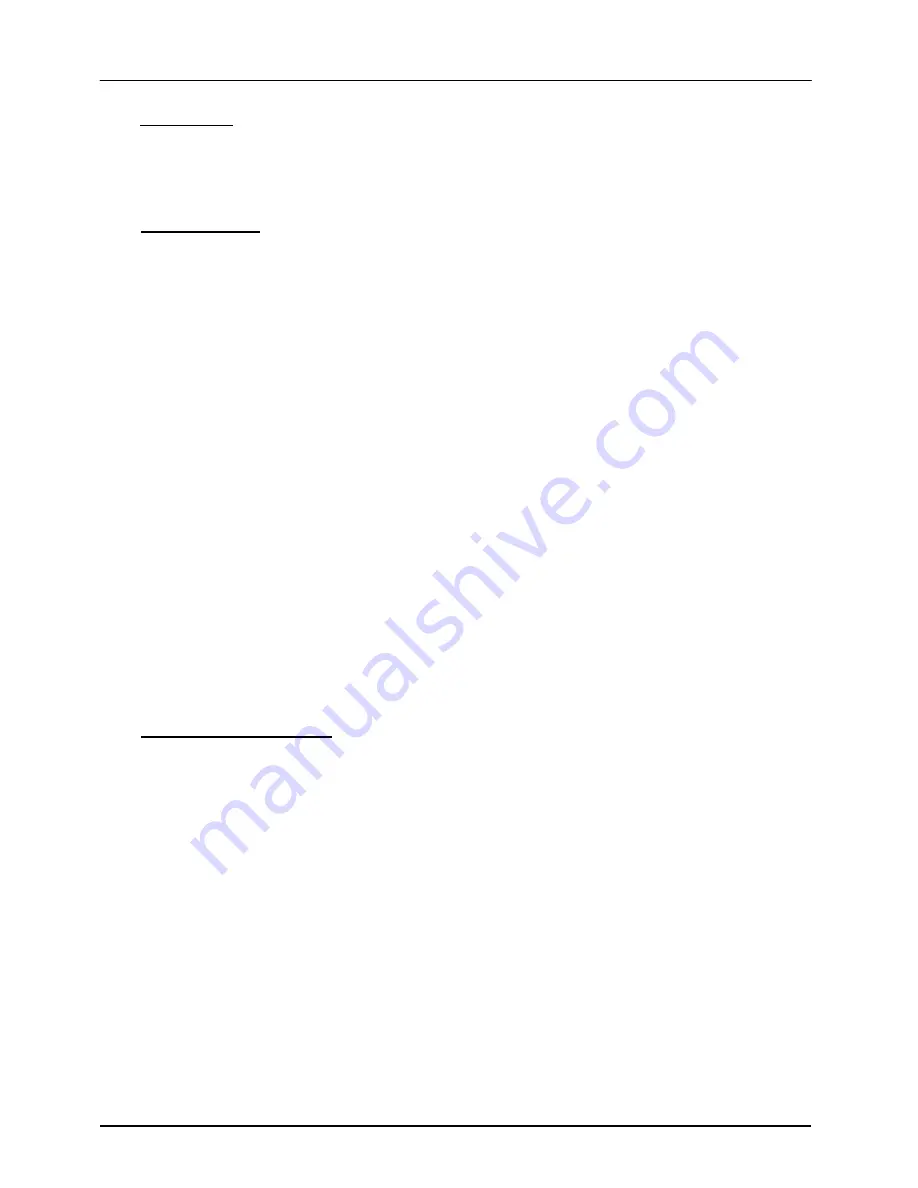
1700-1800°
Chamber
O
PERATION
The instructions for operating the temperature controller are given in a separate manual.
If the furnace is fitted with a time switch, see also the supplementary manual MS03.
If cascade control is fitted, see the supplementary manual MS07.
3.1
Operating Cycle
The furnace is fitted with a combined Supply light and Instrument switch. The light is on
whenever the furnace is connected to the supply. The switch cuts off power to the controllers and
contactor.
Connect the furnace to the electrical supply. The Supply light should glow and the cooling fans
automatically operate.
Electric door models
: before switching on the control instrumentation, check the door switch for
correct operation. The spring return switch stops the door in any position, but over-travel is
automatically limited. Load the furnace and close the door.
Manual door models
: observe the warning in 2.1 about gentle operation of the door.
Operate the instrument switch to activate the temperature controller; the
O
position is off, the
I
position on. The controller becomes illuminated and goes through a short test cycle.
Close the furnace door and adjust the temperature controller – see the controller manual.
Set the overtemperature controller to a temperature a little (say 15°C) above the maximum
setpoint of program temperature, according to the instructions in the appropriate manual.
Unless a time switch is fitted and is off, the furnace starts to heat up. The Heat light glows brightly
at first, more dimly as the furnace temperature approaches a program setpoint.
If the overtemperature trip operates then an indicator or message in the overtemperature controller
flashes, and the heating elements are isolated. Find and correct the cause before resetting the
overtemperature controller according to the instructions supplied.
To switch the furnace off, set the Instrument switch to off. The case cooling fans remain on and
the chamber can be unloaded. Leave the fans on until the furnace cools to below 300°C. If the
furnace is to be left off, isolate it from the electrical supply.
3.2
General Operating Advice
Heating element life is shortened by use at temperatures close to maximum. Do not leave the
furnace at high temperature when not required. The maximum temperature is shown on the
furnace rating label and on the back page of this manual. The furnace can be cycled between room
temperature and maximum without a detrimental effect on element life.
On first installing the elements, and on subsequent element replacement, run the furnace at
1500°C for an hour to create a protective glaze on the element surface.
When heating large objects, in particular poor conductors, avoid shielding the thermocouple from
the heating elements. The thermocouple is intended to sense the temperature near the heating
element, but if a large object is placed in the chamber it may record the average temperature of the
object and the elements, which can lead to overheating of the elements. Allow large objects to
gain heat at a lower temperature and then reset the controller to a temperature close to the desired
maximum.
The furnace elements are very susceptible to mechanical shock. Take great care when loading or
unloading the furnace chamber. If it is necessary to load or unload work at elevated temperatures,
keep the door open for as short a period as possible. The insulation cools quickly and may crack
through thermal shock. Note, though, that the insulation material is susceptible to some surface
cracking arising from high temperature cycling; such cracking is not detrimental to the
performance of the furnace.
MF22
5
Summary of Contents for HTF 18/15
Page 14: ...1700 1800 Chamber 14 MF22...