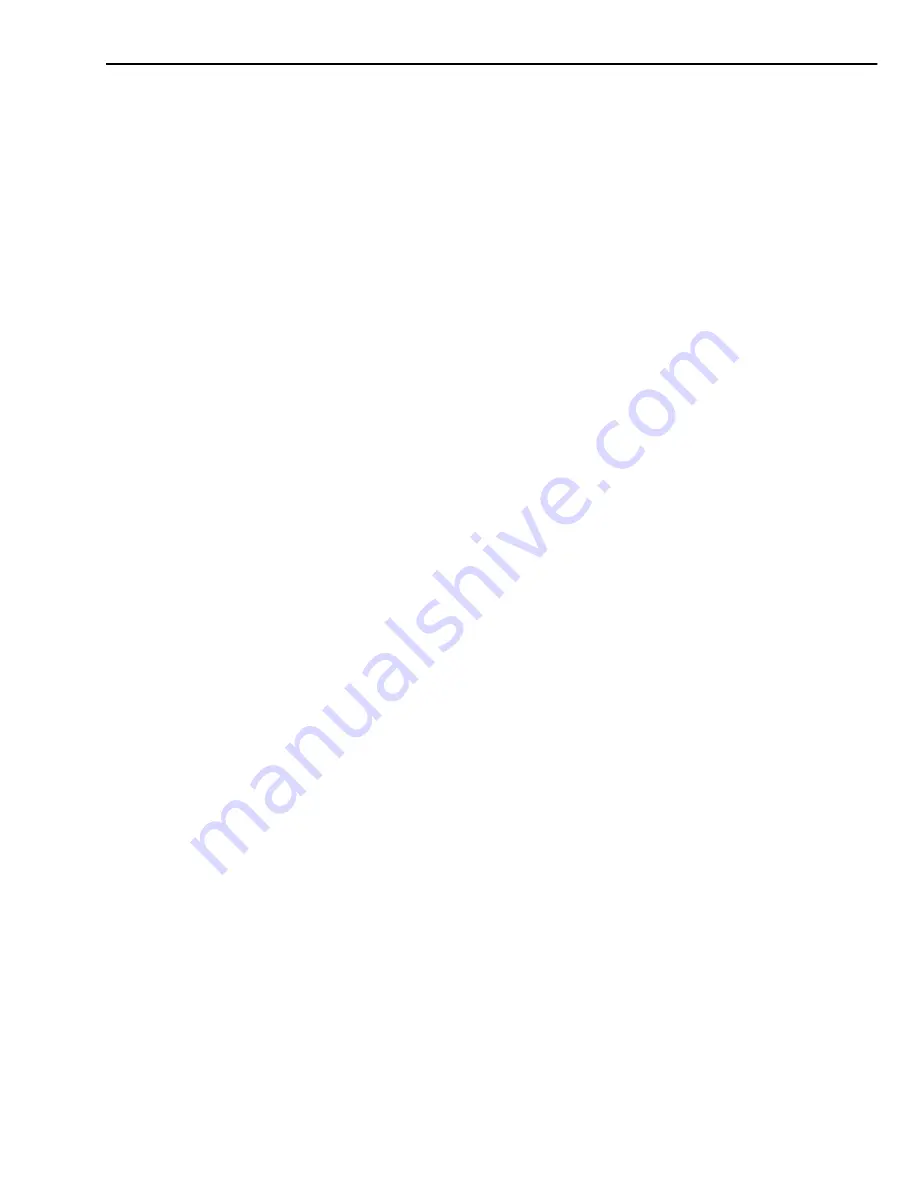
Action: Check whether any gears are worn or missing.
3. The fixing entrance guide is dirty, damaged, or clogged with toner.
Action: Clean the guide.
4. The fixing separation guide is dirty, damaged, or clogged with toner.
Action: Clean the guide.
5. The fixing separation claw is worn or damaged.
Action: Replace the claw.
6. The upper or fixing lower roller is deformed or damaged.
Action: Replace deformed or damaged rollers.
7. The nip width of the fixing lower unit is not correct.
Action: Replace the fixing unit.
8. The fixing unit delivery sensor arm does not move smoothly or is damaged.
Action: Adjust the arm so that it moves smoothly. If it is damaged, replace it.
9. The fixing unit delivery roller is worn.
Action: Replace the fixing unit delivery roller.
10. The fixing unit delivery roller does not rotate smoothly.
Action: Check whether any gears are worn or missing.
11. The face-down delivery roller does not rotate smoothly.
Action: Check whether any gears are worn or missing.
J-3 Duplexing Unit
<Possible causes>
1. Foreign matter is adhering to the feed guide or it is burred.
Action: Remove any foreign matter. If the guide is burred, replace it.
2. The switchback roller, feed roller, or duplex feed roller is worn or deformed.
Action: Replace worn or deformed rollers.
3. Paper dust or dirt is adhering to rollers.
Action: Remove the paper dust or dirt.
4. Gears are worn or damaged.
Action: Replace any worn or damaged gears.
5. Sensor arms do not move smoothly or are damaged.
Action: Adjust the arm so that they move smoothly. If damaged, replace them.
6. Duplexing unit sensors are defective.
Action: Check the state of each sensor using the printer driver tester. Replace any defective
sensors.
CHAPTER 4
4 - 53
Summary of Contents for LBP 2460 - B/W Laser Printer
Page 4: ......
Page 10: ......
Page 12: ......
Page 14: ...This page intentionally left blank CHAPTER 1 1 2 ...
Page 44: ...CHAPTER 1 1 32 ...
Page 46: ......
Page 63: ...This page intentionally left blank CHAPTER 2 2 17 ...
Page 77: ...This page intentionally left blank CHAPTER 2 2 31 ...
Page 105: ...This page intentionally left blank CHAPTER 2 2 59 ...
Page 142: ......
Page 212: ...CHAPTER 3 3 70 ...
Page 214: ......
Page 271: ...This page intentionally left blank CHAPTER 4 4 57 ...
Page 276: ...Figure 4 8 3 CHAPTER 4 4 62 PS35 PS33 PS31 PS32 PS34 ...
Page 278: ...C Clutches and Solenoids Figure 4 8 4 CHAPTER 4 4 64 SL22 SL21 CL21 SL3 SL1 CL1 CL3 CL2 SL2 ...
Page 282: ...E PC Boards Figure 4 8 8 CHAPTER 4 4 68 7 8 6 6 3 4 2 1 5 ...
Page 297: ...APPENDIX I GENERAL TIMING CHART A 1 II GENERAL CIRCUIT DIAGRAM A 3 III LIST OF SIGNALS A 7 ...
Page 298: ......
Page 304: ...APPENDIX A 6 ...