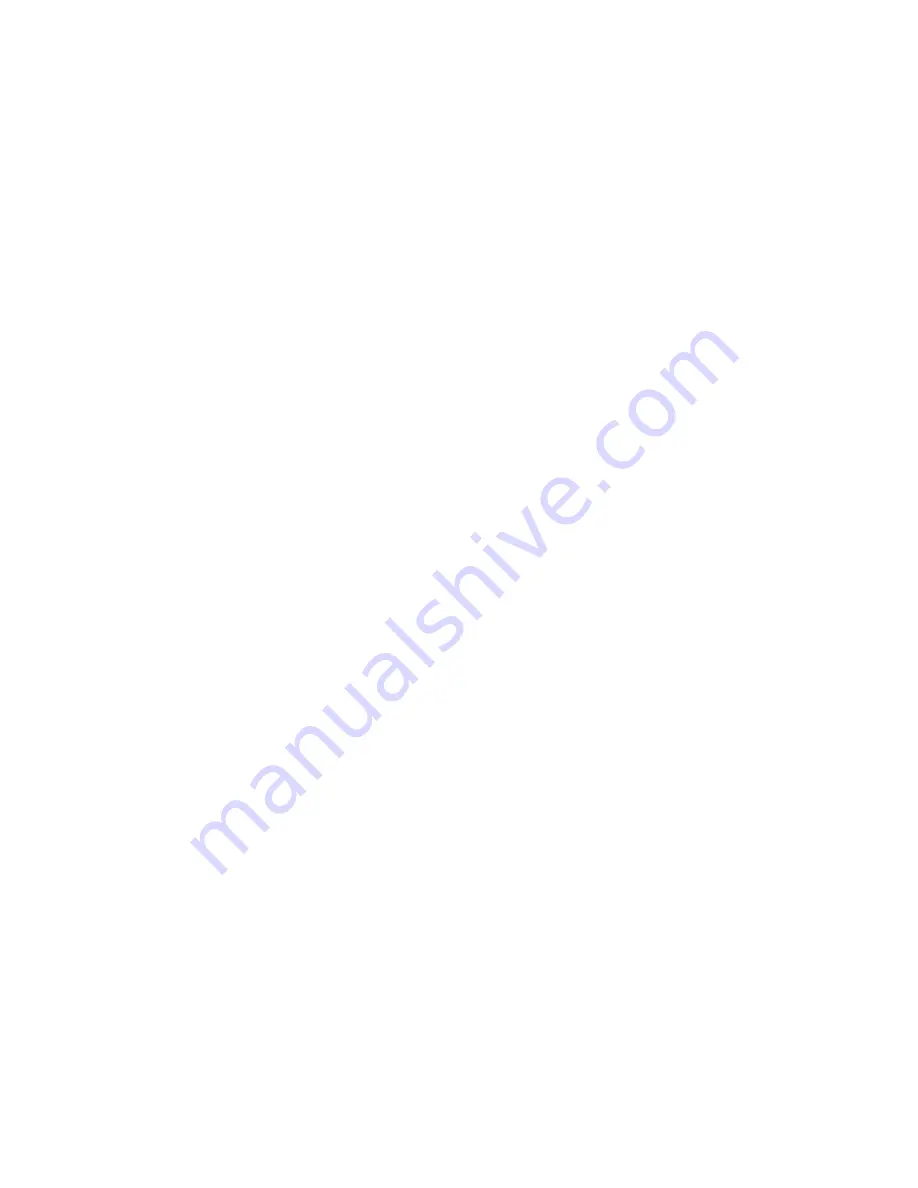
37
Factory Settings
Password to enter factory menu is 1 1 1 1.
Temperature Control
Tempering Sensor
– If “None” is selected, no external tempering thermistor will be connected (External
or Monitor Only
). If “HMI” is selected, the HMI will be used as the tempering sensor. If “Space” is selected,
the space thermistor will be used as the tempering sensor
. If “Return” is selected, the return air thermistor
will be used as the tempering sensor.
Mode Change Tim
– Mode change time is only applicable to heat pumps. This is the time required to
elapse in order to change state (from heating to cooling or cooling to heating). For example, a heat pump
must be off after heating for the duration of this timer in order to reverse the condenser valve and change
to cooling. If the condenser valve is switched rapidly, it will damage the condenser. This timer is intended
to increase the life of the condenser.
Stage Runtimes
Max Runtime
– Maximum time that a stage is required to run before the RTULink will allow a call
for the next stage (if applicable). For example, if stage x has been running for the duration of this
timer, then force stage x+1, if the unit is equipped with a stage x+1. This timer applies to heating
and cooling. This timer is intended to increase efficiency by not allowing a unit to continuously
run while not satisfying set points. The timer is in a MM:SS format and is adjustable from 00:00
to 120:00.
Heating Config
Heat Hysteresis
– The number of degree(s) the tempering stat is allowed to be above the heating set
point before the RTULink stops a call for heating.
Heat Pump
–
This sets the wiring configuration that the RTULink will output to the RTU. Heatpump output
signals Y and O/B are used. Standard output signals Y and W are used.
HP O/B Mode
– For heatpump units, this will set the reversing valve to activate for heating or cooling.
# Heat Stages
– Sets the number of heating stages that are equipped on the RTU.
Heat Differential
– When the number of heat stages is set to greater than 1, the following menus will be
available.
Stage 2
– Second stage heating temperature differential is the number degrees below the
heating set point that the tempering sensor must be to allow a call for the second stage of
heating.
Stage 3
– Third stage heating temperature differential is the number degrees below the heating
set point minus the Heat Diff Stg 2 that the tempering sensor must be to allow a call for the
second stage of heating.
E Heat Type
– If RTULink is selected, RTULink will control the emergency heat with “E” terminal. Only
visible if tempering sensor is configured. If None is selected, the RTU does not have an emergency heat
feature.
E Heat Diff
– Emergency heat differential is the temperature differential from the heating set point in
degrees Fahrenheit at which emergency heat will be activated. For example, if the tempering thermistor
goes below this set point, the RTULink will send an emergency heat signal on the “E” terminal.
Min On Time
– Minimum heat on time is the time that the heating signal is required to be ON before it is
allowed to turn OFF. This timer is intended to reduce heater cycling and increase life cycle of the heating
components. The timer is in a MM:SS format and is adjustable from 00:00 to 20:00.
Min Off Time
– Minimum heat off time is the time that the heating signal is required to be OFF before it is
allowed to turn ON. This timer is intended to reduce heater cycling and increase life cycle of the heating
components. The timer is in a MM:SS format and is adjustable from 00:00 to 20:00.
Summary of Contents for RTULink
Page 2: ...2...
Page 30: ...30 Main Board HMI Menu Tree...
Page 31: ...31...
Page 32: ...32...
Page 33: ...33...
Page 34: ...34...
Page 41: ...41...
Page 42: ...42...
Page 43: ...43...
Page 44: ...44...
Page 52: ...52 APPENDIX C Fixed Dry Bulb Economizer Figure 34 Fixed Dry Bulb Economizer Operation...
Page 53: ...53 Differential Dry Bulb Economizer Figure 35 Differential Dry Bulb Economizer Operation...
Page 54: ...54 Fixed Enthalpy Economizer Figure 36 Fixed Enthalpy Economizer Operation...
Page 55: ...55 Differential Enthalpy Economizer Figure 37 Differential Enthalpy Economizer Operation...