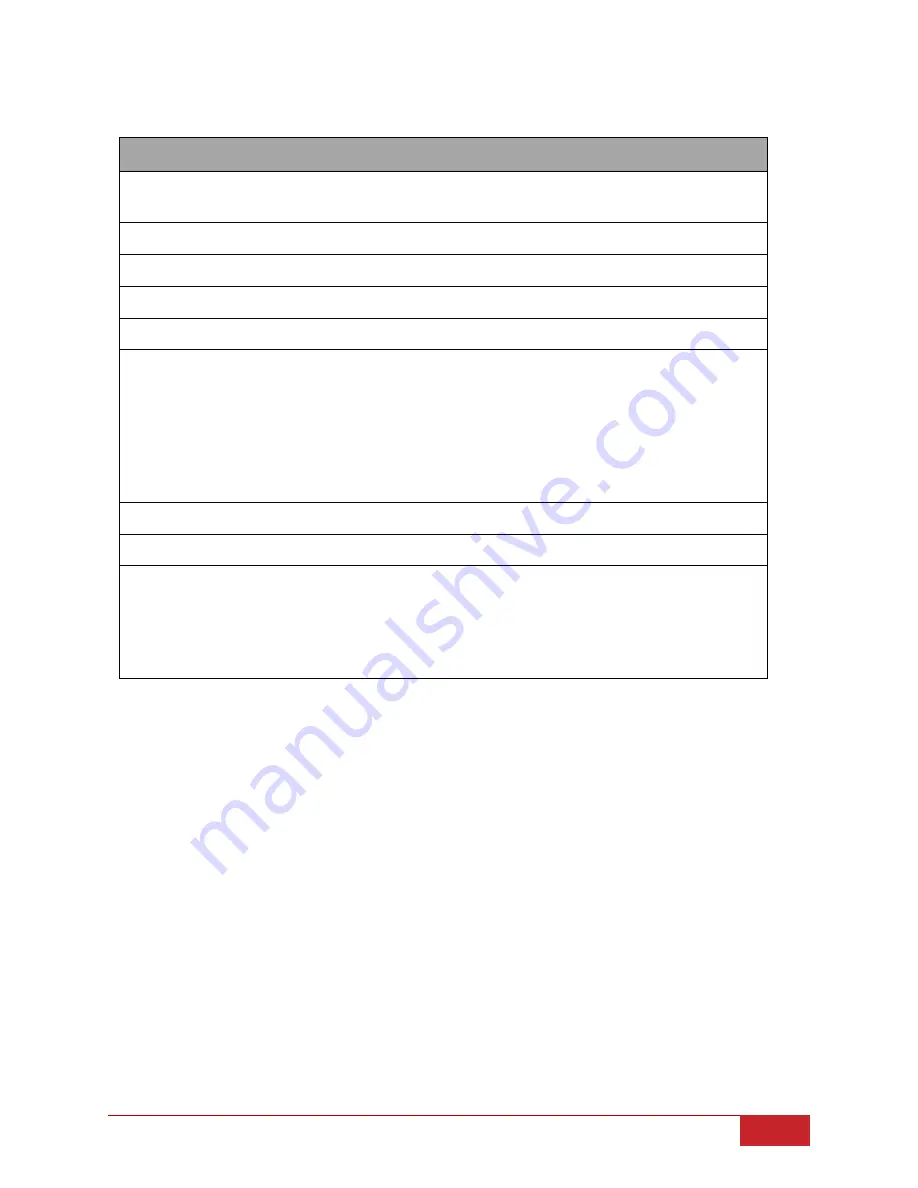
CANNON Instrument Company® | Advanced Setup
45
Table 23 — Method Settings: Test
Parameter name
Description
Wet Tube
Runs an initial, unrecorded sample drop to coat the inside of
the tube with the sample material.
Soak Time Units
Time unit in seconds, minutes, or hours
Bulb1 Soak Time
Time to thermal soak a sample that draws only into bulb 1.
Bulb2 Soak Time
Time to thermal soak a sample that draws only into bulb 2.
Bulb3 Soak Time
Time to thermal soak a sample that draws only into bulb 3.
Preheat Type
No preheat
Minimum preheat
starts the preheat cycle as soon as the
previous sample begins running and runs for at least the set
preheat time.
Serialized preheat
starts the preheat cycle after the
previous sample finishes and runs for exactly the set preheat
time.
Minimum Preheat Time
This is the time that the preheater is applied to the sample.
Preheat Temperature Units
Select either Fahrenheit or Celsius.
Preheat Temperature
Fahrenheit: 0 °F to 437 °F; Celsius: 0 °C to 225 °C
The heater temperature is determined by the
Preheat
Temperature
setting of the sample that is in the preheat
position, even if that sample is set to
No preheat
. Set the
temperature to 0 (zero) to turn off the heater.