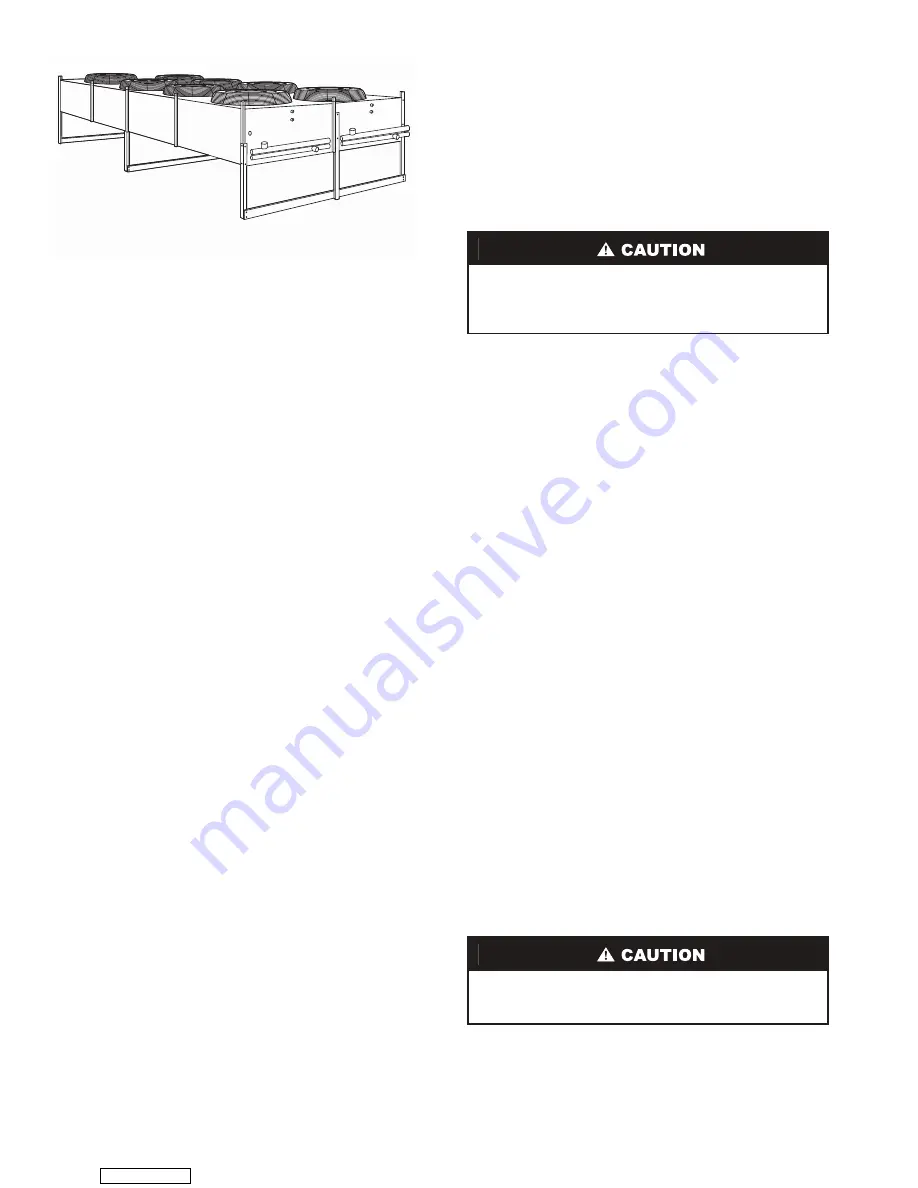
2
GENERAL
These units are remote air-cooled condensers for use with
vertical package units, liquid chilling packages, or other air-
cooled compressor and remote condenser units. Models are
available for either vertical or horizontal airflow. The 09AZ
units have been optimized for use with the 30HX remote pack-
age units. Refer to Fig. 2 for model number nomenclature.
Units are remote air-cooled condensers with direct drive
axial flow condenser fan. These units are available in nominal
heat rejection capacity from 90 to 200 tons. Inlet and discharge
are on opposite sides of the unit. Units may be mounted in any
area having unobstructed air circulation. Low silhouette
permits installation on varied ground, roof, or suspended
applications.
Each unit consists of direct-drive motor(s), propeller fan(s),
fan guards, motor mounts, condenser coil with integral sub-
cooling circuit, and electrical junction box. Factory options that
extend the capability and features of the unit are available.
Check space requirements, service clearances, floor
strength, location of piping, size of power supply, and airflow
clearances before installing. See Fig. 3A and 3B for unit di-
mensions and Tables 1A and 1B for unit operating weights. See
Tables 2A and 2B for corresponding chiller and condenser
sizes.
INSTALLATION
Step 1 — Complete Pre-Installation Checks —
Examine unit for damage incurred during shipment. File claim
immediately with transit company if damage is found. Check
the shipment for completeness. Verify that the nameplate elec-
trical requirements match the available power supply.
Step 2 — Rig and Place Unit
LOCATION — If roof installation is specified, make certain
that roof structure can support condenser weight. Refer to
Table 1.
Locate condenser where an adequate supply of inlet outdoor
air is available. Do not locate where the possibility of air recir-
culation exists, such as under a roof overhang. Locate in an
area free from airborne dirt or other foreign material that could
clog condenser units.
RIGGING — Leave the units in the carton or on the skid until
they are as close to the installation location as possible. The
method of rigging depends on the unit size. Never lift the unit
by the header or the return bends. Unit legs must be unbolted
and positioned while the unit is rigged.
The preferred method is with spreader bars from above the
unit. Lifting lugs are provided to aid in lifting the unit. Use
2-in. OD pipe and hooks in lifting eyes. Rig with 4 cables and
spreader bars. All panels must be in place when rigging. See
Table 3 and Fig. 4 for details concerning shipping weights, dis-
tance between lifting holes, center of gravity, and spreader bar
dimensions.
If overhead rigging is not possible, place unit on skid or pad
for rolling or dragging. When dragging, pull the pad. Do not
apply force to the unit. When in final position, raise from above
to lift unit off skid.
PLACING UNIT — The 09AZ units are designed for outdoor
applications. If the unit is mounted indoors, provisions must be
made to ensure that discharge air is not recirculated into the
unit. If the unit is ducted, the duct must not add more than
0.1 in. wg to the static pressure imposed on the fans.
Vertical units 09AZV should be located no closer than the
width of the unit to an obstruction such as a wall or another
unit. Keep the area around each unit clear to avoid restricting
the airflow to the unit. There must be 4 ft for service and for
unrestricted airflow on all sides of the unit and a minimum of
8 ft clear air space above units. For multiple units, allow 8 ft
separation between units for airflow and service.
MOUNTING UNIT — Units must be level to ensure proper
drainage of liquid refrigerant and oil. When units are installed
on a roof, they must be mounted on support beams that span
load walls. Ground mounted units should be installed on con-
crete pads of sufficient size to prevent grass and brush from
blocking the unit inlet. When unit is level and in proper loca-
tion, use mounting holes in legs for securing unit to supporting
structure. Fasteners for mounting unit must be field supplied. If
unit is to be mounted on vibration isolators, use mounting holes
in bottom of support legs as support points, and locate isolators
at those points.
Step 3 — Complete Refrigerant Piping —
Refer to
Fig. 5 for typical piping details.
GENERAL — All field leak and pressure testing should be in
accordance with local code requirements. If no local code ex-
ists, follow American National Standards Institute (ANSI),
American Society of Heating, Refrigeration and Air Condition-
ing Engineers (ASHRAE) Safety Standard 15, latest revision.
For leak testing procedures, refer to the Carrier Refrigerant
Service Techniques manual. Perform Phos-copper brazing on
all field-made connections while protecting adjacent points
from heat.
COIL CIRCUITING — The 09AZV091-181 single circuit
models require field assembly of gas and liquid manifolds (see
Fig. 6). Dual circuit units require no field assembly and piping.
Fig. 1 — Typical 09AZ102 Unit
To avoid damage to units, do not forklift them unless they
are attached to skids designed for forklifting. Forklift
trucks used to lift units on skids must have forks a mini-
mum of 48 in. long.
To prevent unit damage, never connect two separate com-
pressor-evaporator circuits together on the same condenser
circuit.
Downloaded from