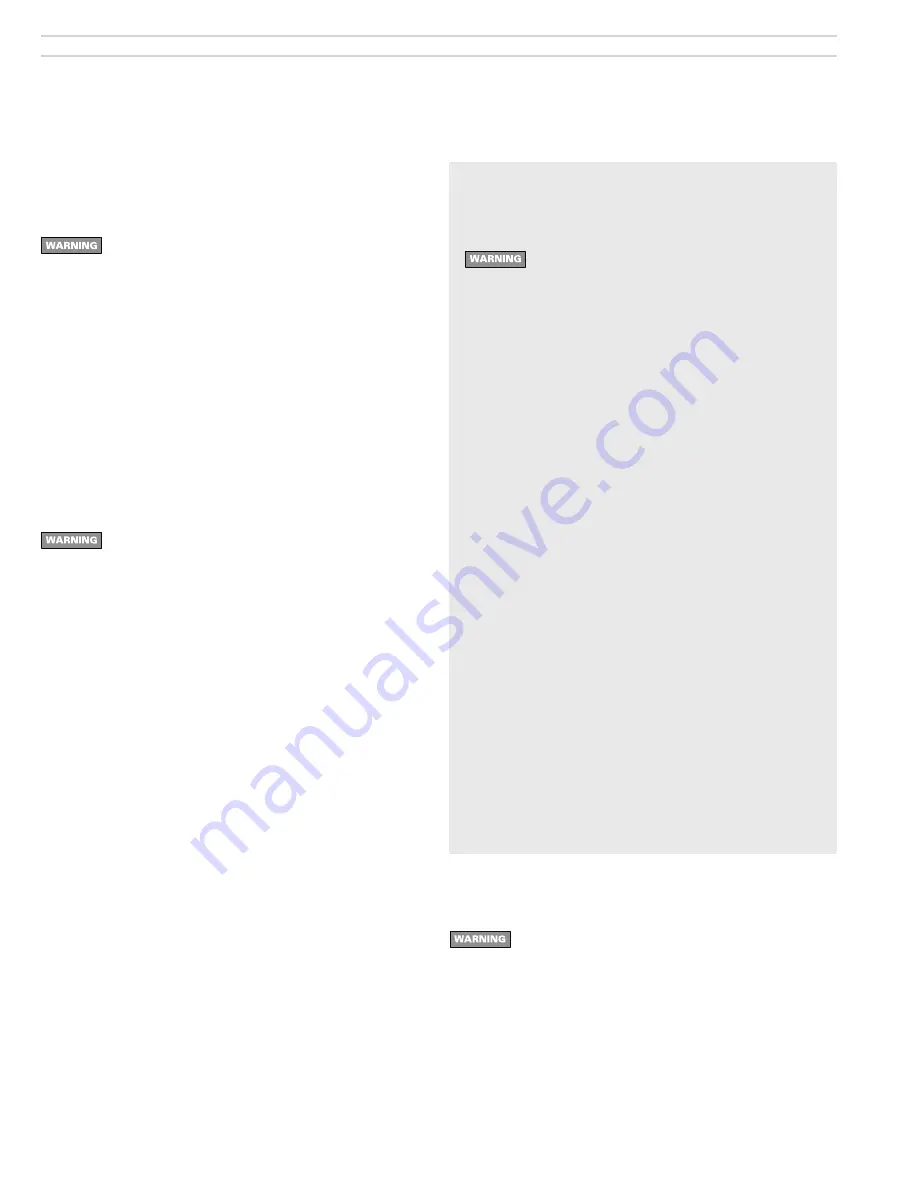
Model 201GAS burner — Instruction manual
Carlin part number MN201GAS Rev. 03/14/11
– 6 –
Where appliance instructions differ from this manual, follow the appliance instructions.
Verify clearances
• Verify that the burner/appliance will maintain all clearances to combus
-
tible walls or floor and all clearances required for service/maintenance as
required in the appliance manual and applicable codes.
Prepare the appliance
Burner input
: Install a gas burner sized for the normal input
rating of the appliance. Do not install a burner with a higher
firing rate than the appliance rating. Do not install a burner
with a firing rate more than 10% lower than the appliance
rating. The appliance and vent system could be damaged
due to condensation.
Clean the appliance
: Clean the appliance thoroughly and
seal all joints. Test all electrical components and verify the
relief valve works (boilers only).
Verify combustion chamber dimensions
comply with the
minimum dimensions shown in Figure 3, page 7. Install or re-
place chamber liner if required by the appliance manufacturer.
The burner must not extend into the combustion chamber. The
end of the burner air tube must be within ¼” of the inside
face of the chamber. If the space around the burner air tube
is more than ¼”, wrap the burner air tube with minimum
2300 °F – rated ceramic fiber blanket to seal off the gap.
Repair or replace damaged appliance components
.
Inspect the appliance thoroughly. Follow appliance manufac-
turer’s guidelines for repair or replacement of any component
found defective.
When cleaning the appliance or working with
ceramic fiber refrac-
tories or fiberglass insulation
, see
WARNING
on this page.
Failure to comply with the above could result in severe per-
sonal injury, death or substantial property damage.
Prepare appliance for burner mounting
The universal flange supplied with 201GAS burners is
intended only for firing chambers with negative overfire pres-
sure. For pressurized firing, you must obtain a burner with a
welded flange, designed for use with the appliance. You can
also use the optional forced draft flange. Failure to comply
could result in severe personal injury, death or substantial
property damage.
See page 19 for required dimensions and bolt locations.
1. Prepare site • prepare burner • mount burner
(continued)
Prepare installation site
Verify combustion/ventilation air openings
(continued)
When sizing air openings for combustion and ventilation,
include air required for exhaust fans and other appliances,
such as clothes driers, that require air for operation.
Check appliance manual and applicable codes for required sizing of com-
bustion and ventilation air openings.
• Verify that openings are unobstructed.
• Verify that appliance space and air source spaces are free of:
– Gasoline or other flammable liquids or vapors.
– Combustible materials.
– Air contaminants, such as laundry products, paint, thinner, varnish,
etc.
• Confirm with user that the area will be kept free of these materials at all
times.
Ceramic fiber or
Fiberglass insulation
Ceramic fiber materials, such as chamber liners, may
contain carcinogenic particles (chrystobalites) after
exposure to heat. Airborne particles from fiberglass or
ceramic fiber components have been listed as poten-
tially carcinogenic by the State of California. Take the
following precautions when removing, replacing and
handling these items.
Avoid breathing dust and avoid contact with skin or
eyes.
Wear long-sleeved, loose-fitting clothing, gloves
and eye protection. Use a NIOSH N95 certified respira
-
tor. This respirator meets requirements for protection
from chrystobalites. Actual job requirements or NIOSH
regulations may require other or additional protection.
For information, refer to the NIOSH website, http://www.
cdc.gov/niosh/homepage.html.
Ceramic fiber removal
: To prevent airborne dust, thor-
oughly wet ceramic fiber with water before handling.
Place ceramic fiber materials in a plastic bag and seal
to dispose.
Avoid blowing, tearing, sawing or spraying
fiberglass
or ceramic fiber materials. If such operations are neces-
sary, wear extra protection to prevent breathing dust.
Wash work clothes separately from other laundry
.
Rinse clothes washer thoroughly afterwards to prevent
contamination of other clothing.
NIOSH First aid procedures
:
Eye exposure — irrigate immediately
Breathing — fresh air.