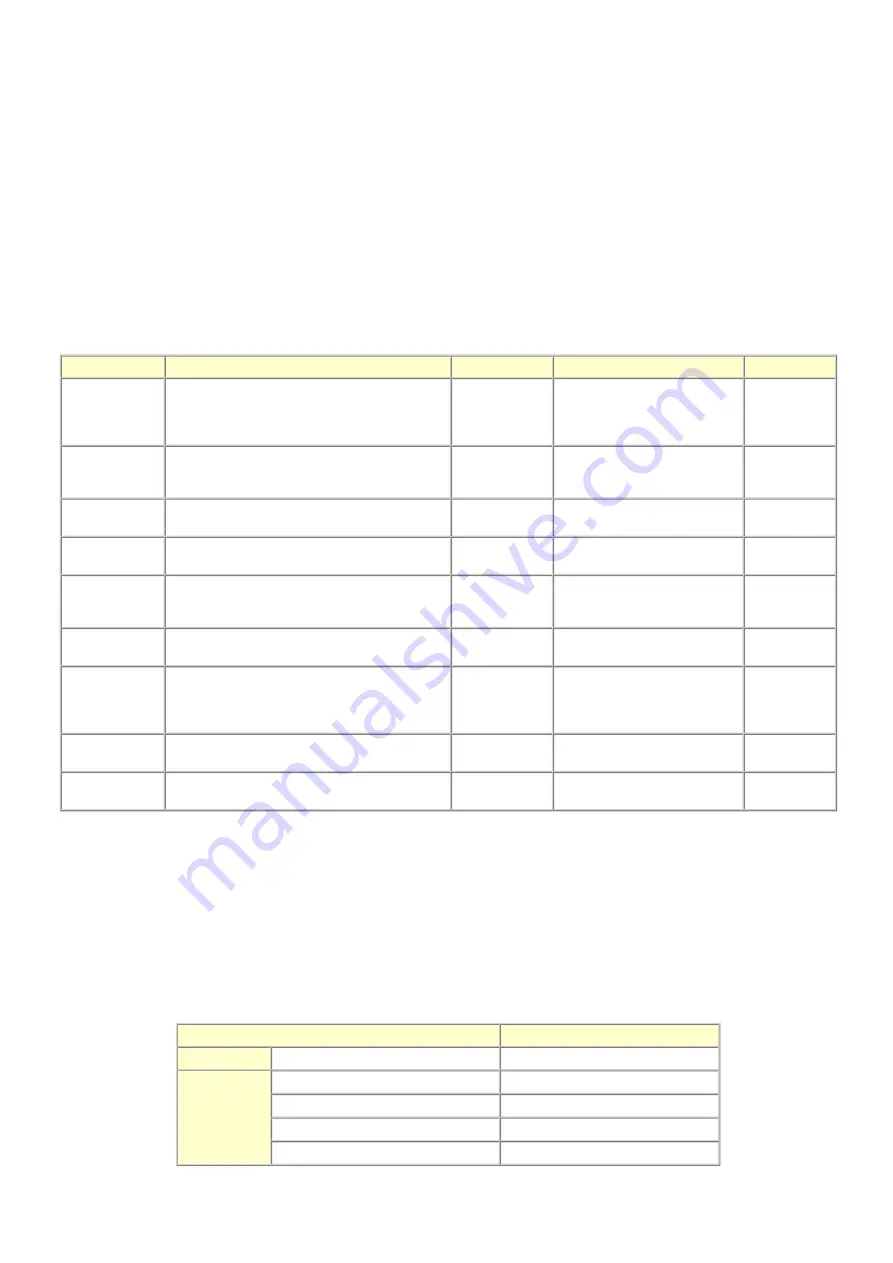
(2) Periodic maintenance
No periodic maintenance is necessary.
(3) Periodic replacement parts
There are no parts in this machine that require periodic replacement by a service engineer.
(4) Replacement consumables
There are no consumables that require replacement by a service engineer.
1-2. Customer Maintenance
1-3. Product Life
(1) Machine
Specified print volume (I) or the years of use (II), whichever comes first.
(I) Print volume: 24,000 pages
(II) Years of use: 5 years of use
Adjustment
Timing
Purpose
Tool
Approx. time
Automatic print
head alignment
- At print head replacement
- When print quality is not satisfying (uneven printing,
etc.)
To ensure accurate
dot placement.
- Machine buttons
- Matte Photo Paper (MP-101) for the
MP810
- Computer (MP driver)
MP810: 13 min.
(Use MP-101.)
MP960: 6 min.
Manual print head
alignment
- At print head replacement
- When print quality is not satisfying (uneven printing,
etc.)
To ensure accurate
dot placement.
- Machine buttons
- Computer (MP driver)
MP810: 15 min.
MP960: 6 min.
Print head cleaning
When print quality is not satisfying.
To improve nozzle
conditions.
- Machine buttons
- Computer (MP driver)
1 min.
Print head deep
cleaning
When print quality is not satisfying, and not improved by
print head cleaning.
To improve nozzle
conditions.
- Machine buttons
- Computer (MP driver)
2 min.
Ink tank
replacement
When an ink tank becomes empty. ("No ink error"
displayed on the monitor or on the machine LCD, or
short flashing of an ink tank LED)
---
---
1 min.
ASF paper feed
roller cleaning
- When paper does not feed properly.
- When the front side of the paper is smeared.
To clean the paper
feed rollers.
- Machine buttons
- Computer (MP driver)
2 min.
ASF sub- roller
cleaning
When the paper fed from the ASF is smeared due to ink
mist attached to the ASF sub-rollers.
To clean the ASF
sub-rollers.
- Machine buttons
See Part 2, 4. FAQ, How to make and
set the ASF sub-roller cleaning sheet,
for details.
1 min.
Bottom plate
cleaning
When the back side of the paper is smeared.
To clean the platen
ribs.
- Machine buttons
- Computer (MP driver)
1 min.
Scanning area
cleaning
When the platen glass or document pressure plate sheet is
dirty.
To clean the platen
glass.
Soft, dry, and clean lint-free cloth.
1 min.
MP810 / MP960
Black
1500 character pattern
11,000 pages
Color
7.5% duty per color pattern
7,200 pages
A4, photo, borderless printing
500 pages
4 x 6, photo, borderless printing
4,300 pages
Postcard, photo, borderless printing
1,000 pages
1-2