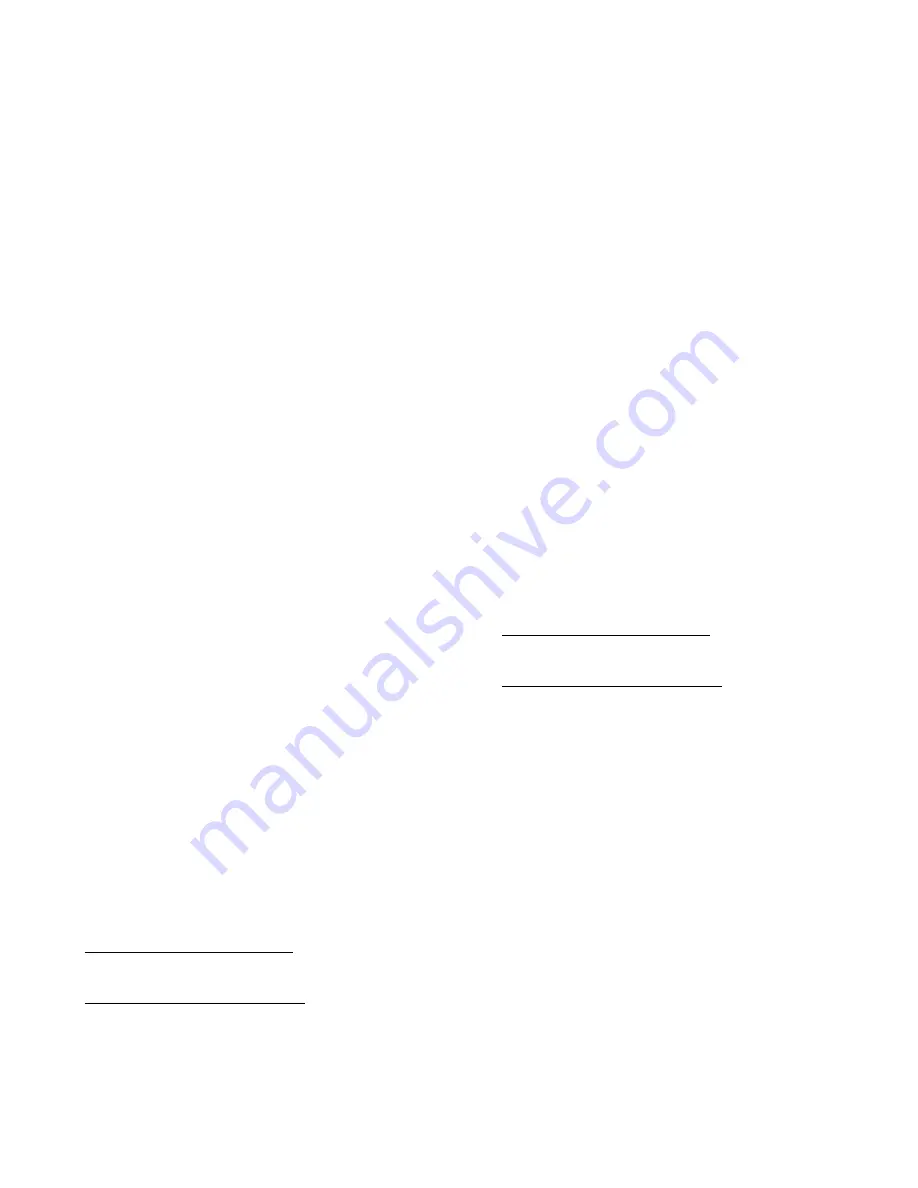
INSULATION AND PAINT
Insulation (If Required) —
Apply insulation as indi-
cated in the job data, after the chiller assembly and field pip-
ing have been completed. If the shipping vacuum or pres-
sure test indicate possible leakage, do not apply insulation
until the leak has been corrected. Protect insulation from weld
heat damage and weld splatter during installation. Recom-
mended areas for insulation include:
COLD SURFACES
• entering and leaving chilled water lines
• evaporator waterboxes and covers (be sure to allow for
easy cover removal)
• refrigerant pump casing and its inlet and outlet piping
• evaporator shell and tube sheets, including refrigerant sump
box
HOT SURFACES
• steam and condensate lines
• drain heat exchanger and piping
• generator steam chest. Be sure to allow for easy cover
removal.
• high-stage generator shell, tube sheets, and float chamber
• high-temperature heat exchanger and strong solution pip-
ing from high-stage generator
• hot refrigerant vapor inlet and hot refrigerant water outlet
on the low-stage generator and the vapor line from the high-
stage generator. Large chillers (models 080-150 and 080L-
150L) have 2 hot refrigerant vapor inlets and 2 hot refrig-
erant water outlets.
Final Paint Coat (If Required) —
Paint the chiller as
indicated in the job data after installation assembly, leak test-
ing, and insulation have been completed. Use specified paint,
making sure only high-temperature paint is applied to areas
with hot surfaces, as described above.
CONTROLS AND WIRING
The 16JT chiller has either Product Integrated Controls
(PIC) or electro-mechanical controls (electronic or pneu-
matic). Field wiring and pneumatic connections must be in-
stalled in accordance with job wiring diagrams and all ap-
plicable codes.
Two-Piece Chiller Connections —
Reconnect any
control wiring and conduit that had been disconnected at the
factory for shipping the chiller in 2 pieces.
Chillers With Electro-Mechanical Controls
CAPACITY CONTROL VALVE(S) —The controls can be
either electronic or pneumatic (Fig. 17). Refer to the job con-
trol diagrams and instructions for specific connections. The
chilled water temperature sensor and its wiring to the con-
trol panel are installed in the factory. Install wiring for the
valve positioning control between the valve operator and the
wiring terminals in the control panel.
Electronically Controlled Actuator — Also install wiring for
valve operator power between the valve operator and wiring
terminals in the control panel.
Pneumatically Controlled Actuator — Also install
1
⁄
4
-in.
(6 mm) plastic tubing between the valve operator and the
pneumatic supply air.
EXTERNAL WIRING — Install external wiring to the chiller
control panel according to job wiring diagrams and data. Check
available power supply and safety interlocks to be sure they
match the chiller equipment requirements, including:
• three-phase power supply for controls and chiller her-
metic pumps
• start and run interlocks for chilled water and cooling wa-
ter pumps and for cooling tower fan(s)
• remote chiller start/stop contacts, if used
• remote operating status and fault indication, if used.
SENSOR ELEMENTS — For all sensor elements not al-
ready installed on the chiller, uncoil the capillary tubing for
the thermoswitches and place the sensing element in the ad-
jacent temperature wells. Add heat conductive oil or com-
pound to the wells after checking and calibrating the follow-
ing controls at start-up:
• absorber solution temperature limit switch
• high-stage generator/high-temperature limit switch
• low chilled water temperature limit switch
• low refrigerant temperature limit switch or other tempera-
ture switches when used
• water pressure differential switch (normally installed in the
field). Since there is no bulb, the pressure is tapped to the
water piping.
Chillers with PIC Controls
CAPACITY CONTROL VALVE(S) — Refer to the job con-
trol diagrams and instructions for specific connections. The
chilled water temperature sensor and its wiring to the con-
trol panel are installed in the factory. Install wiring for the
valve positioning control between the valve operator and the
wiring terminals in the control panel. Wire the 4 to 20 mA
signal for the valve operator to terminal strip 1 (TB-1), ter-
minals 415 (+) and 416 (−). The 4 to 20 mA signal is in-
ternally powered.
Electronically Controlled Actuator — Also install wiring for
valve operator power between the valve operator and wiring
terminals in the control panel.
Pneumatically Controlled Actuator — Also install
1
⁄
4
-in.
(6 mm) plastic tubing between the valve operator and the
pneumatic supply air.
EXTERNAL WIRING — Install external wiring to chiller
control panel according to job wiring diagrams and data. Check
available power supply and safety interlocks to be sure they
match the chiller equipment requirements, including:
• three-phase power supply for controls and chiller her-
metic pumps
• start and run interlocks for chilled water and cooling wa-
ter pumps and for cooling tower fan(s)
• remote chiller start/stop contacts, if used
• remote operating status and fault indication, if used
• any CCN wiring as indicated on the job wiring diagrams.
SENSOR ELEMENTS — For all sensor elements not al-
ready installed on the chiller, uncoil the capillary tubing for
the thermoswitches and place the sensing element in the ad-
jacent temperature wells. Add heat conductive oil or com-
pound to the wells after checking and calibrating the follow-
ing controls at start-up:
• high-stage generator/high-temperature limit switch
• low chilled water temperature limit switch
• water pressure differential switch (normally installed in the
field). Since there is no bulb, the pressure is tapped to the
water piping.
11