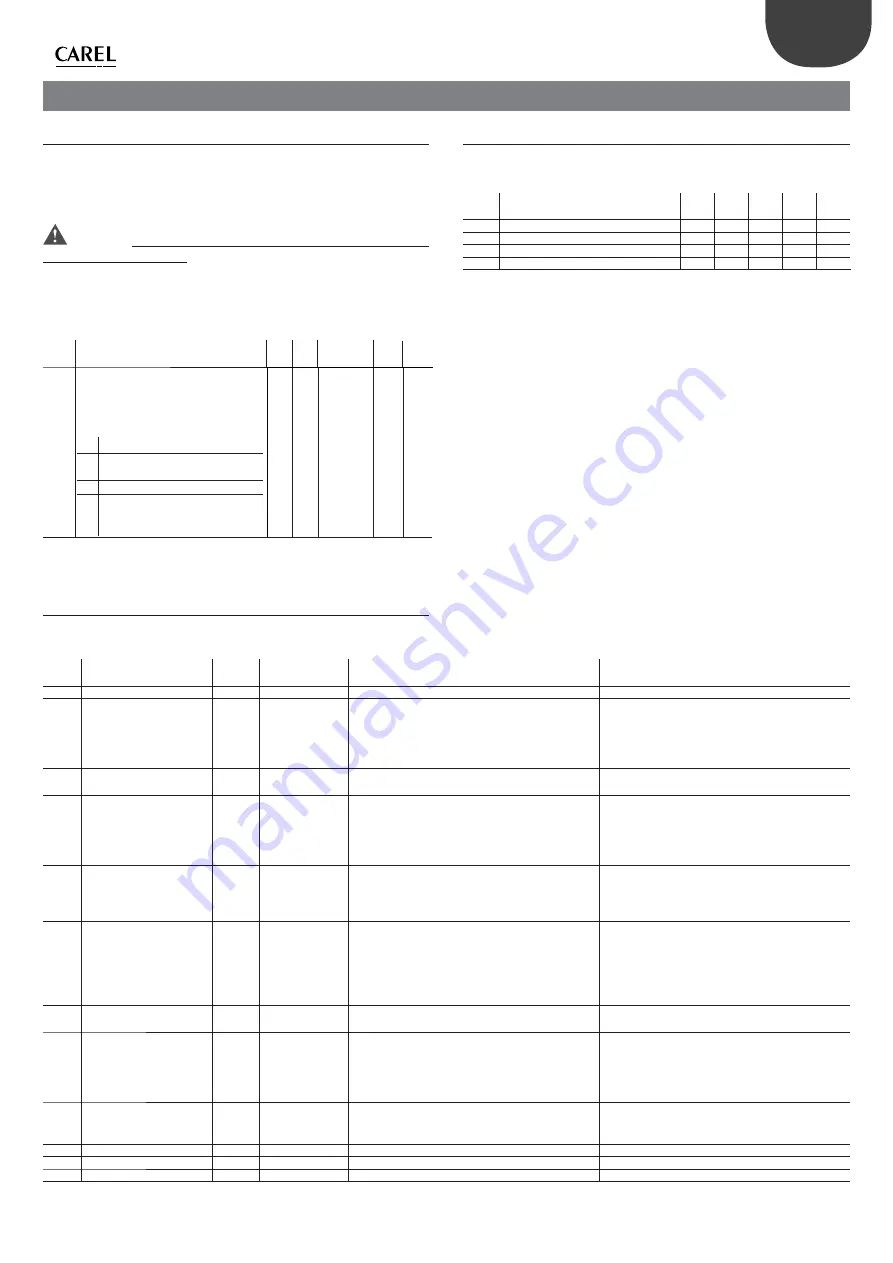
ENG
“Power+” +0300050EN - rel. 2.3 - 08.06.2012
31
8. ALARMS
8.1 Types of alarm
There are two types of alarm:
•
drive malfunctioning alarms;
•
motor malfunctioning alarms.
Among the status variables it is possible to check the presence of Modbus®
communication alarms.
Important:
All alarms stop the motor and must be restored using
the alarm reset command
:
Pr.101 = 1
followed by the command:
Pr.101 = 0
to resume the initial state.
Mod.
add.
Description
Def Min
Max
U.M. R/W
101 Reset (3 bit parameter)
The particular reset comand is executed
when the related bit changes from 0 to
1. After that the bit has to be cleared to
0 again.
bit meaning
0
alarms reset and updating of
communication parameters
1
parameters reset at default values
2
reset fl ag check drive switch on
and switch off (see speed register,
bit2)
0
0
allowable
values:
1, 2 ,4
-
R/W
Tab. 8.a
8.2 Alarms
log
The most recent 4 alarms are memorised in a FIFO type alarms queue. The
last alarm memorised is visible in the Alarm 1 status variable.
Mod.
add.
Description
Def
Min
Max
U.M.
R/W
137
Alarm 1
-
-
-
-
R
138
Alarm 2
-
-
-
-
R
139
Alarm 3
-
-
-
-
R
140
Alarm 4
-
-
-
-
R
Tab. 8.b
8.3 Alarms
table
The alarm code is given in the Alarm 1...4 parameters and in the alarm code
parameter (Modbus®=105)
Alarm
code
Description
Relay
alarm
Reset
Possible cause
Solutions
0
No alarm
-
-
-
-
1
Overcurrent
(*)
reset command The drive has detected a current supplied that is too
high due to:
- sudden strong load increase;
- acceleration that is too high;
- wrong parameters values or inadequate motor.
Check the load, the dimension of the motor and
the cables. Decrease acceleration. Check the motor
parameters..
2
Motor overload
(*)
reset command The current supplied has exceeded the rated current
over the maximum time accepted
3
Overvoltage
(*)
reset command The DC voltage of the intermediate circuit has
exceeded the limits envisioned due to:
- deceleration that is too high;
- high over-voltage peaks on the power supply
network.
Decrease deceleration.
4
Undervoltage
(*)
reset command The DC voltage of the intermediate circuit is below
the limits envisioned due to:
- insuffi
cient power supply voltage;
- fault inside the drive.
In the event of temporary cut-off of the power
supply, reset the alarm and re-start the drive. Check
the power supply voltage.
5
Drive overtemperature
(*)
reset command The temperature inside the drive has exceeded the
maximum level allowed.
Check that the quantity and fl ow of cooling air are
regular. Check that there is not dust in the heat sink.
Check the environment temperature. Ensure that
the switching frequency is not too high with respect
to the environment temperature and the motor
load.
6
Drive undertemperature
(*)
reset command The temperature inside the drive has exceeded the
minimum level allowed.
7
Overcurrent HW
(*)
reset command The drive has detected an istantaneous current
supplied that is too high due to:
- sudden strong load increase;
- motor cables short circuit;
- wrong parameters values or inadequate motor.
Check the load, the dimension of the motor and the
cables. Check the motor parameters.
8
Motor overtemperature
(*)
reset command The temperature detected by the PTC thermistor
corresponds to a resistance > 2600 ohm.
Reduce the motor load.
Check motor cooling.
9
IGBT module error
(*)
reset command Internal fault
Call for assistance
10
CPU error
(*)
reset command Loss of data in memory
Call for assistance
11
Parameter default
(*)
reset command Execution of reset parameter default command
Summary of Contents for Power+
Page 2: ......
Page 4: ......
Page 6: ...ENG Power 0300050EN rel 2 3 08 06 2012 6 ...
Page 35: ......