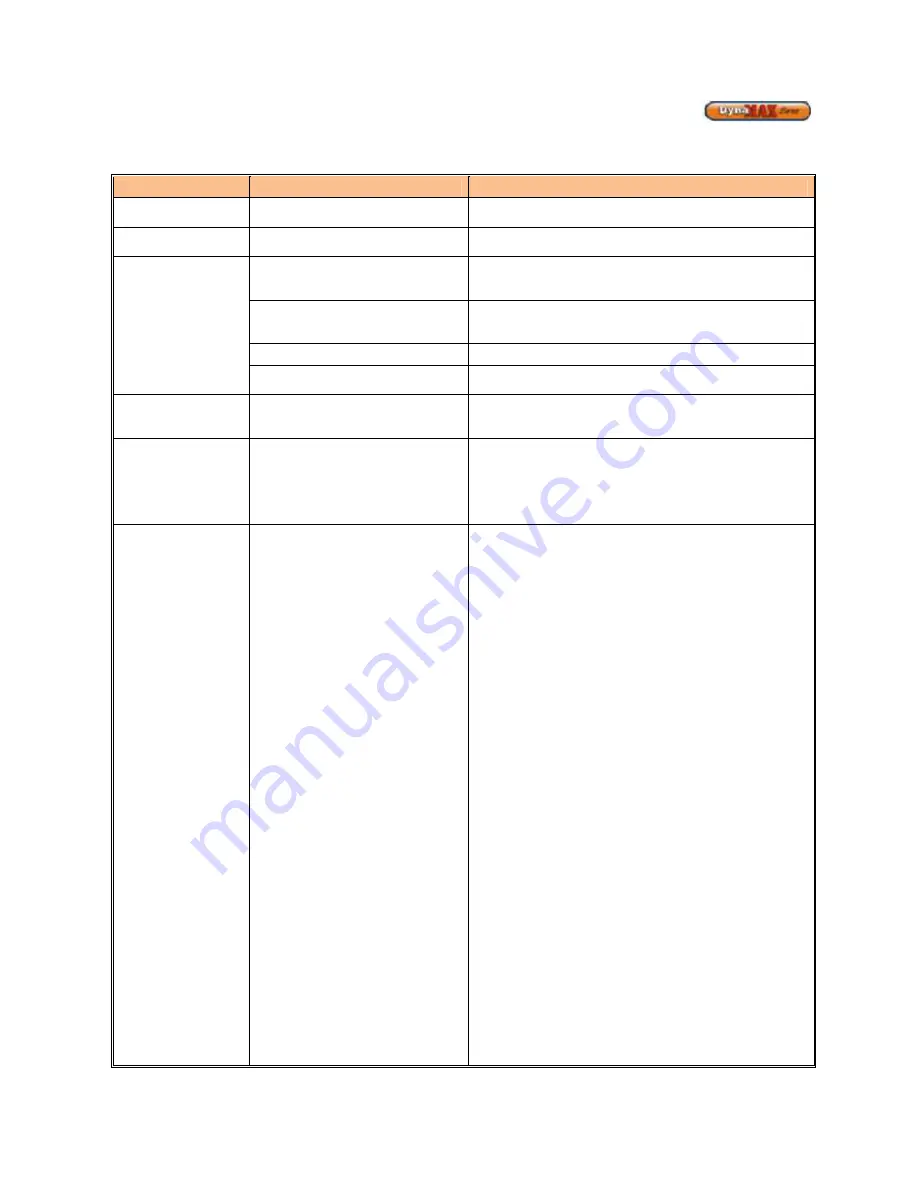
40
PART 8
TROUBLESHOOTING
Table 18: Troubleshooting Table
COMPONENT
FAILURE MODE
ANALYSIS
Incoming Power
• Two wires interchanged
• No effect on safety
• Live and Neutral wires are interchanged.
Transformer Tripped
• The 24Volts and 120 Volts wired
are interchanged
• Transformer immediately burns out, replace transformer
Pump Fails to
Circulate
• Wiring Issue
• Check that wires are correctly wired from the DynaMax HS
Controller to the pump delay relay.
• Check that 115V is delivered to pump coil.
• Faulty Pump on a wet rotor pump
• Pump impeller may be stuck. Use a flat head screwdriver
on face of pump to turn impeller manually
• Replace Pump
• Air in the piping system
• Purge all air from the piping system
• Internal Fault on DynaMax HS
Controller
• Replace DynaMax HS Controller
Relief Valve
• System pressure exceeds relief
valve setting
• Replace the standard relief valve with a higher rated valve
up to the maximum pressure of the heat exchanger.
Improperly sized expansion tank.
Flow Proving
Device/ LWCO
• Flow Proving Device/ LWCO
contacts are open
• Verify LED’s on current sensing transformer during a heat
demand (wall hung)
• Check flow switch paddle (floor mount)
• Verify for closed valves or obstructions in boiler piping
• Verify that all air has been purged from the system
• Verify that wiring is correct
Flame Failure
(Pressing the manual
OK button on the
DynaMax HS Control
Panel to restart the
ignition sequence)
• The boiler has failed to ignite the
burner after 3 consecutive
attempts
• Verify that all air has been purged from gas line
• Inspect spark electrode and related wiring for damage and
connection errors
• Verify that the ignition fan speed is set to 3000 RPM
through fan diagnostics screen.
• Verify that boiler is properly grounded
• Verify incoming gas supply pressure and that it coincides
with Table 9.
• Verify that the vent/ air inlet piping (if equipped) are
correctly installed and obstructions are not present.
• Check wiring from DynaMax HS Controller, Gas Valve
Transformer and Gas Valve Relay. If a signal cannot be
detected, the DynaMax HS Controller needs to be
replaced
• If 24 VAC is present, check the outlet of the valve to
ensure that gas is flowing. With a manometer connected
to the outlet pressure tap of the gas valve a negative
pressure should be present during pre-purge. When the
valve is energized a change in pressure should occur, if
no change is detected the gas valve has failed to open or
it is passing insufficient amount of gas. If this is an initial
startup increase the low fire gas setting by ¼ turn
clockwise.
• Inspect flame sensor and associated wiring. Replace if
necessary
• Inspect the burner. Refer to Burner Maintenance in section
9.7
• Replace the DynaMax HS Controller