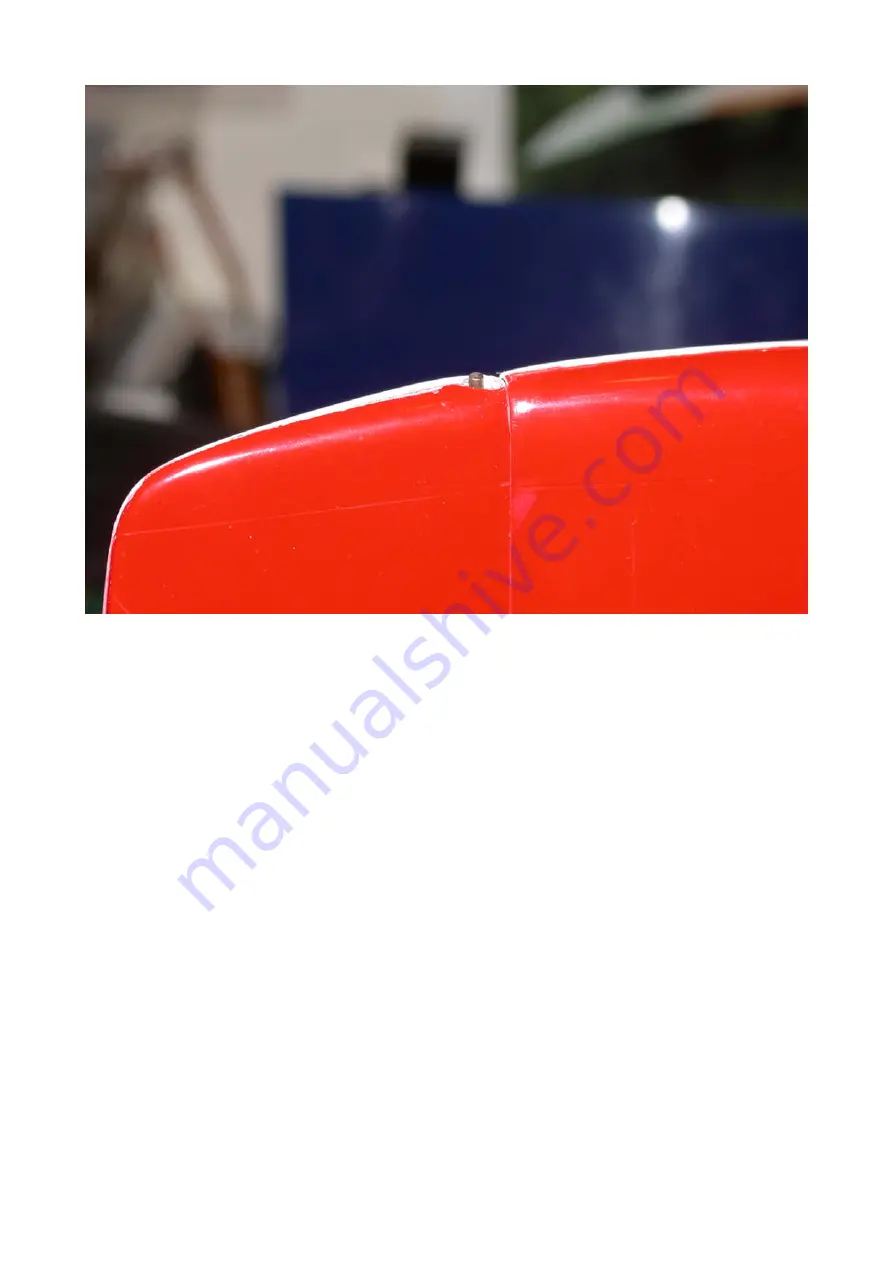
Composite ARF Tutor T-114 manual – [email protected]
19
Rudder .
Very little work is needed to complete the
rudder, but it should be completed early as the
tail pipe cannot be installed until after the rear
end is finished.
The factory cut hinge slots may require a
small amount of work to allow full and free
movement. The angled design of the rudder may
require the hinge slots lower edge chamfering
slightly to allow easy installation over the
factory fitted hinge lugs in the fin post. The
rudder is hinged using a 4mm brass tube, which
is fixed with a simple dab of glue on the top
face.
The rudder servo is fitted in the base of the fin
in a factory installed plate. A removable hatch
is located in the lower fuselage skin to allow
easy fitting of the screws. The rudder servo arm
should be cut to 28mm centres. The servo arm
length is critical to provide perfect geometry
with the factory fitted rudder horns. Screw the
rudder servo in position with the spline towards
the front using 2.9 x 13 screws. The rudder
servo and elevator servo extension leads are
passed though the holes bored in the fin former.
Add heatshrink tube or tape to protect the wires.
The Elevator extension leads will need to be
approx 1.5m long and the rudder lead around
1.3m. These are best custom made either by
shortening stock 1.8m leads or having leads
made. Protect the leads with the aluminium
tape provided.
Make the pull-pull linkage from the supplied
2mm pushrods. Fit the 2mm ball links to
threaded end before passing the linkage though
the factory slots. Mark the exact pushrod length
before cutting and soldering the clevis ends to
the non threaded end. The ball links are screwed
between the rudder horns with M2 x20 screws
and nuts.
Photo 17: Hinge wire.
Summary of Contents for CL-41 Tutor
Page 1: ...CL 41 Tutor www carf models com...
Page 4: ...Composite ARF Tutor T 114 manual techsupport composite arf com 2...
Page 8: ...Composite ARF Tutor T 114 manual techsupport composite arf com 6 Photo 2 Undercarriage legs...
Page 37: ...Composite ARF Tutor T 114 manual techsupport composite arf com 35 Assembled Assembled...
Page 38: ...Composite ARF Tutor T 114 manual techsupport composite arf com 36 Tail...
Page 40: ...Composite ARF Tutor T 114 manual techsupport composite arf com 38 In flight Cockpit...
Page 41: ...Composite ARF Tutor T 114 manual techsupport composite arf com 39 Underside in flight...
Page 42: ...Composite ARF Tutor T 114 manual techsupport composite arf com 40...
Page 43: ...Composite ARF Tutor T 114 manual techsupport composite arf com 41...
Page 44: ......