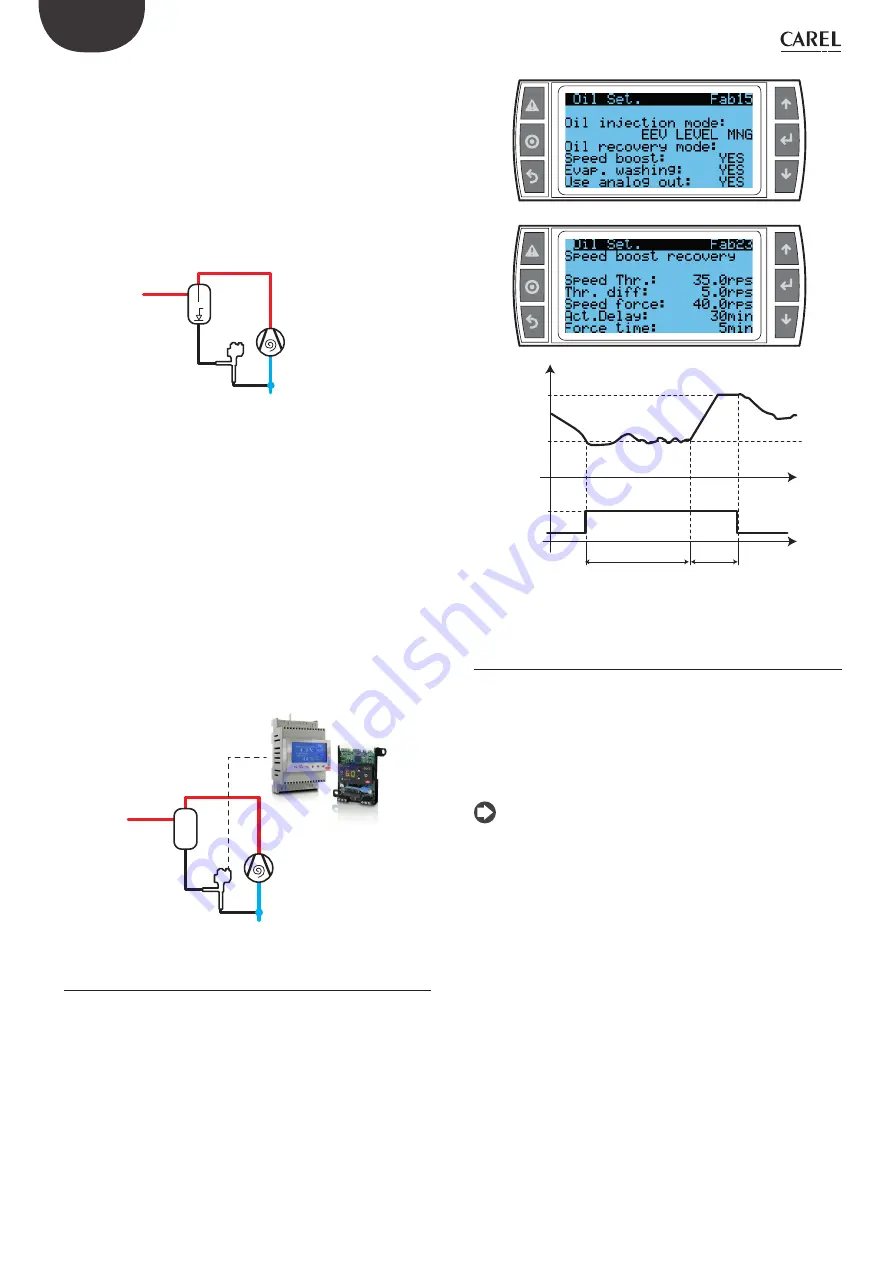
30
ENG
Hecu
C
O
2
+0300085EN rel. 2.2 - 07.05.2019
Electronic expansion valve (EEV LEVEL MNG)
This solution involves a CAREL expansion valve. The valve opening is
calibrated based on normal system operating conditions. This solution is
very effi
cient from an energy viewpoint, as it injects the exact quantity of
oil needed by the compressor. In order to use this function, an advanced
oil separator needs to be installed, featuring a level sensor that defi nes
three states via two digital inputs, confi gurable on
screens Faa55, Faa56
.
An advanced algorithm calculates valve opening based on the time that
elapses between the various states, comparing this against the previous
measurements. The objective is to replicate the oil level inside the
compressor by measuring the amount in the separator and keeping this
level stable over time.
3
advanced
oil separator
(double oil level)
EEV valve
BLDC
compressor
V
Fig. 6.q
On
screen Fab20
, two preventive thresholds can be set for the high and
low oil level (Emergency HL and LL). If the oil remains at this level for
the set time, the valve will open to the maximum (HL) or minimum (LL),
moving at 1 step/sec.
Electronic expansion valve controlled by external driver (EEV
COMP SPEED)
This solution features an expansion valve driven by an external driver
(EVDevo, EVD mini), confi gured as a positioner that receives the 0...10 V
control signal from the Hecu unit.
This is exploited when integrated drivers for the oil valve cannot be used
on Hecu CO2 as they are reserved for transcritical valves. Valve opening
is calibrated based on the BLDC compressor operating conditions (MT
or LT, not parallel), adjusted proportionally based on compressor speed.
A standard oil separator can be installed to exploit this function.
The parameters can be confi gured from screens Bad14 for assigning the
analogue output, and Fab15 to enablòe the function.
standard
oil separator
EEV valve
BLDC
compressor
V
Fig. 6.r
O
il speed boost
This function boosts the return of oil by operating the compressor at
a fi xed speed for a set time, thus recovering the oil spread along the
refrigerant circuit.
This override function is activated if the following conditions are true, see
screens Fab15, Fab23
:
•
Speed boost: YES
•
Compressor speed < minimum threshold
•
The previous conditions remain for a set time
Act. Delay
Force time
t
t
rps
Speed Force
Comp. Speed
Thr diff.
Speed Thr
Fig. 6.s
O
il Recovery Washing
Another function available on Hecu CO2 to assist oil return to the
compressor involves washing the evaporators.
This function uses serial
communication between Hecu
C
O
2 and the MP
X
PR
O
controllers,
and the electronic expansion valves on the evaporators
. The oil
recovery washing function sets the superheat set point to 0K for a
settable time t1 [default 3 minutes] in order to retrieve the oil spread
along the refrigerant circuit; the valve will thus open further, “washing”
the evaporator and fl ushing the accumulated oil back the compressor.
Note
: to make this function more eff ective, the electronic expansion
valve on the evaporator opens fully at the start of the recovery washing
cycle and then its position is controlled automatically based on the new
superheat set point.
td is the time at the end of a washing cycle for which compressor speed
remains fi xed, and valve opening returns to the same position as prior
to activation of the function [default 2 minutes]. If this value is set to 0,
at the end of a washing cycle the system will restart without overriding
compressor speed and keeping the valve at the previous opening
position for a set time. During a washing cycle, the following conditions
are set:
•
Oil recovery washing: ON
•
Smooth Line: OFF
•
P3: 0K
•
P7: -10K
•
St: -50°C
Summary of Contents for Hecu CO2
Page 2: ......
Page 4: ...4 ENG Hecu CO2 0300085EN rel 2 2 07 05 2019...
Page 6: ......
Page 61: ...61 ENG Hecu CO2 0300085EN rel 2 2 07 05 2019 9 2 Software revision history New version 3 0 012...
Page 62: ...62 ENG Hecu CO2 0300085EN rel 2 2 07 05 2019 Notes...
Page 63: ......