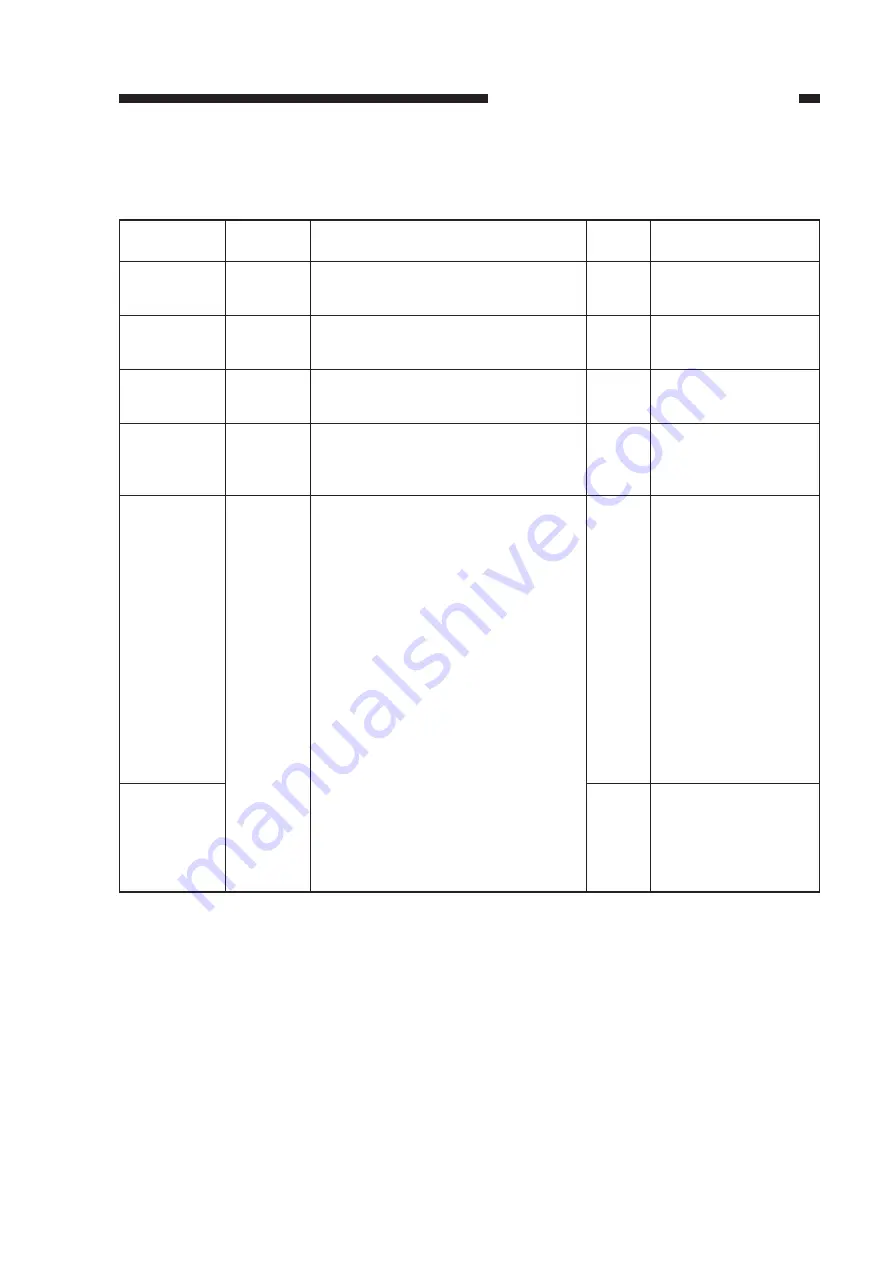
CHAPTER 4 IMAGE TROUBLESHOOTING
4-7
4.
Uneven density (front side dark)
5.
Uneven density (front side light)
Cause/Problem
area
Primary
corona wire
height
Developing
assembly
Dirt on the
scanner
Pre-exposure
lamp unit
Developing
assembly
Corona as-
sembly and
copy paper
Action
End.
Check the pressure ap-
plying mechanism of the
developing assembly.
End.
1.Replace the pre-expo-
sure lamp unit.
2.Replace the DC con-
troller PCB.
1.Clean the edge of the
blade of the develop-
ing assembly.
2.If the problem is in the
black developing as-
sembly, wipe the sur-
face of the developing
cylinder with a dry
cloth.
3.If the problem is in the
CT unit, try putting the
CT unit in the storage
box and shaking it vig-
orously. If the image
does not improve, re-
place the CT unit
1.Clean all the corona
wires once more; then
recheck the position of
each corona wire.
2.Try changing the copy
paper.
Result
Yes
No
Yes
No
No
Yes
Check
Does the image quality improve after the
basic adjustment procedure is followed?
Is the spacer roller of the developing as-
sembly pressing against the photosensitive
drum?
Does the image improve after the scanning
lamp, reflectors, side reflectors, lens and
dust-proofing glass are cleaned?
Does the pre-exposure lamp go ON during
copying?
Is the surface of the developing cylinder
coated uniformly with toner density?
Procedure
1
2
3
4
5