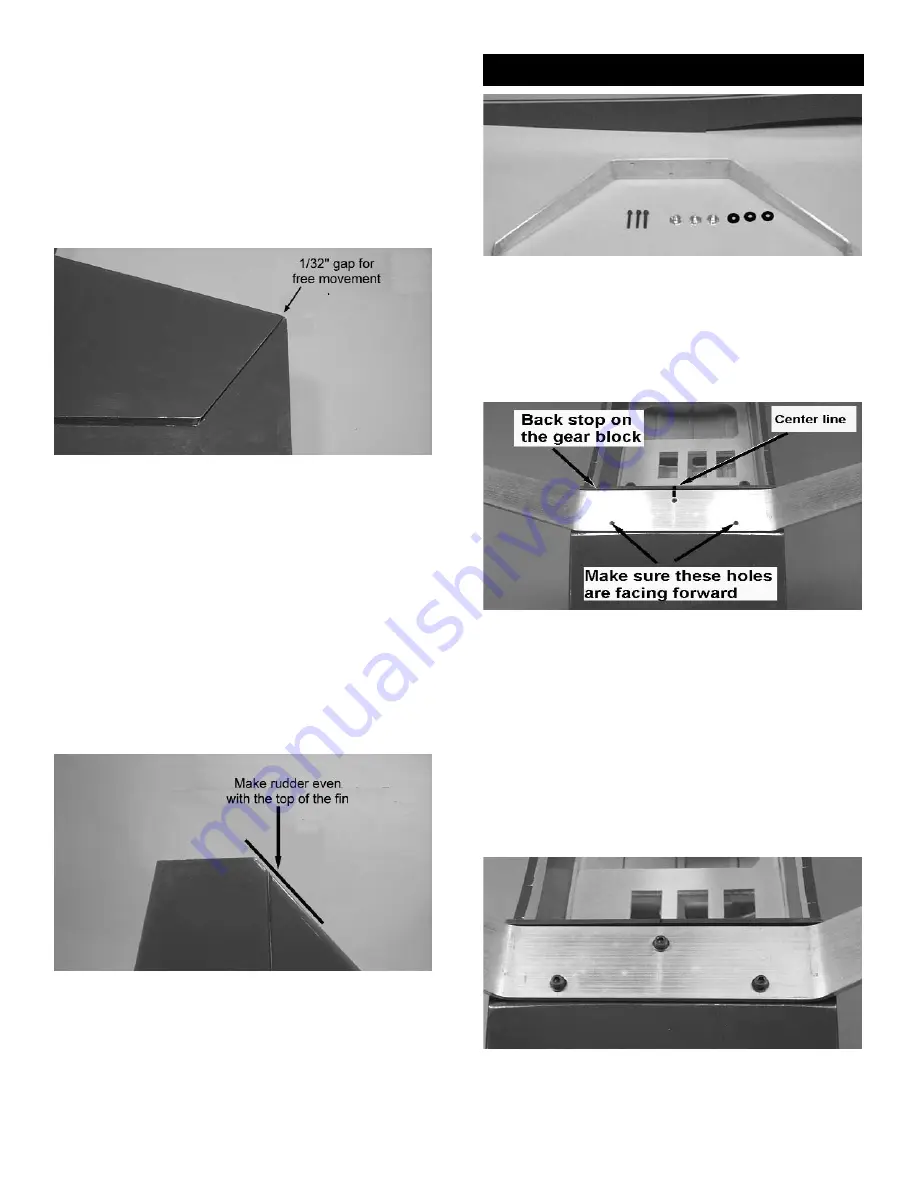
Landing Gear Installation
1.
Collect the following items:
(1) Landing gear
(3) 6-32 x 3/4” socket head screws
(3) 6-32 blind nuts
(3) #6 washers
(1) Fuselage
2.
Place the main gear on the bottom of the
fuselage, as shown.
Locate the center of the fuselage and mark
it. Then mark the center of the gear and line
up both center marks.
3.
Move the gear back until it touches the stop on the
back of the gear block. Then mark the hole loca-
tions and drill a 5/32” hole at each location.
4.
With the screws and the washers through
the gear, pull the blind nuts up tight inside
the fuselage.
2.
Take three hinges and, as with the aileron
hinge installation, insert the hinge into the
elevator, using straight pins to ensure the
hinge stays centered between the stabilizer
and the elevator.
Slide the exposed side of the hinge into the
slots in the stab until the pins touch both the
stab and the elevator.
3.
Holding the elevator and stab together, place
a straight pin between the stab and the ele-
vator, at the elevator tip. This pin will create
a 1/32” gap between the elevator and the
stab.
Remove the pins in each hinge and, keeping
the elevator/stab assembly in position, apply
3 or 4 drops of thin CA to each hinge, on
both the top and bottom sides of the stab.
Allow ten minutes for the CA to cure before
flexing the elevator. Then install the second
elevator.
4.
When the elevators have cured, install the
hinges and mount the rudder, using the
same techniques used for the other hinged
surfaces.
NOTE:
Before gluing, make sure the top of the rud-
der is even with the top of the fin.
13
Summary of Contents for ULTIMATE
Page 31: ......