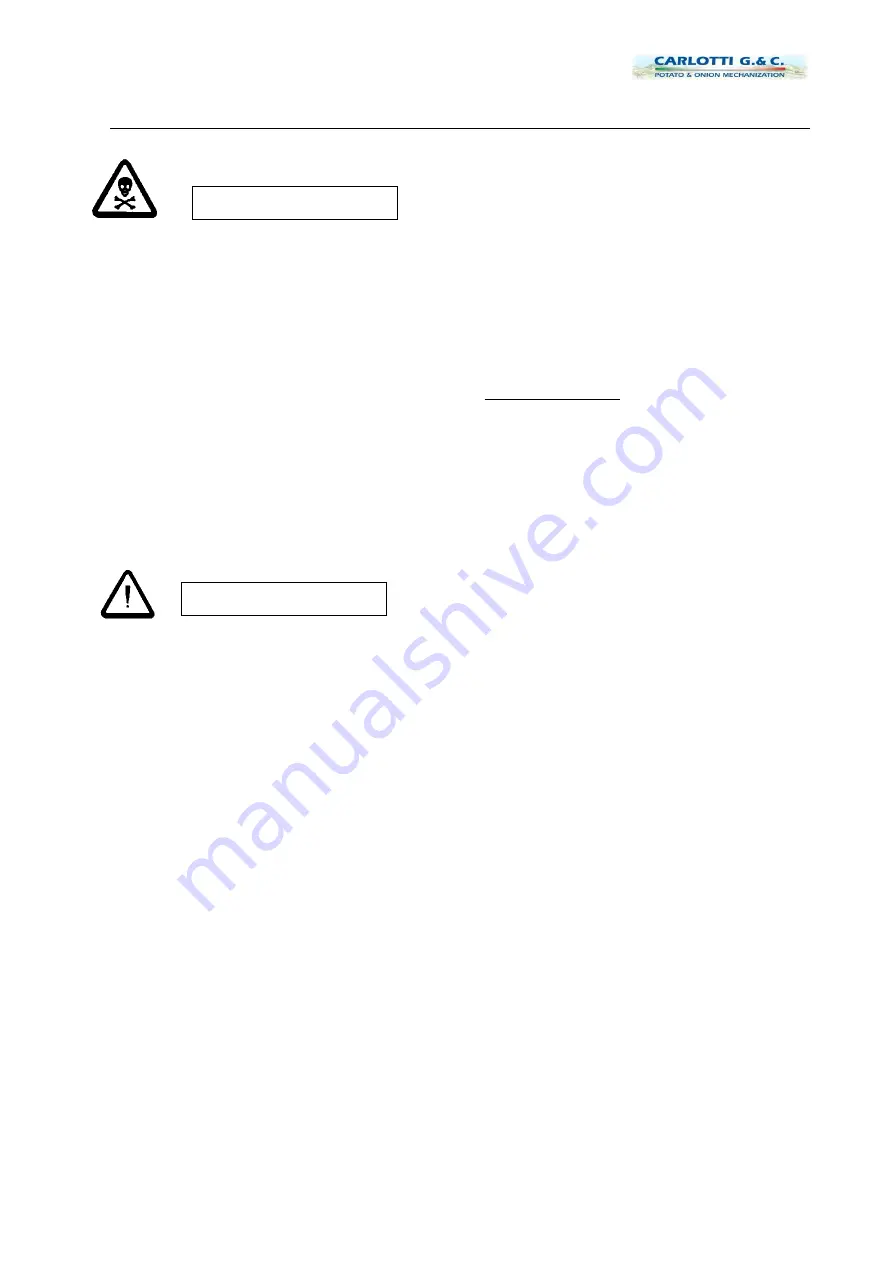
5.
ORDINARY MAINTENANCE
All maintenance, adjustment, cleaning, lubrication, greasing and repair operations must be
carried out with the machine completely detached from the tractor and resting on the support
foot on level ground. Do not perform this operation on slopes or in other places that do not
ensure complete stability of the machine
5.1 Daily maintenance
Every day, after using the SPRING 750/35 machine, the qualified technician must:
-
Clean it from dirt, dust and leaves.
-
Perform a general service of the machine paying particular attention to the oil level (in the tank in
the gearbox and in and top up if necessary.
-
Replace or repair damaged items.
5.2 Lubrication
•
Always read the warnings and precautions indicated on the lubricant packaging.
•
Always use gloves for hand protection.
•
Before lubricating, carefully clean the grease nipples to prevent sludge, dust or other foreign objects
from mixing with grease, decreasing or even cancelling the lubrication effect.
•
Avoid any contact with the skin.
•
Wash hands thoroughly after use.
For lubrication use the recommended products listed below:
- Hydraulic oil
ISO 46
to top up the tank
- Gearbox oil
80W90
to top up the gear box
- Grease GRIS 30
for supports/rollers/... as indicated by the appropriate graphic sign (see symbols
table paragraph 1.2)
5.3
Changing the oil/topping up
-
Make changes only inside the workshop, if any, or in specifically designated places. In any case, the
flooring should be waterproof.
-
Replacement of the used oil or the top-up operations must be carried out under conditions of
maximum safety and hygiene to avoid a situation whereby approximate operations or unsuitable
technical means produce spills on the ground and in the water.
-
The used oil must be stored, before being transferred to the company responsible for collection, in
suitable containers to store it in suitable conditions, eliminating the risks of breakage and spillage.
DANGER
ATTENTION