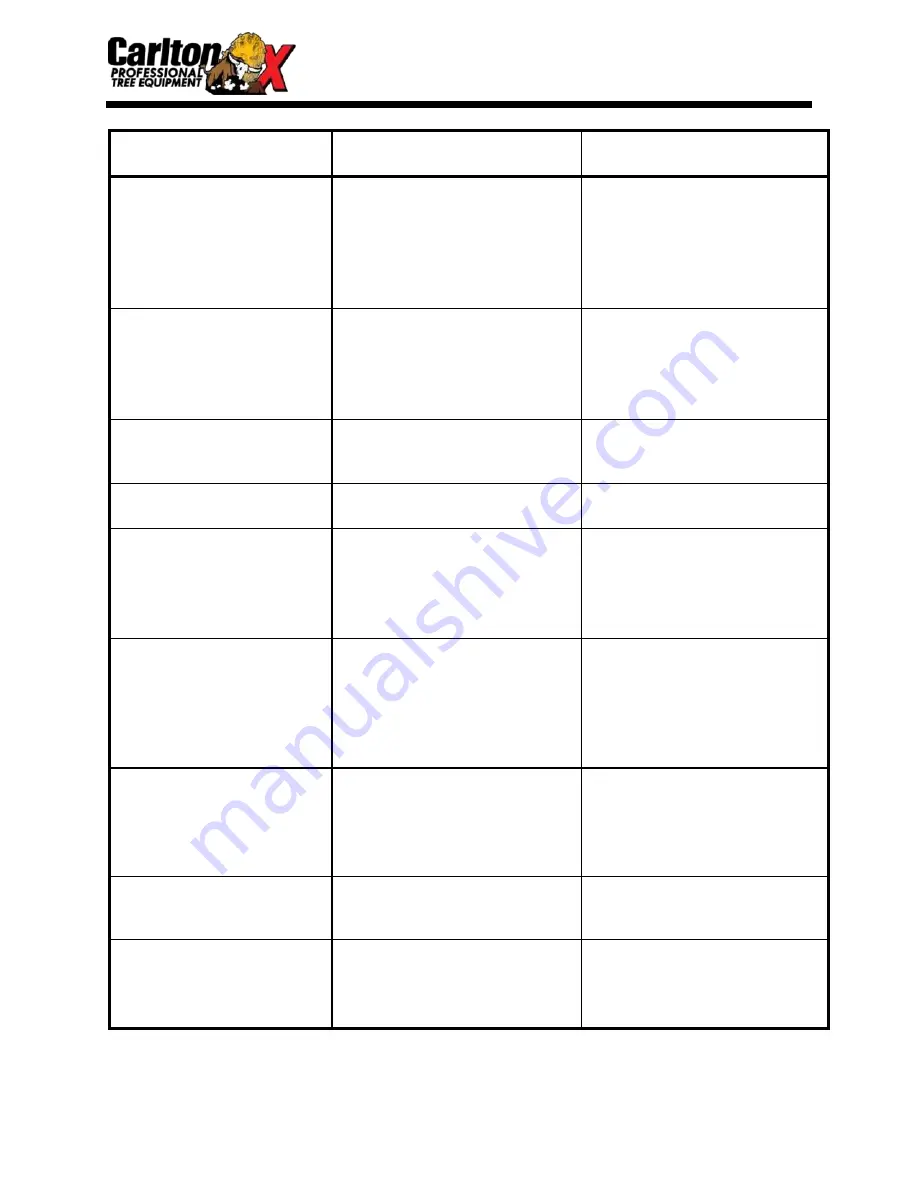
SP6016 TROUBLSHOOTING GUIDE
COMPLAINT
CAUSE
CORRECTION
Engine will not start.
(See Engine Manufacturers’
Manual for further
information.)
•
On/Off switch on machine
control panel is in off position.
•
Loose ground wire.
•
Loose hot wire.
•
Dead battery.
•
Move switch to the
ON
position and follow normal
startup procedure.
•
Clean and tighten.
•
Clean and tighten.
•
Recharge or replace.
Hydraulic system loss of
power.
•
Low oil.
•
Valve set too low.
•
Splined pump coupling worn.
•
Bad cylinder.
•
Bad Pump.
•
Refill with correct oil.
•
Adjust relief valve.
•
Remove pump coupler.
•
Replace cylinder packing.
•
Replace Pump.
Cutter Head Swing cylinder
loss of power.
•
Swing Speed adjustment valve
turned wide open.
•
Turn valve clockwise to close
bypass. Re-
adjust for “no
bounce” cutting.
Belt Squeal.
•
Belt tension too loose.
•
Belt out of alignment.
•
Tighten.
•
Align Pulleys.
Belt jumping off.
•
Engaging or disengaging belt
at high engine RPM.
•
Belt keeper too far from belt.
•
Belt worn.
•
Pulley worn.
•
Only engage or disengage
belts at low engine speeds.
•
Adjust keeper closer to belt.
•
Replace belt.
•
Replace pulley.
Cutter wheel vibration.
•
Tooth missing.
•
Pocket out of balance.
•
Improper tooth arrangement.
•
Replace missing teeth.
•
Always replace pockets in
pairs across from each other.
•
Install correctly with like
pairs of teeth directly across
from each other.
Standard Cutter wheel
throwing teeth.
•
Bad pocket.
•
Dirt in pocket.
•
Cutter wheel worn where
tooth sits.
•
Replace pocket.
•
Clean pocket and replace
missing teeth.
•
Replace cutter wheel.
Standard Cutter wheel
breaking teeth.
•
Teeth set too far out of pocket.
•
Use gauge to set teeth
correctly.
Razor Cutter wheel
throwing teeth.
•
Bad pocket.
•
Tooth Nut not torqued
properly.
•
•
Replace Pocket.
•
Tighten nut with torque
wrench. (150 - 170 ft/lbs.)
35
Summary of Contents for SP6016 Series
Page 2: ...BLANK SHEET ...
Page 4: ...SP6016 SAFETY ALERT ...
Page 5: ...SP6016 SAFETY ALERT OPERATE MACHINE FROM 25 FEET AWAY KEEP SPECTATORS AWAY ...
Page 6: ...SP6016 SAFETY ALERT ...
Page 7: ...SP6016 SAFETY ALERT ...
Page 10: ...BLANK SHEET ...
Page 12: ...BLANK SHEET ...
Page 47: ...SP6016 MACHINE MAINTENANCE 7 6 34 ...
Page 69: ...1 RUBBER TRACK OPERATIONS MANUAL ...
Page 70: ...2 ...
Page 83: ...15 2 6 LUBRICATION CHART ...
Page 90: ...22 APPENDIX A BOLT TORQUE TABLE ...
Page 95: ...Appendix A ...
Page 96: ...BLANK SHEET ...