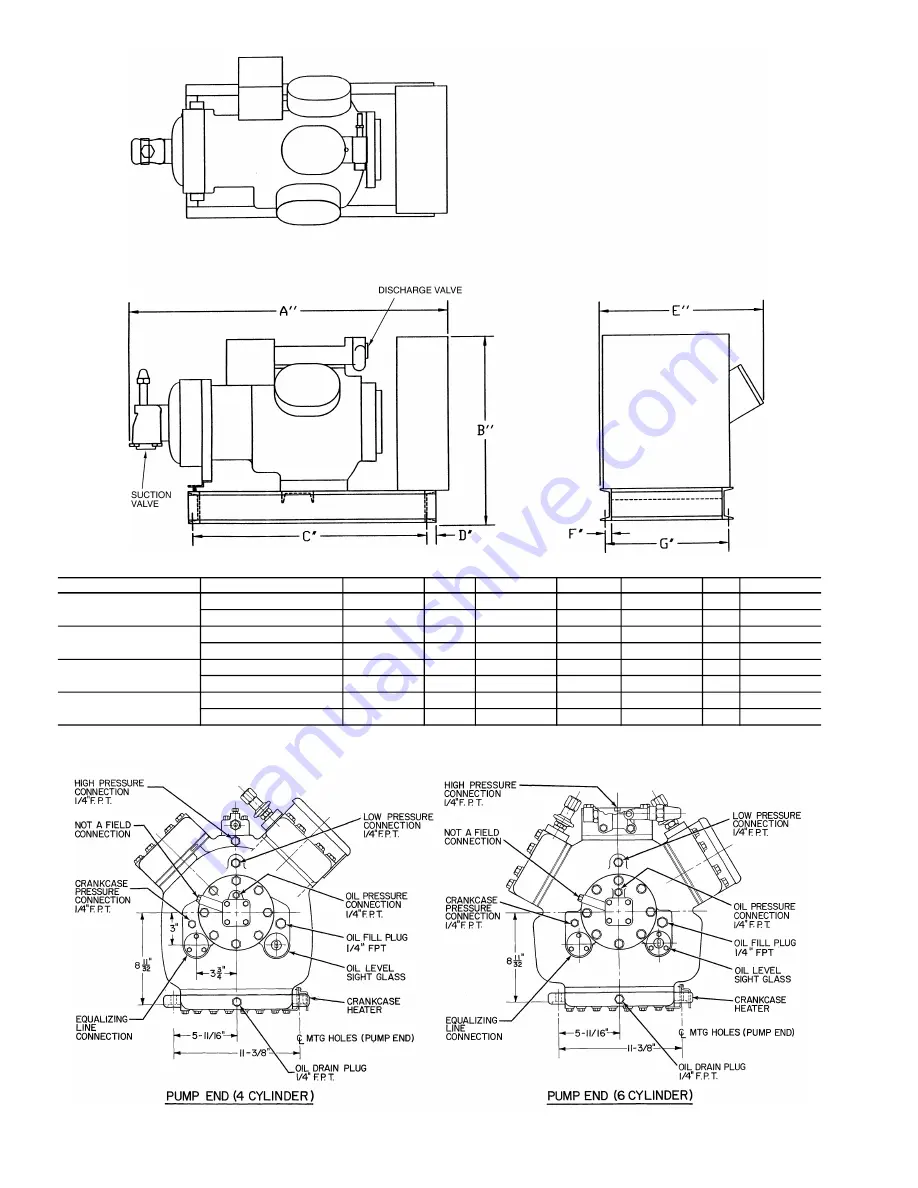
4
DIMENSIONS (in.)
06E UNIT
VOLTAGE
A
B
C
D
E
F
G
V022
208/230
48
1
/
4
35
36
7
/
8
1
1
/
2
27
1
/
2
1
19
1
/
2
460,575
48
1
/
4
29
36
7
/
8
1
1
/
2
26
1
19
1
/
2
W027
208/230
50
1
/
4
35
36
7
/
8
1
1
/
2
27
1
/
2
1
19
1
/
2
460,575
50
1
/
4
29
36
7
/
8
1
1
/
2
26
1
19
1
/
2
W033
208/230
50
1
/
4
35
36
7
/
8
1
1
/
2
27
1
/
2
1
19
1
/
2
460,575
50
1
/
4
29
36
7
/
8
1
1
/
2
26
1
19
1
/
2
W044
208/230
50
1
/
4
35
36
7
/
8
1
1
/
2
27
1
/
2
1
19
1
/
2
460,575
50
1
/
4
35
36
7
/
8
1
1
/
2
27
1
/
2
1
19
1
/
2
Fig. 3 — 06E Hermetic Compressor Units
Fig. 4 — 06E Compressors
NOTES:
1. For standard service practices, such as troubleshooting
and refrigerant charging, allow a minimum 2
-6
clearance
around the unit.
2. For compressor removal, allow a minimum 3
wide access
aisle to and from the unit.
3. Local codes or jurisdiction may prevail for unit clearances.
Summary of Contents for 05FY/HY Series
Page 19: ......