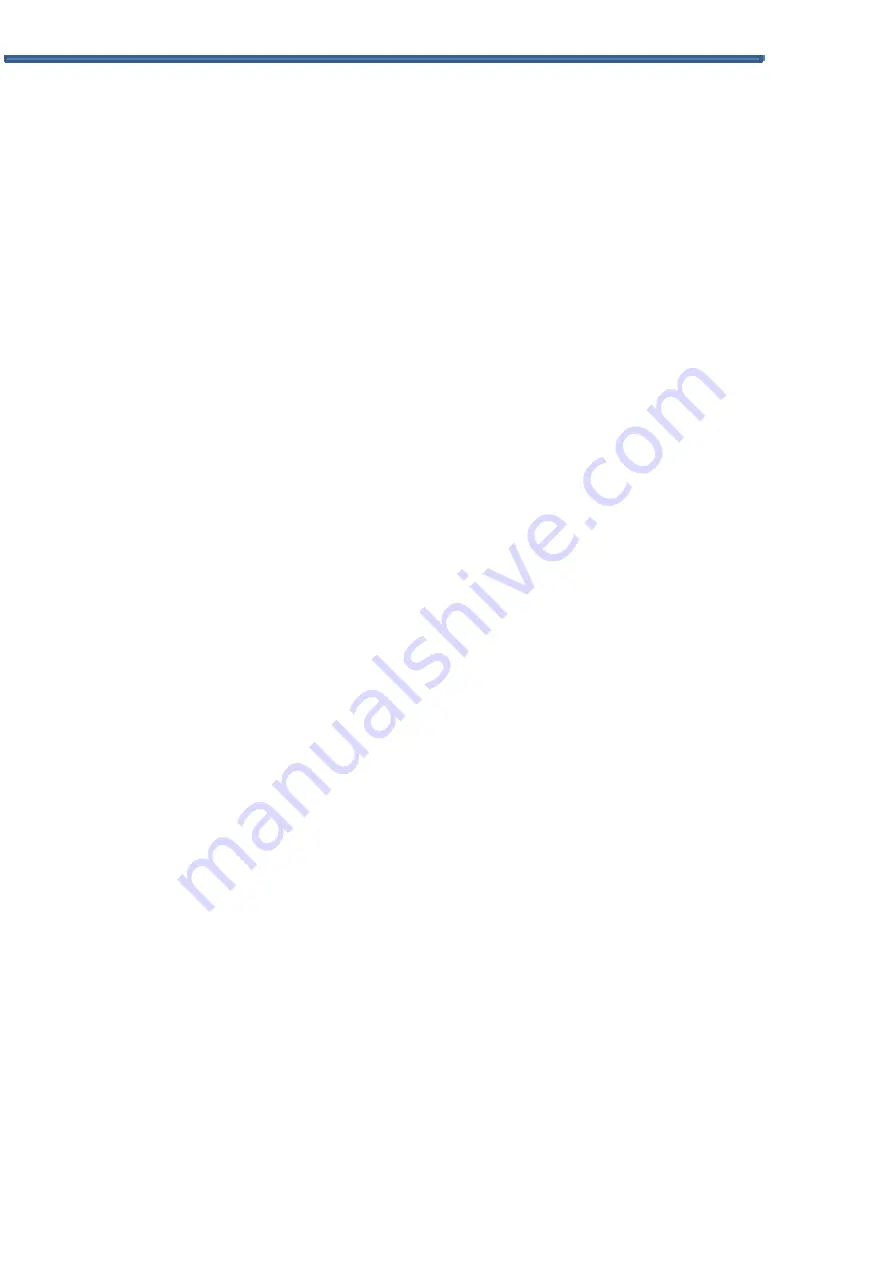
DISASSEMBLY COMPONENT LOCATION
1. Undo the back cover
2. Undo top cover
3. Undo the control panel and PCB
4. Undo the door assembly
5. Undo the front plate
6. Undo the detergent box
7. Undo the inlet valve
8. Undo the pressure switch
9. Undo the drain pump
10. Undo the pulley and motor
11. Undo the absorber pin from the cabinet
12.Undo the drum tub assembly
13. Undo the absorber pin from the drum
14.Undo the heater and NTC
9
DISASSEMBLY COMPONENT LOCATION
Summary of Contents for WDI3300
Page 1: ...Service Manual Washer Dryer Model WDI3300 ...
Page 36: ...10 SERVICE TOOLS ...