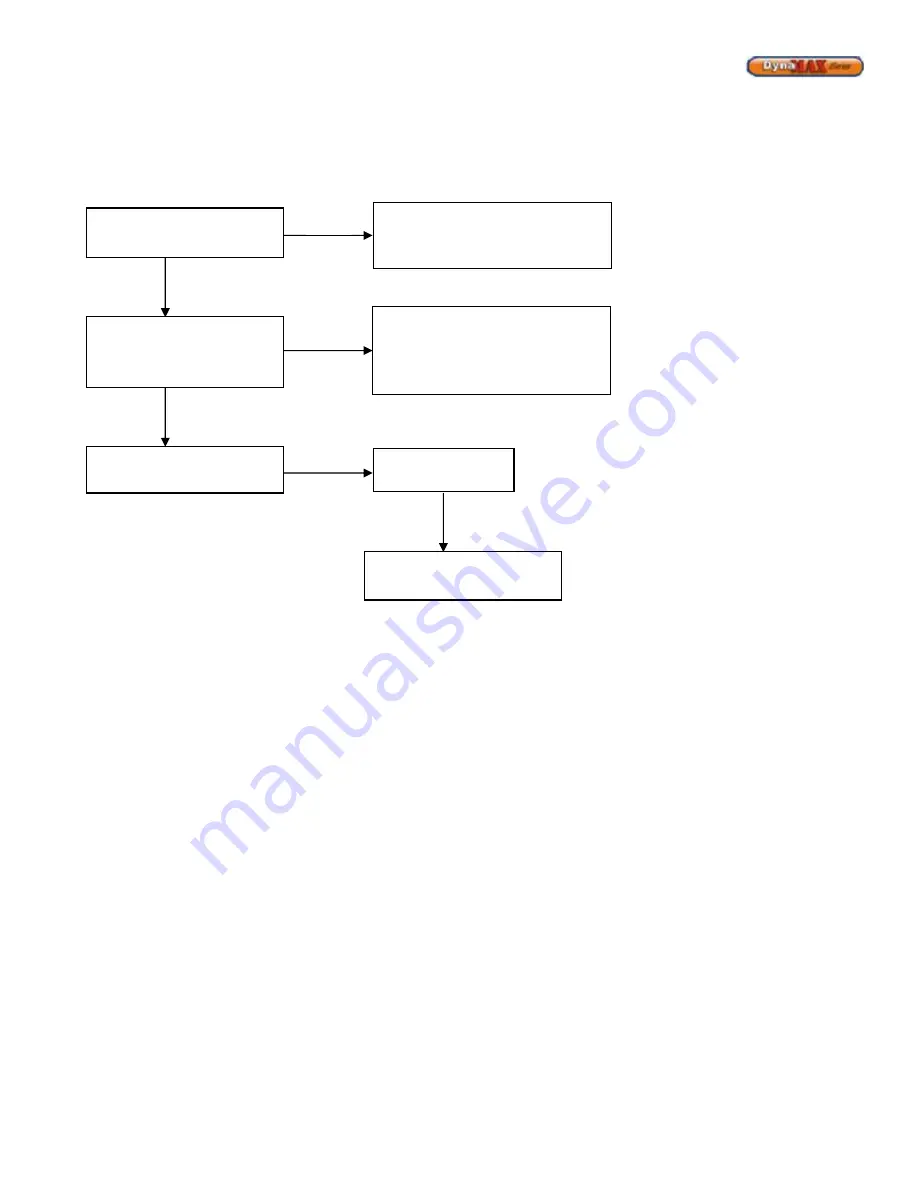
46
Alert 291: Abnormal Recycle: Flame was not on at end of ignition
Alert 294: Abnormal Recycle: Flame was lost during Run
Alert 324: Abnormal Recycle: Hardware flame bias
Alert 377: Abnormal Recycle: Hardware flame bias delta
This type of failure indicates a flame rectification signal issue through the flame rod.
Is Flame sensor plug secure?
NO
Fasten flame sensor plug securely to
flame sensor wire and check for
corrosion deposits at wire terminals
YES
Check continuity of flame
sensor wire from flame sensor
to ignition control, J1-2
NO
YES
Remove flame sensor and clean
if necessary
NO
Bend flame sensor
closer to burner
NO
Replace flame sensor and
graphite flame sensor gasket
Replace sensor wire since corrosion
can affect the perceived flame signal
significantly and position it away from
the heat exchanger
Summary of Contents for DynaMax DMH201
Page 2: ......
Page 70: ...62 PART 14 EXPLODED VIEW PARTS LIST DYNAMAX HS WALL HUNG 10 May be located outside cabinet...
Page 71: ...63 DYNAMAX HS FLOOR MOUNT 10 May be located outside cabinet...
Page 77: ...69 11 6 Front Strut 14 8037 X X Not shown in Exploded View Part Recommended spare parts...
Page 78: ...70 PART 15 ELECTRICAL DIAGRAMS 15 1 DM 200 299 INTERNAL WIRING DIAGRAM...
Page 79: ...71 15 2 DM 399 800 INTERNAL WIRING DIAGRAM...
Page 80: ...72...