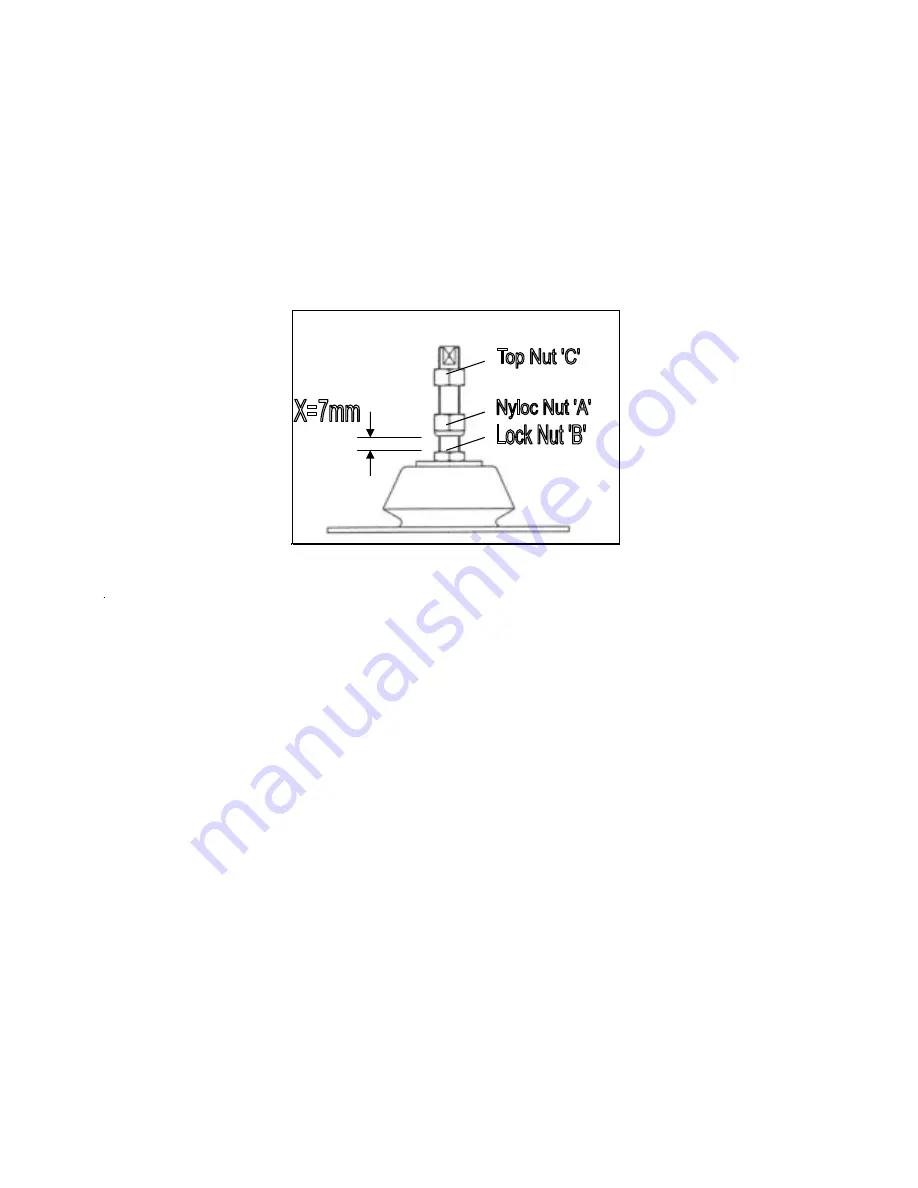
29
Marine Engine Installation Information
Anti vibration Mount Installation
These mounts are supplied for use where accurate alignment is required, e.g.
between the gearbox output shaft and propeller shaft on marine installations.
They also provide isolation of the power unit, to minimise the transmission of
vibration into the hull.
Assembly and adjustment is as below:
T op N ut ‘C ’
N yloc
Nut ‘A’
L
ock
Nut ‘ B’
X =7m m
T op N ut ‘C ’
N yloc
Nut ‘A’
L
ock
Nut ‘ B’
X =7m m
Set the gap ‘X’ between the lower face of the Nyloc Nut ‘A’ and the upper face of
Locknut ‘B’ to 7mm.
1.
Attach each mount to the engine bearers and secure by tightening Top Nut
‘C’
2.
Lower the propulsion unit, complete with mounts onto the beds or support
structure, ensuring that the base of each mounts is fully seated. If any
clearance between the underside of the mounts and beds is found, proceed
as below:
3.
(i)
If the gap is less than 2mm, re-adjust Nyloc Nut ‘A’, until the base of
the mount contacts the bed face.
(ii)
If the gap exceeds 2mm, a separate packing piece / shim should be
fitted.
4.
Fit and tighten the bolts fixing the mounts to the bed. Tighten Top Nut ‘C’.
Alignment between the Gearbox and Propeller Shaft Flanges should now be
checked., preferably using a dial indicator for concentricity and feeler
gauges for angular misalignment (see sketch).
Adjust alignment by raising or lowering the Nyloc Nut ‘A’, to achieve
alignment within the limits of the Gearbox to Propeller Shaft Coupling, as
specified by the manufacturer. If a rigid coupling is used, then it is
suggested that eccentricity should not exceed 0.25mm (0.010”) total
indicator reading and, angular misalignment should be within 0.025mm
(0.001”) per 25mm of flange diameter.