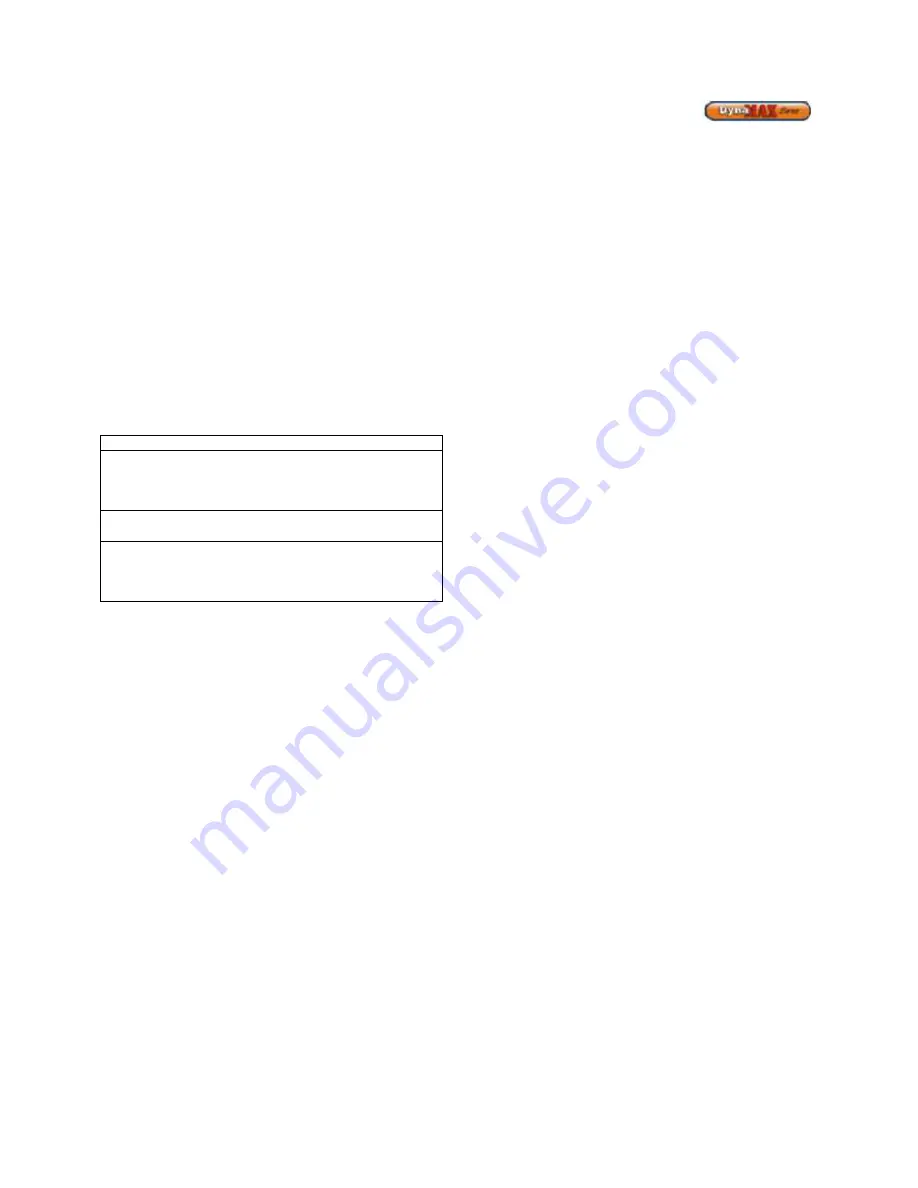
52
12) Brush the heat exchanger with a nylon bristle brush.
DO NOT use a metal brush. Re-vacuum the heat
exchanger.
13) Finish cleaning by wiping down the boiler heating
surfaces with a clean, damp cloth.
14) Rinse out any additional debris with a low pressure
water supply. Start rinsing from the rear of the heat
exchanger and slowly working your way towards the
front of the heat exchanger.
15) Remove the water proof material after cleaning is
complete.
16) Re-install the heat exchanger door by evenly torquing
down the (6) nuts to 3 ft-lbs, burner, igniter and flame
sensor, and fan/ mixing tube assembly. Fasten the
nuts back to the heat exchanger assembly.
17) Re-connect the fan assembly to the boiler mixing tube.
18) Re-connect the condensate hose to the heat
exchanger.
NOTE
All gaskets on disassembled components must be replaced
with new gaskets/sealant on re-assembly, if required.
Gasket kits are available from the factory
CAUTION
When the vent system is disconnected for any reason it
must be reassembled and resealed according to vent
manufacturer’s instruction
9.4
CONDENSATE TREATMENT
Condensate occurs when the products of combustion are
cooled below their dew point in the heat transfer process.
The liquid condensate formed from this high efficiency heat
transfer process is mildly acidic.
•
The condensate will typically have a pH ranging from
4.0 to 5.0 as it is discharged from the condensate drain
of the appliance.
•
The condensate collection box inside each DynaMax
HS where the condensate is collected is constructed of
a non-corrosive material.
•
All materials external to the appliance in contact with
the condensate must be corrosion resistant.
•
Condensate must be able to flow freely from the
appliance. All condensate flow is accomplished by
gravity requiring a minimum downward slope of 1/4”
per foot (21mm/m) to ensure proper flow to a suitable
drain.
•
All condensate piping and connections must be easily
accessible for routine maintenance and inspection.
•
Use solid piping when running condensate line across
the floor.
•
Check neutralized pH level regularly or as required by
local jurisdiction. Replace neutralizer medium as
required.
There are several factors affecting amount of condensation
created by the appliance, however for rough approximation
use.
Condensation Volume, US Gallon/Hr = Input, MBH/1000 x
5.0
Many jurisdictions will require the acidic condensate to be
neutralized before it can be placed in a drain system.
•
A neutralizer, calcium carbonate, to control the pH of
the liquid discharged to a drain system is provided with
every DynaMax HS boiler.
•
As the reservoir fills, it provides an extended residence
time to neutralize the condensate.
•
Residency time in the neutralizer reservoir allows time
for the pH to be raised.
•
Prime the neutralizer reservoir with 1 liter of water.
As the condensate migrates through the reservoir in typical
applications the pH is controlled to a range of 5.5 to 6.0
before exiting the system. Always check with local codes
for specific requirements.
9.5
IGNITER AND FLAME SENSOR
ELECTRODES
The direct spark igniter is to be checked at every service
interval. Clean the direct spark igniter as required to
maintain peak ignition efficiency.
1) Turn off main electrical power to the appliance.
2) Turn off main manual gas shutoff to the appliance.
3)
Locate the direct spark igniter and flame sensor.
4)
Disconnect the power lead to the direct spark
igniter and flame sensor
5) Loosen and remove the two (2) torx screws that
hold the igniter and flame sensor to the heat
exchanger flange.
6) Pull the igniter horizontally out of the heat
exchanger flange. Use care, do not hit or break
the igniter leads.
7) Remove any debris that has accumulated on the
electrodes using steel wool. If the electrodes
cannot be cleaned to their original appearance,
replacements are needed. Do not use sand-paper
since this will contaminate the surface.
8) Check that the igniter and flame sensor gaskets
are still in good condition (no tears or seams). If
the gaskets are in good condition the electrodes
can be re-installed back to the heat exchanger
flange.
9) Check that the igniter gap is 9/64”.
9.6
CHECK IGNITER GROUND WIRING
1) Inspect boiler ground wire from the heat
exchanger flange to ground on boiler. Check boiler
ground wire continuity.
2) Verify that all wiring is in good condition and is
securely anchored.
9.7
BURNER MAINTENANCE
The burner should be removed for inspection and cleaning
Summary of Contents for DynaMax DMH081
Page 2: ......
Page 68: ...65 PART 14 EXPLODED VIEW PARTS LIST DYNAMAX HS WALL HUNG...
Page 69: ...66 DYNAMAX HS FLOOR MOUNT...
Page 76: ...73 PART 15 ELECTRICAL DIAGRAMS 15 1 DM 80 299 INTERNAL WIRING DIAGRAM...
Page 77: ...74 15 2 DM 399 800 INTERNAL WIRING DIAGRAM...
Page 78: ...75...