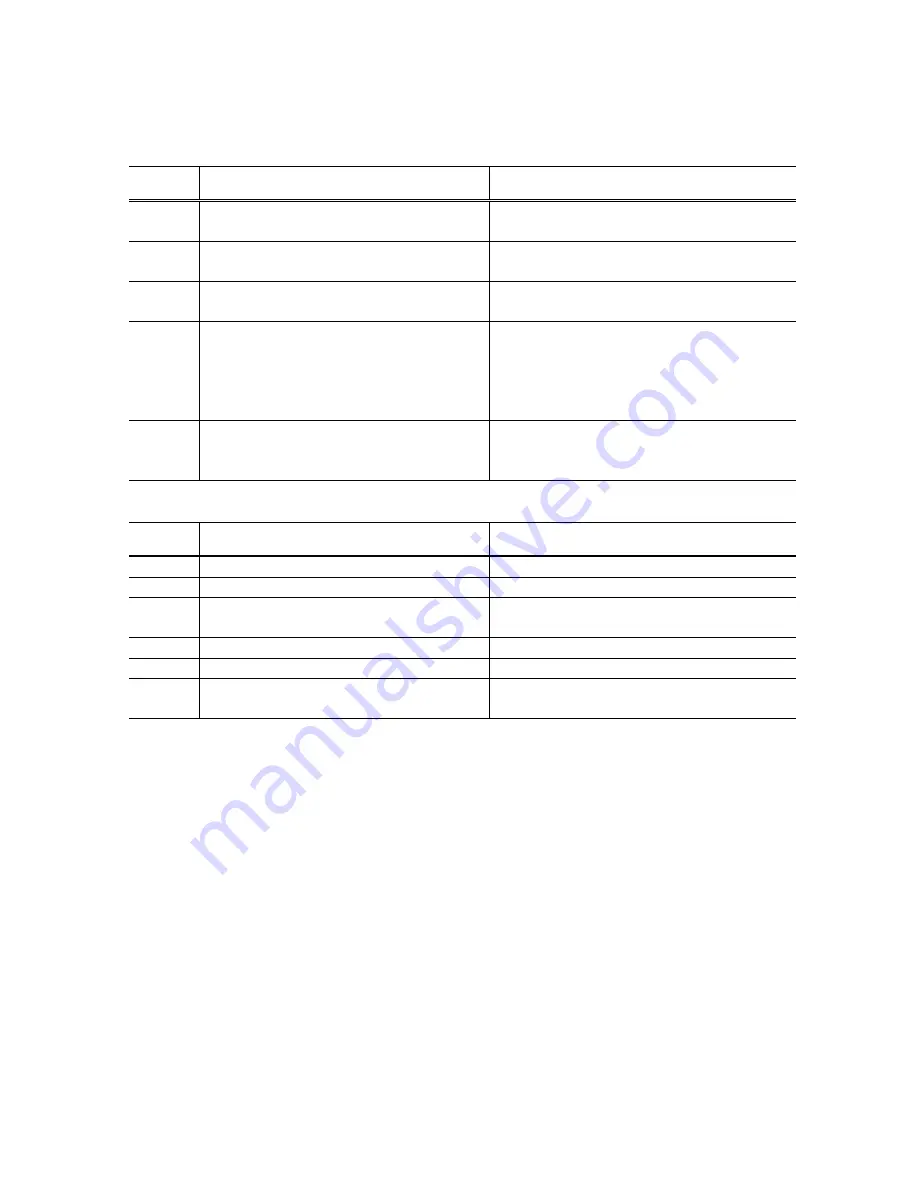
5
3. ERROR DISPLAY
Errors are displayed by the LEDs, and ink low warnings are displayed by the Status Monitor.
3-1. Operator Call Error (LED Blinking in Orange)
LED
blinking
Error Corrective
action
2 times
Paper out
Set paper, and press the Resume/Cancel
button to feed the paper.
3 times
Paper jam
Remove the jammed paper, and press the
Resume/Cancel button.
4 times
Ink tank not installed
Re-install the ink tanks, and close the access
cover.
5 times
Print head not installed or failure has
occurred in the print head.
(Non-supported print head (see page 4) is
installed or print head EEPROM data is
abnormal.)
Install the print head, and close the access
cover. Or, confirm the print head is
“QY6-0044-000” and perform re-installation. If
not recovered with the print head installed,
power the printer off and on.
8 times
Waste ink absorber full or platen waste ink
absorber full warning (approx. 95% of the
maximum capacity)
Pressing the Resume/Cancel button will exit
the error, and enable printing.
3-2. Service Call Error (LED Blinking in Orange and Green Alternately)
LED
blinking
Error Corrective
Action
2 times
Carriage error
Replace the printer as it has failed.
6 times
Internal temperature error
Replace the printer as it has failed.
7 times
Waste ink absorber full or platen waste ink
absorber full
Replace the printer as it has failed.
8 times
Print head temperature rise error
Replace the printer as it has failed.
9 times
EEPROM error
Replace the printer as it has failed.
10 times No print head detected excepting print head
replacement (during printing)
Replace the printer as it has failed.